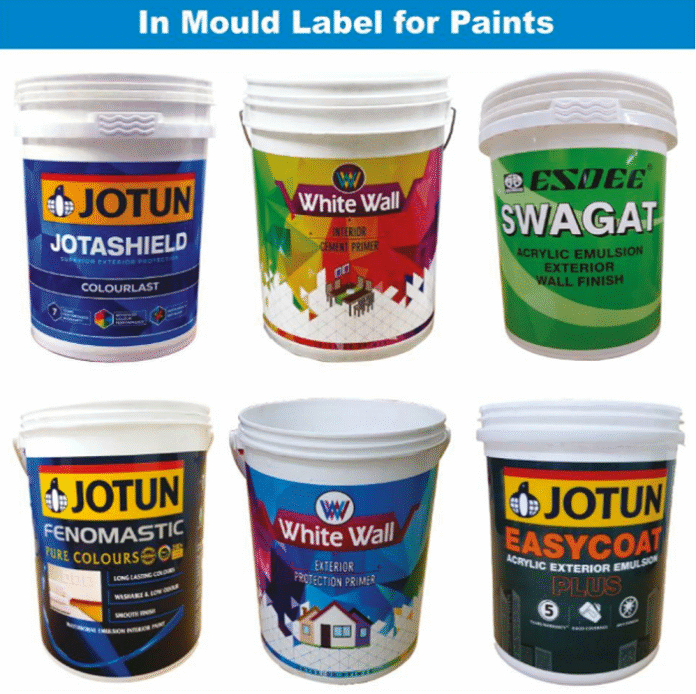
In-mold labels (IML) have caught on in the past decade among brand owners – and especially in the last five years in the Indian rigid container industry. They offer the convenience of durability, ease of manufacturing, and sustainability, as well as a seamless, integrated look, unlike traditional labels that can peel or tear. This process also offers ease of operation by combining decoration and manufacturing in one step, thereby making it cost-effective.
Plastic containers with in-mold labeling are manufactured using two methods: injection molding and blow molding. Although numerous label converters are able to provide in-mold labels, the perceived shortage of injection molding companies in this segment in earlier years seems to have been overcome with molders available in every region of the country, as even smaller local brands are opting for this method of decoration and packaging.
Widely used in tubs for food and beverages (yogurt, ice cream, or butter); industrial pails and containers for paint and chemicals, laundry detergents and fabric softeners; automotive parts; consumer goods such as packaging for electronics, and toys; as well as personal care products such as shampoo bottles, deodorants, soaps and cosmetic tubes – the in-mold labeling process involves placing of pre-printed film labels on a mold before the plastic container is formed.
Decoration and manufacturing are integrated into a single step, which results in a durable, high-quality label that is fused to the container’s surface. IMLs can fit a wide range of container shapes such as round, oval, square, rectangular, ‘sqround’, or special shapes.
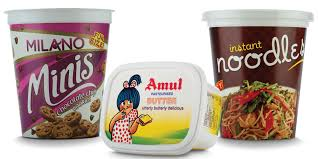
In-mold labels are generally resistant to scratches, scuffs, and chemicals, making them useful for demanding applications. They resist humidity and big temperature changes, making them a practical choice to decorate plastic containers for frozen and refrigerated products, as was shown to us at the Ajanta Arts stand adjacent to the ElitePlus conference on injection and blow molding in Mumbai earlier this month. Another leading supplier of in-mold labels, Mudrika Labels, also had a stand at Elite-Plus. Together with Hyderabad-headquartered Mold-Tek, which not only prints IML labels but also produces the containers by incorporating them, these are three of the significant IML suppliers to the industry.
These labels are usually printed in rolls or sheets on thin films, usually by the gravure or flexo process, although Ajanta has pioneered the printing of IMLs using the UV offset process. Apart from the excellent print quality with detailed and vibrant graphics, with high-resolution colors and images, there is also the flexibility to respond to creative design ideas using flat, curved, or 3D-formed graphics. Ajanta showed us containers with dazzling metallic effects as well as those used for frozen and cold chain products, where normal pre-sensitized labels would likely shrivel or peel off.
Most often, the process uses polypropylene (PP) for both the container and label, making it a mono-material packaging and allowing for easy recycling. High-density polyethylene (HDPE) is also used for auto lubricant containers. Unlike traditional methods of pressure-sensitive labeling that require adhesives not generally conducive for recycling, in the IML process, the container and the label are combined without the exterior glue.
The in-mold and container manufacturing process
“In-mold labels are applied to a container during the manufacturing process. A pre-printed label is placed in the mold, and the label becomes an integral part of the finished item, with no requirement for label application equipment on the filling line.
Blow molding – In-mold labeling (IML) is carried out on blow moldings such as polyethylene and polypropylene containers or bottles. The label substrate can be paper, in which case it is coated with a heat-sensitive adhesive, or films such as polypropylene, which fuse directly to the blow-molded container.
Injection molding – In-mold labeling of injection moldings most commonly uses film labels, which are placed into the injection mold. The molten plastic is injected and the label fuses to the component surface. Good, all-round decoration can be obtained using this method, which is currently used for tubs for butter and margarine, and for large containers for biscuits. A similar process exists for in-mold labeling during thermoforming.
The pre-printed and die-cut labels are delivered to the molder in stacks and are usually picked up and placed automatically into the mold during the opening cycle. Accuracy of label placement in the mold is critical for good finished effects. Large surface areas can labeled with excellent adhesion and resistance to scuffing.”
– The explanatory paragraphs on the manufacturing process are a slightly edited excerpt from an article by AR White of AWA Consulting, UK, in Science Direct.