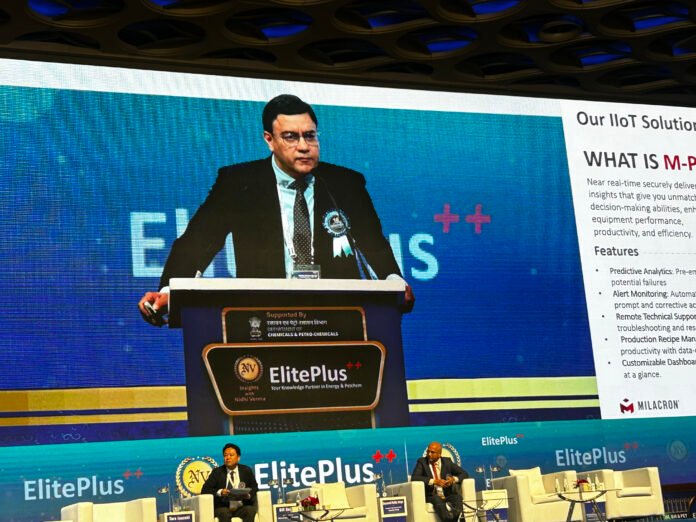
Several injection and blow molding machine manufacturers, mold makers, and polymer and additive suppliers spoke at Elite, highlighting their innovations in terms of scaling, energy, and material saving. I hope to cover several in detail in future issues, but here is my brief report on Milacron, which is based in Ahmedabad and is a significant supplier to the Indian market.
Milacron’s presentation, actually, showed innovations not just in rigid packaging but in several other areas where plastic injection provides a multiplicity of components and products. One might say that reducing cycle time and the use of recycled polymers in injection molding was an important theme of the conference.
Milacron India marked its 30-year milestone at the 10th ElitePlus Injection, Blow Moulding and PET Conference. Addressing the audience, managing director Bill Shukla reflected on the company’s journey from launching five machines in 1995 to becoming a leader in injection molding innovation.
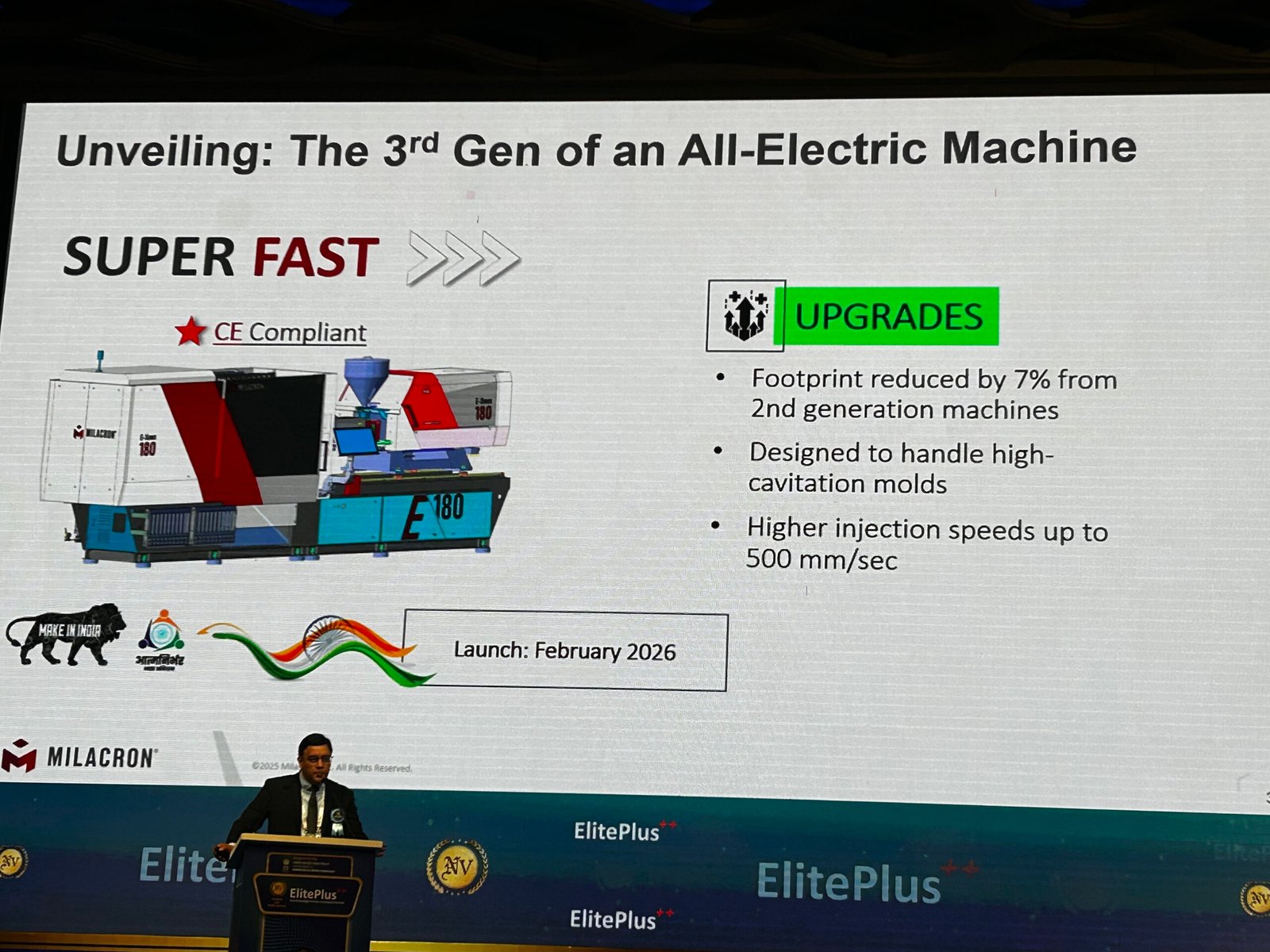
He said that Milacron India has delivered over 20,000 machines, supported by 750 associates and more than 100 service engineers across 95% of the country’s pin codes. Now part of the global US-based Bain Capital Group, Milacron continues to push tech boundaries with over 290 pre-engineered models, turnkey systems, and advanced IoT-enabled solutions through its M-Powered platform.
Shukla highlighted key success stories from the past year in packaging, construction, automotive, and lighting components. It has partnered with a mold-maker to produce a flip-top cap on a 550-ton machine—a smaller, more efficient, and cost-effective solution than the previously used 650-ton press for this application. For construction fittings, it has developed the first domestically built 1,300-ton machine for PVC/CPVC fittings of up to 28 kilograms per shot, and with the near-term capability to reach 40 kilogram products.
Highlighting more compact and energy-saving machines, Milacron has enabled helmet production on a compact 350-ton all-electric machine, optimized for speed and space. It has also designed and manufactured a special machine in India to mold complex lighting components, replacing high-cost imported solutions for ambient lighting.
He explained that all Milacron machines now feature its M-Powered IoT—enabling real-time performance tracking, predictive maintenance, and remote diagnostics, significantly improving uptime and customer productivity. Speaking about the company’s innovations, he mentioned its mono-sandwich and co-injection technology platforms that combine vertical and horizontal injection units to sandwich materials—using up to 70% recycled content without compromising cycle time.
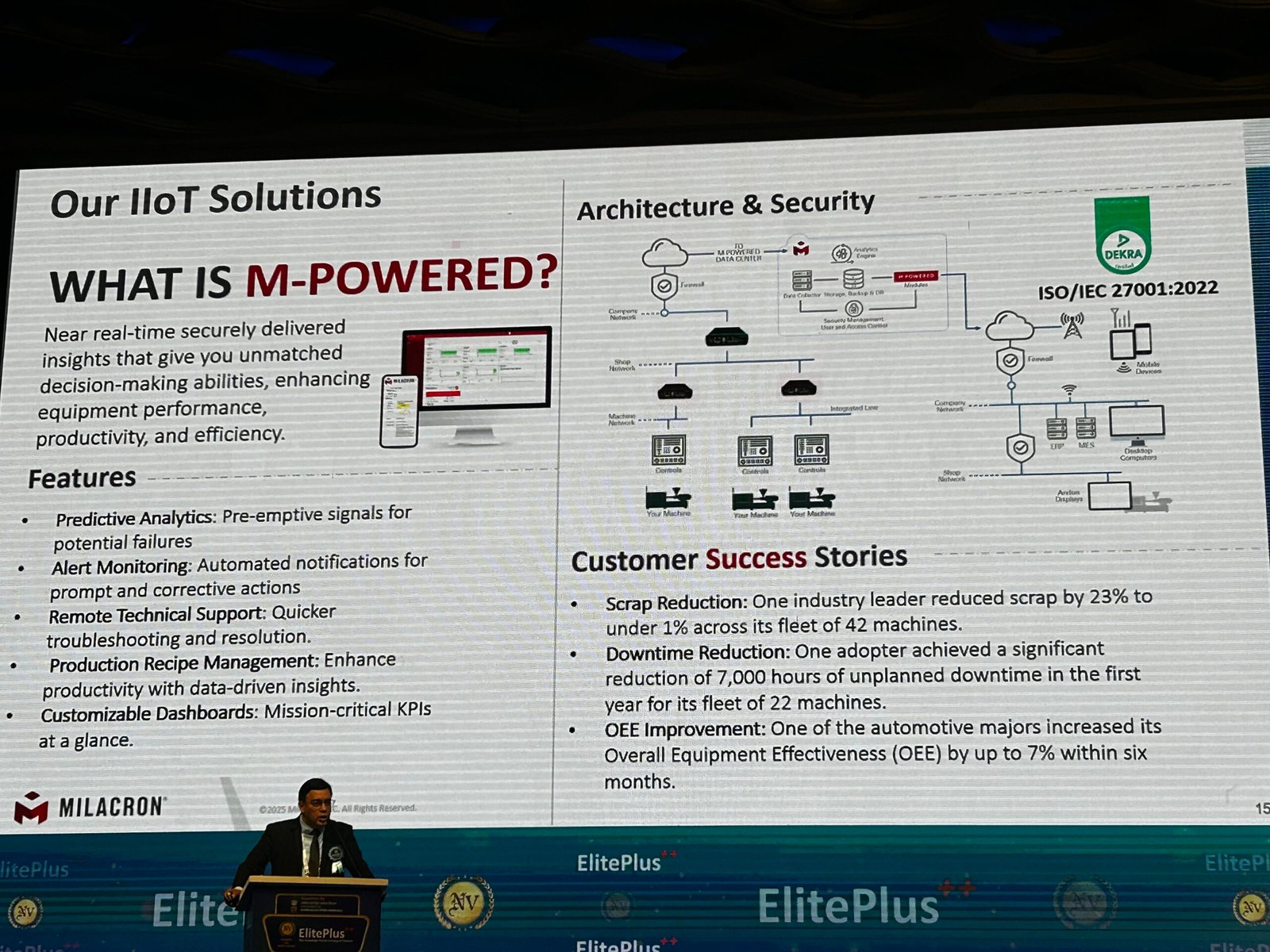
Its M-Series co-injection machine, built in India and exported to the US, can produce two 18-liter HDPE pails with in-mold labeling (IML) in just 18 seconds. Its low-pressure injection molding (LBIM) machine is meant for large-part manufacturing, such as pallets, using 100% recycled material. The Milacron LBIM enables wood-to-plastic conversion, with parts up to 150 kilograms made in a single shot. The first India-built LBIM machine is set for launch this December in Ahmedabad.
Milacron’s B-Series machine, designed and built locally by Indian engineers, offers 50% oil savings, 10% faster cycle times, and a 25% cost reduction. Its launch is expected in February 2026.
The company has completely designed and manufactured its third-generation all-electric injection molding machine in India. This machine features 7% higher output and speeds up to 500 mm per second. Shukla said it is ready for export markets with enhanced aesthetics.
Milacron now offers extrusion of CPVC pipes up to 400 kilograms an hour and PVC pipes up to 750 kilograms an hour—an entirely local innovation using a twin parallel extruder. Shukla ended by saying, “These developments reflect Milacron’s ongoing commitment to sustainable manufacturing, local engineering, and customer-focused innovation as the company moves confidently into its next decade.”