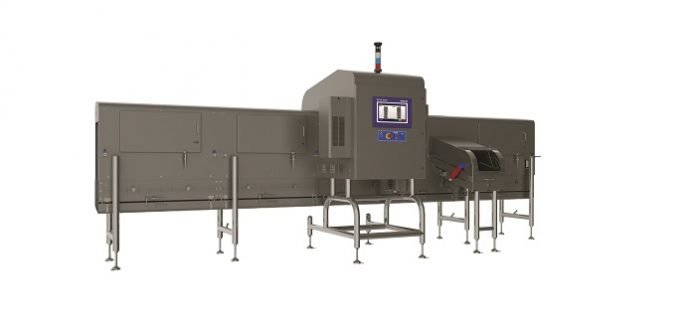
Extending its range of next generation X-ray inspection systems, Mettler-Toledo Safeline X-ray has designed the X37 Series for optimum product inspection of tall, rigid containers, including cartons, doypacks, plastic and glass containers and metal cans. Available in a number of flexible technology alternatives, the X37 Series can be configured with different detector sensitivity options supported by a range of power generators, to detect and reject contaminants, such as metal, glass, calcified bone or high-density plastics. This customization enables food and pharmaceutical manufacturers to reduce total cost of ownership (TCO) and comply with safety regulations and guidelines by consistently guaranteeing contaminant-free products.
In order to suit a variety of tall, rigid packaging applications, manufacturers can choose between a 0.4 mm and a 0.8 mm detector diode. The 0.8 mm detector technology is five times more sensitive to X-ray than traditional systems, ensuring unparalleled precision in the contaminant inspection of food and pharmaceutical products. For the inspection of composite cans, cartons, tubes, doypacks and plastic containers, for instance, producers can select a 20 watt generator which can result in a significant reduction of power consumption and cooling requirements, as it offers the sameprecisionas a conventional 100 watt device.
“Traditionally, food processors have needed to implement high power X-ray systems to inspect cans or glass containers athighspeeds, sometimes inexcess of 1,000 products a minute,” explained Daniela Verhaeg, marketing manager, SBU X-ray Inspection, Mettler-Toledo Safeline X-ray. “The X37 Series, with its new detector technology and class-leading inspection software, is able to offer equal or, in some cases, improved detection levels whilst typically only needing one-fifth of the standard X-ray energy power consumption.
Consequently, this allows food and pharmaceutical manufacturers to substantially reduce operational costs while also maintaining the utmost level of safety and quality fortheir products.”
The new X-ray range can be fully configured to the particular needs of a specific production facility. Manufacturers can, for example, select different highspeed reject systems to match their production needs and guarantee easy and effective product rejection. Suitable for a wide range of product types, the system is available with fully adjustable pusher and air blast options with a large vision window on the tunnel and chute. An optional removable rollertrack inthe reject chute can also be installed to ensure that products slide down the chute gently and to facilitate easy cleaning.