An integrated packaging concept that guarantees hygienic, reliable, swift and efficient packaging of finished products is an important component in modern production of meat and sausage products. The correct selection of vacuum generation systems substantially influences the operational reliability and economic efficiency of the packaging process. Depending on the size of the plant and the production quantity, there are a number of vacuum supply options.
Vacuum packaging of meat and sausage products offers a fundamental advantage: the elimination of the air in the packaging drastically reduces the oxygen content, slows down the activity of bacteria requiring oxygen and thus significantly increases shelf life. Additionally, vacuum packaging is hygienic and enables the products to be presented in an attractive manner. Vacuum must be generated to meet the requirements for vacuum packaging. This can be achieved by either an integrated or a separate vacuum pump. Other alternatives include central vacuum supply systems to which several packaging machines are connected.
Integrated vacuum pump
Normally, the vacuum pump is integrated or set up separately in the immediate vicinity for any vacuum packaging machine, whether it be a vacuum chamber packaging machine, tray sealer or thermoforming packaging machine. Oil-lubricated rotary vane vacuum pumps are almost exclusively used for this purpose. This type of vacuum pump, developed specifically for the packaging industry by Busch Vacuum Pumps and Systems, has long been the standard in vacuum packaging. The newest generation of these vacuum pumps is optimized for energy savings of 20%.
Partial centralization
With partial centralization, the rotary vane vacuum pumps are removed from the actual packaging room and integrated into a central pre-vacuum system for all packaging machines in a separate room. Dry, oil-free vacuum boosters are installed directly in the packaging machines and connected to the central pre-vacuum technology system with a scheme of pipes. If more packaging machines are used, the investment costs become high due to the vacuum boosters in the individual machines; thus, it is recommended to fully centralize the vacuum supply.
Central vacuum supply
Economic efficiency: Full centralization of the vacuum supply is an economically viable option when there are six or more packaging machines. Usually, it is safe to assume that substantially fewer vacuum pumps are required for a central vacuum supply than for a set-up of individual vacuum pumps directly alongside the packaging lines. If the vacuum supply is subsequently converted from a decentralized to a centralized system, existing vacuum pumps can be integrated into the new centralized system, reducing the investment costs.
Hygiene: The absence of all vacuum generators in the production or packaging room in turn eliminates the danger of food contamination through oil aerosols. Additionally, there is no need for employees to enter the hygienically sensitive packaging room for maintenance or repair work. Clean-room conditions can therefore be created in the area surrounding the packaging lines.
Operation method: The individual packaging chambers are evacuated in two stages to be able to run maximum cycle frequencies on the packaging lines. To do so, the critical pressure gradient is utilized and thus achieves the fastest possible evacuation. This requires a rough vacuum pump unit for the initial evacuation and a medium vacuum pump unit for the evacuation to packaging pressure. The reversing valves with the corresponding control units are attached to the packaging machines. They control the transition from a rough to a medium vacuum. For thermoforming packaging machines, the molding station is supplied using a separate thermoforming vacuum pump unit. This ensures that the previously heated base foils are sucked into the tray mold and take the desired shape.
On the one hand, this separation into various vacuum stations is necessary as the molding and sealing functions run at different vacuums and, on the other, as a substantially lower pumping speed is required for the two-stage evacuation of the sealing chamber. The pipework serves as a vacuum buffer. This buffer is necessary to keep the packaging pressure at a constant level, even when all the packaging machines are running with the same number of cycles.
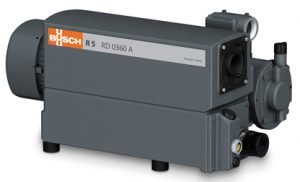
The central vacuum system is fully automatic: it activates individual vacuum modules if a greater vacuum is required or switches off individual vacuum modules if a smaller vacuum is required. If a vacuum pump fails in the rough, medium or thermoforming pump units, then the reserve pump is automatically activated. This ensures maximum operational reliability for the vacuum supply to the packaging machines.
Maintenance: A central vacuum supply system has a modular design, which allows maintenance work to be carried out during operation without affecting the production output of the packaging machines. In the central system, the individual rotary vane vacuum pumps are subjected to substantially lower loads relative to the individual units, thus extending the maintenance intervals.
Integration into the process control system: Central vacuum supply systems are very well-suited for integration into the operational process control system, meaning that the vacuum plant can be controlled and monitored from a PC. Any indications of imminent faults can be easily identified and rectified before the machines fail. The necessary technical parameters can be permanently called up and the pressures in the vacuum lines are displayed in graph form.