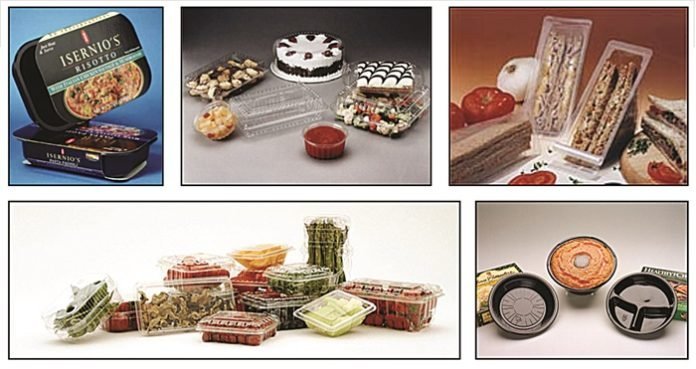
It has its potential and its challenges. Given this background, specialists from Germany and entrepreneurs from India shared ideas and pointers on the future of plastic applications in the food industry. Topics discussed in fairly deep technical detail ranged from food safety to smart machines in beverage food packaging; cost-effective production systems for caps and closures and more.
The two-day Indo-German Seminar on Plastic Applications in the Food Industry was held on 20 and 21 February 2014 at the Lalit Ashok in Bengaluru. Germany’s consul general in Bengaluru, Jörn Rohde, was the chief guest at the inauguration.
Technical presentations which drew the audience included machinery and robotics in general packaging; innovative green technologies; new opportunities in film production; pellitizationofPET and PLA; new challenges in sheet extrusion for rigid packaging applications; and innovative food packaging solutions through cooperation along the value chain.
PlastIndia launch
During the event, the launch-function for next year’s PlastIndia 2015 was also held on the first evening. After a networking tea on day two, the discussions focused on increasing the yield of film production; extrusion blow moulding for the diary market; and thin-wall moulding of packaging containers.
Other themes related to the expectations and challenges of plastic packaging for food were also taken up. Deepak Lawale, secretary general of the Mumbai-based Organization of Plastics Processors of India (OPPI), was among those playing an active role in making a success of this event.
Enrico Rühle, CEO and managing director for South Asia of TÜV Rheinland India, the Cologne-headquartered leading provider of technical services worldwide that employs over 17,000 people, traced the growth of the firm in India. In 1996, it started India operations as a subsidiary of TUV-Rheinland Japan. After setting up new offices and ‘soft lines labs’ at Bengaluru and Gurgaon, it now has 30 offices in 32 locations across the country.
Food safety in India – FSSAI
Rühle pointed out that the Food Safety and Standards Authority of India (FSSAI) has been established under Food Safety and Standards Act, 2006. It consolidates various acts and orders that earlier handled food-related issues in various ministries and departments. It aims to establish a single reference point for all matters relating to food safety and standards.
Under Schedule 4 of the FSSAIAct, the general requirements include: water testing; packaging material safety; equipment hygiene; personnel hygiene; raw material safety; end product safety; environmental monitoring of production and other areas; disposal and washing area’s hygiene levels; a declaration of nutritional facts; and a declaration of the best-before date (thus needing shelf-life studies).
Rühle pointed out that contaminants could be physical(stones, hair, rusted nails, feathers, cigarette buds, burnt matchsticks, animal droppings, thread and ropes from storage bags), chemical (pesticide residues, veterinary drug residues, nonpermissive food additives, naturally occurring toxins, cleaning chemicals, harmful gaseous surroundings, excess permitted food additives) or micro-biological (agri raw material, food handlers, garbage and sewage, pests, packaging material, soil, temperature and moisture).
Outlining food packaging requirements under the FSSAI, Rühle explained various food grade estimations from different parts of the globe.
More aware consumers
He cautioned that today’s consumeris “more aware than before about food safety and related risks.” They’re also more curious about what they eat, more allergic to food items, and “fascinated and ready to explore packaged foods.” Yet consumers also don’t worry about hazards from packaging, and in this gap lies the risk, he suggested.
Patrick Scharpf, of the Swiss NETSTAL Maschinen AG, pointed to the concept of a ‘smart machine’ — which combines the most suitable technologies that provide the highest productivity at lowest cost. Its machines, he said, were able to produce sophisticated packaging for dairy products, plant pots, multi-chamber containers, buckets, cartridges, tubes and tablet containers, and even airline cups.
Eduard Stückle of the German ARBURG GmbH + Co KG — a company manufacturing modular injection moulding machines and flexible robotic systems stressed the importance of caps and closures in the food and beverage industry.
Crucial consumers
“They have a rather short life time and can be regarded as a disposable part. Due to these facts, the whole market is interested in producing closures at the highest possible output and lowest possible price.Cooperation between mould maker, machine manufacturer and down-stream-supplier can lead to a significant improvement of output and reduction of production costs,” he said.
Samir Chimbalkar, manager key accounts of Baumuller India, focused on innovative drive solutions for general packaging and film production machinery and robotics. The Nuremberg-headquartered Baumülleris a supplier of mechanical engineering automation solution systems.
Green material handling
Srikanth Padmanabhan of Motan-Colortronic Plastics Machinery (India) spoke on innovative green technology in material handling for polymer processing in packaging applications.
“Modern day food packaging extensively uses polymers due its cost advantage and versatility. The focus now is to reduce energy requirements, avoid polymer wastage and recycle rejects,” said Srikanth Padmanabhan. He suggested two ‘innovative green technology’ concepts.
Gerhard Schoone of Windmoller & Holscher argued, “that due to the highly competitive market in India, many local film producers face challenges in their film production and conversion, day-in-day-out.” Schoone argued that the biggest challenge for them is to reduce the film and conversion costs to the maximum extent while keeping the quality of the film at the same level.
The focus on pre-requisites for efficient PET bottle production came from Andreas Vömel oftheAutomatikPlastics MachineryGmbH.Given the demand of the Indian PET bottle market, he stressed the importance of recycling via the ‘bottle to bottle’ and the use of efficient technology.
Vömel dealt with the entire process chain downstream of the extruder – that is, melt pump, melt filtration and conveying, PET pelletizing, crystallizing, and downstream processing of the pellets in extrusion lines.
“Dedicated equipment components and targeted processing technology contribute essentially to the economic success of the user, whether in virgin polymer production, in PET recycling operations, or in sheet and profile extrusion applications,” he emphasized. He outlined the latest innovations in these fields of application and processing – from melt to product.
Rigid packages
Focus also went to the global market for rigid packages, which Mark Borutta called “highly competitive.” Borutta is the area sales manager of Reifenhäuser Cast Sheet Coating. He talked about the new trends and challenges in sheet extrusion for rigid packaging applications – current market trends, increasing PET sheet production efficiency for trays and blisters and new mineral-filled sheets for cups and trays.
He made the point that the market demands regarding optical properties and performance of a package increase while the prices for the packages are under continuous pressure. Producers of sheets for rigid packaging need to continuously increase their production efficiency to maintain margins. This, he argued, leads to the demand for new processing technologies as well as for new products, even if this might result in higher investment costs at the beginning.
40% wastage
Statistics can be shocking. Figures say that today more than 40% of food is wasted before it reaches the consumer in India and other developing countries, mainly due to missing or improper packaging. “Innovation in packaging is therefore the key to reduce such losses whereas the development needs a close cooperation along the value chain of this industry. Starting at the raw material makers the collaboration (needs to reach out) to the brand owners to understand each of their needs,” argued Markus Gschwandtner, sales director of Brückner Maschinenbau.
Ganesh Sivaramakrishnan of Isra Vision India, based in Pune, suggested increasing the yield of film production by deploying the “latest trends in optical inspection technologies.” Optical inspection’s latest developments, he argued, not only find defects in gels, contaminations, black specs, but also help to undertake root-cause analysis to improve the total output of the line and to avoid producing and shipping defected rolls to customers. Isra Vision is involved in fully automated optical surface quality control. It undertakes surface inspection of special paper, paper, metals, coating, composites, non-wovens, film, glass, print and solar.
Extrusion
On the technical front, another presentation by Andreas Lichtenauer, managing director and partner of the Bonn-based Kautex Maschinenbau offered an overview about the different extrusion blow moulding applications in the food industry, especially in the dairy market.
Lichtenauer said India is among the top five countries for packaging worldwide – after China and the US, but ahead of Japan and Russia. India was also a ‘leading milk country,’ with a 16.7% global share. Only the EU as a whole (with 19.3% share) came higher.
Another innovation to be showcased was the quick color change system (ActiveColorChange). “This system is a new innovation to improve the efficiency and flexibility for moulders with many color changes in the packaging field,” said Jens Loewe, head of product management, Sumitomo (SHI) Demag Plastics Machinery.
Thinwall too
Meanwhile, a focus on ‘thin wall packaging in the 20th century’ came in from Kurt Hell, sales manager (business unit packaging) of Engel Austria. He spoke of high performing, efficient and flexible all-electric injection moulding technologies for barrier applications, IML and other thin-wall containers.