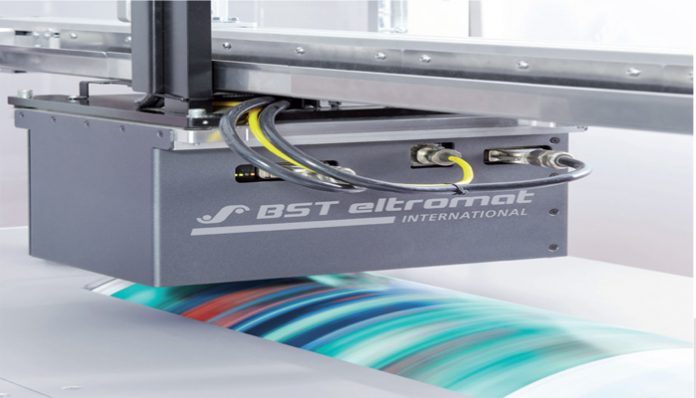
BST eltromat India announced completion of the installation and commissioning of its various quality assurance systems at Manikchand Packaging Limited (MPL), Pune. The company believes that the task was a complex one as MPL has a range of presses at their plant, which they wanted to invest in quality assurance systems to enhance their overall productivity and quality. The application and requirement of each machine was different. MPL opted to install BST eltromat systems on their various presses like Rotomec 888 printing machine: iPQ View & iPQ Check- 100% inspection, W&H CI Flexo machine: iPQ View, Cerutti machine: iPQ Workflow, iPQ Check- 100% inspection, iPQ view, Regi Star 20 and Viscosity Control, Brievt UV machine: iPQ view with UV flashes for security print inspection.
Since the installation, the amount of wastage in terms of resources, man-hours and energy has significantly reduced. Operators not only find the entire system user friendly but now they can also keep complete control over the production process. BST eltromat India presented the idea of a flexible platform through its iPQ Centre print process technology to MPL and explained them about the system’s endless capabilities when it comes to print process management. iPQ Center is a modular and forward-thinking system, which combines a variety of quality assurance tasks in one user interface.
Its uniform and intuitive control design enables a central access to various quality management features, right from a view of the complete web width, to zoom and selection of image areas, to the determination of measuring locations for color measurement. The iPQ-Center can be freely configured and upgraded as per the requirements of customers.
In the past, converters did not have the option of a modular scalable quality assurance system; they had to either install different systems for different tasks or compromise on the quality. So they would equip their machines with various systems that would work independently without a centralized HMI, which made it difficult for operators to use each of the systems to its full capacity.
The disadvantages of having various systems working without synchronization are clear—higher hardware expense due to equipping each system with its separate PC and monitor; greater complexity of operating processes for the machine operators due to different software, HMI, system setup, system features and its limits. As a result, there would be an endless learning curve for the machine operators with any break in the training chain leading to the misuse of the system or the system being idle due to operator frustration. It is to address these issues that iPQ Center has been developed.