PMMI, The Association for Packaging and Processing Technologies that hosts Pack Expo, used the occasion to announce their updated 2015 Business Intelligence Report on the Global Packaging Industry. Lumping South Asia together with other Asian nations as the ‘Asia Pacific’ region, PMMI’s report attributes 46% of global packaging volume to the region. According to the PMMI report released at Pack Expo, worldwide flexible packaging is the industry segment projected for the most growth – whether in South Asia or the mature US market.

Walking the halls of Pack Expo, you certainly wouldn’t know you were in a city that is known as Party Central. For exhibitors and visitors alike, this is a serious industry event and everyone is clearly at Pack Expo to do business. This was the first Las Vegas year for the companion Pharma Expo Show, at which most exhibitors seemed to have noticeably larger stands than in the Pharma Expo’s world debut last year in Chicago.
Together, Pack Expo and Pharma Expo are included in the top 50 of the fastest growing trade shows in the world. You couldn’t feel that the Las Vegas show was smaller than last year’s in Chicago, especially when you ran out in the +/- 100 degree Farenheit dry heat to get from one exhibit hall to another. Actually, it was a tad smaller, that is. About 2,000 exhibitors in Las Vegas compared to more than 2,350 in Chicago, but just as important to the exhibitors who find this location a chance to connect more with packagers and brands that are headquartered in the US West.

nominated. Photo Peter Kachergis
Walking the floor that growing consumer interest in health and wellness did seem to be a driver of some of the more notable ‘Big Idea’ innovations, along with the continuing march towards global standards for food and drug safety. From a US health-conscious consumer perspective Milliken’s additive for a Klear Can that allows use of extant tooling originally created for metal can production and can now eliminate metal cans’ potentially carcinogenic bisphenol-A (BPA) or bisphenol-S (BPS) layers was a standout. Shawn Bhavsar, account manager, plastic additives for Milliken, seemed to enjoy the astonished reactions to the see-through canned fruit he held in his hands.
Milliken makes the Millad NX 8000 clarifier technology used in Milacron’s polypropylene Klear Can. From packagers’ point of view the Klear Can enables use of existing downstream infrastructure, as well as the same easy-open and traditional lids used with metal cans. Brand owners benefit by being able to differentiate their products at the point of purchase and consumers can easily view the quality and freshness of fruit, vegetables and other foods through the clear container.
The stackable Klear Cans are also 40 to 50% lighter than metal cans of equivalent size, helping to reduce transportation costs, fuel usage and carbon emissions. The huge potential of Klear Can though is likely rooted in the growing concern among US consumers about BPA and BPS plasticizers in ordinary metal cans. Bhavsar says, “Using the same machines as before, Klear Cans can be sterilized in 125 degrees Centigrade and give a three-year shelf-life. Our clarifying additive is what makes the polypropylene clear instead of hazy. We can give them vivid colors that are also important to branding – quite a different look – and it’s all sustainable and recyclable.
Avery Dennison – with an eye towards products as diverse as wipes, dog treats, pasta, cookies and more – was showing off their closure solutions at Pack Expo and especially reusable adhesive labels for hermetic seals that replace zippers. The truly breakthrough technology though that they brought to the show was a variant of RFID technology, Near Field Communications (NFC), for temperature tracking. Although it is still pre-commercial and not slated for full release until 2016, according to Avery Dennison’s associate product manager – Pharmaceutical Materials Group, North America, Alison Schuitema, this clearly will be a big game changer for pharma manufacturers in India and elsewhere.
Temperature tracking sensors are placed in what looks like a simple plastic card. Using NFC, these sensors communicate with a smartphone app to log temperature data over time and during the products’ entire supply chain journey. All you have to do is touch the card with the phone and voila! All data is stored in the NFC chip and can be uploaded to a smartphone at any time throughout the supply chain. For drugs, biologics, frozen and perishable foods and materials handling scenarios this disruptive technology will quickly make data loggers obsolete. Schuitema says, “Our solution costs about US$12 to US$14 for a card; a temperature data logger on the other hand costs US$40 to US$70 or more.”
While Pack Expo is largely about marketing to North America, many exhibitors were introducing new technology that was developed with the needs of the Indian companies front of mind, to meet international food safety standards and FDA quality compliance standards. Bonfiglioli Engineering of Italy was showing its new Headspace Gas Analysis Quality Control Solution that was specifically created to meet needs of Indian pharmaceutical manufacturers, and which had its world debut earlier this month at the Pharmac Show in Ahmedabad.

Most exhibitors though were not there to make announcements of new machines or technology but rather to give their North American prospects a chance to see their existing offerings or the new features of long-established systems – better mousetraps, so to speak. Global Vision was showcasing various improvements to their software that were all geared to focus on defects and decrease false positives in defect rates. Teaming with Ishida, Heat and Control was exhibiting a rotating salad weigher. According to Heat and Control Trade show coordinator, Bill Learned, “This design minimizes stick and clog with
a wiper giving the best speed in the industry for this type of packaging.”
Nearly a dozen South Asian exhibitors (nine from India, one from Pakistan, and one from Bangladesh) were exhibiting at Pack Expo and those interviewed expressed great satisfaction with the response to their offering. Go to a Pack Expo show in Chicago and
the dance of robotic arms swinging amidst a sea of other packaging machines gives you a mild jolt as you enter the exhibit hall and perks your interest to delve into the latest industry happenings. Put those same buzzing machines in the Las Vegas Convention Center and you instead may welcome a feeling of relief that the Pack Expo halls seem a bit sedated compared to the hotels’ neon light casinos you have had to enter or exit in order to get to the show. Perhaps this welcome break from the blinking slot machines is part
of the success of the Pack Expo shows held in Las Vegas. Next year though, consider braving the November chill in Chicago to see what Pack Expo 2016 has to offer.
Bonfiglioli’s technology for headspace gas analysis
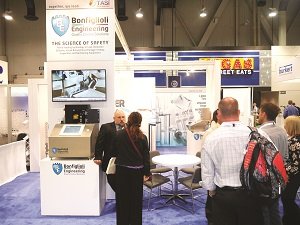
Bonfiglioli Engineering, a TASi Test and Inspection company from Italy that specializes in food and pharma test technology was also showcasing its new NDT technology for headspace gas analysis. The Bonfiglioli system uses a combination of laser technology with leak testing of sealed packages and just had its world debut in India in early September at the Pharmac Show. It’s geared for quality controls of sterile drugs such as oxygen sensitive liquid products or lyophilized or powdered products to ensure that drug potency isn’t lost.
Sergio Bonsi, marketing manager of TASi, says, “This technology–Tunable Diode Laser Absorption Spectroscopy (TDLAS) –counts the oxygen molecules and the moisture in a combination process and package test . . . If the headspace is contaminated we detect this as well as quantify any leakage . . . We developed this technology for requirements in the Indian pharmaceutical industry and we see a lot of opportunity in the Indian market.”
Intralox showcases DirectDrive Self Stacker
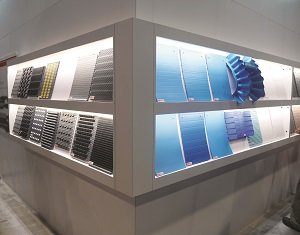
Intralox, known for conveyance technology, was showing, among other products, its Direct Drive Self Stacker, a spiral product claims to be lightweight. Moreover, it is a hygienic modular plastic solution that saves floor space, provides for horizontal air flow, and minimizes incidences of de-stacking. While they make larger systems, the compact one on display at Pack Expo was, according to Intralox R&D manager for food businesses, David
Bogle, proportioned as it would be for typical South Asian businesses. Bogle points out, “This is ideal for freezers. The plastic belts are on top of each other and self stacking, with a design that allows you to blow air across bringing fresh air to the product and enabling you to freeze quickly so you don’t dehydrate products. It’s an entirely hygienic system that you can clean in place.”
Bruker shows the latest IR spectrometer technology

Kachergis
TANGO, the latest IR spectrometer technology from Bruker Optics is what Bruker’s western regional manager, Robin Lavengood, mostly wants Packaging South Asia readers to know about. It can be used by packagers to correctly identify base resins or final products. Lavengood says, “We have four offices in India and pharma is certainly a key industry for this technology but our biggest growth is in Animal Feed and Food ingredients (AFF). For example, we can calibrate rice to analyze how much protein, fat, fibre, and more is in it. This enables companies to do branding for products such as rice milk. Our technology is both for the brand companies and for the supply chain.”
Illinois Instruments’ non-depleting oxygen sensor
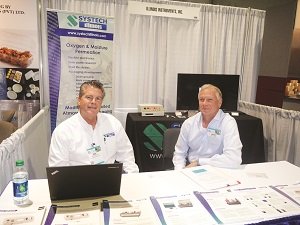
Illinois Instruments was one of several Pack Expo exhibitors that was offering technology to deal with headspace measurement in product packaging with food, pharma and medical device applications. Brad Fritschle, regional manager of Systech Illinois, says, “We’ve been selling our technology for detecting oxygen and carbon dioxide in a product’s headspace for decades, including the last decade or so in India, and now have 1,000s of units worldwide.”
Systech Illinois was introducing its latest GS6000 Headspace Analyzers at the show that feature a nondepleting oxygen sensor made from a zirconia core. For carbon dioxide,
the sensor integrates with a non-depleting infrared (IR) sensor. Fritschle says, “All the other technologies are akin to batteries in that they use an electrochemical reaction and the more oxygen they see the sooner they have to be replaced. Ours is non-depleting, and it’s the best technology to get shelf-life with inert gas flushing systems in packaging.”
Global Vision’s innovative proofreading technologies

false positive rate. Photo Peter Kachergis
Canadian Global Vision, whose tagline is ‘Innovative Proofreading Technologies,’ have the pharma market in mind as it continues to improve its software offering. Their website states that the software is used by 72% of the global pharma industry.
Robert Jennings, account executive of Global Vision, explains, “Our value is that we cover the entire workflow from the copy deck to final products. Pharma companies are our biggest users and about half of our sales are to the brands with the other half to the supply chain. What’s new in our software that we are introducing at Pack Expo is a variety of defect-focussed improvements that overall decrease the false positive rate.”
“Our unique capabilities are based in our use of several different methods for inspection at once, instead of relying on just a single technology as others do. One of these methods is a unique ability to pull the text content out to a separate layer and focus only on that content. Our pattern matching technologies reduce noise and are able to not only text but also inspect bar codes, braille, do spell checks and more. Because pharma is a regulated market with international quality standards, our products are well suited to help producers and packagers in South Asia as elsewhere,” says Jennings.