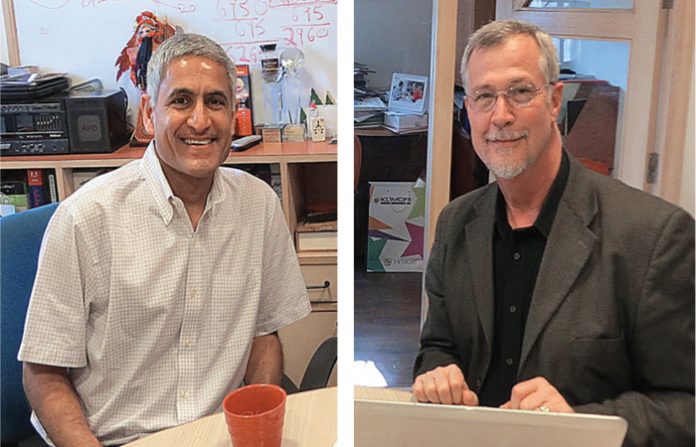
A new generation of G7 Certified Experts and Professionals has emerged after successful completion of training during the recent Idealliance G7 Expert/Professional Training and Certification Program, hosted by Imagine! Print Solutions in Shakopee, Minnesota.
This special event included an introduction to a new Idealliance Program, GRACoL Plus. To increase the appeal of offset to a wider audience, including inkjet, gravure and flexo, Idealliance is developing a methodology by which the printed gamut of a 4-color offset press can be expanded while maintaining G7 compliance. Imagine! Print Solutions was chosen to host this special event to take advantage of its high-caliber of equipment and quality capabilities.
The training brought 29 participants from across North America – including representatives of printing and graphics companies, print suppliers and even a university professor – together to the Imagine! facility. The intensive three-day session, led by instructor and independent color management consultant Don Hutcheson, utilizeda combination of lectures, hands-on labs and demos, and group discussions to engage and educate participants in G7 methodology.
G7 is an exciting advancement for the print industry, developed by leading global print standard authority Idealliance as both a definition of grayscale appearance and as a method of attaining a visually neutral balance and tonal curve for calibration of CMYK imaging devices. Its implementation in proofing and printing systems allows for a consistent proof-to-press match, easier management of color appearance between presses and substrates, an expanded color gamut, and faster, more efficient make-ready on press. With G7 currently in use by more than 1,000 qualified print suppliers worldwide, the method ultimately benefits both printers and their clients, ensuring consistent, standardized printing with every run.
Following successful completionofG7 training and examination, the title of G7Expert or Professional is bestowed to each participant, depending on the needs of the individual facilities. These certified experts and professionals have proven skills in the fields of color management, process and quality control. They effectively demonstrate the ability to analyze color or print-related issues and remedy them through corrective action, bringing systems under control to a set standard with repeatable and predictable results. The skills and methodology honed by participants through G7 training are then brought back to improve the printing quality and consistency at their own facilities.
As a G7 Master certified printing facility, with four G7 certified Experts on staff, Imagine! Print Solutions provided the perfect backdrop for this latest G7 training event. Participants, congregated in a large, stadium seating auditorium during lectures, made use of ample press and proofing equipment for lab demos, and were treated to on-site catering for all meals. Though the June 2015 training sessions were the first to be hosted by the Minnesota-based company, it is clear Imagine! is committed to promoting Idealliance G7 methodology and continual improvement in printing practices throughout the industry.
Note: The Indian affiliate of Idealliance has been active since mid-2013 in publicizing the G7 method for standardization and color management. Color Management Professional training events were held in February 2014 at the Konica-Minolta demonstration centre in Gurgaon and at the Svenska Hotel in Mumbai. The training was conducted by Steve Ballinger with approximately 50 color experts being trained and qualified to take the on-line exam that would certify them as G7 CMP professionals.
In February 2015, Idealliance India asked the well knownG7 expert Steve Smiley to conduct G7 seminars for brand owners and packaging converters in Delhi and Mumbai. These were held with great success with both brand owners and packaging printers and converters learning about appreciating the possibility and the method of standardizing branding and packaging color reproduction across processes and substrates.