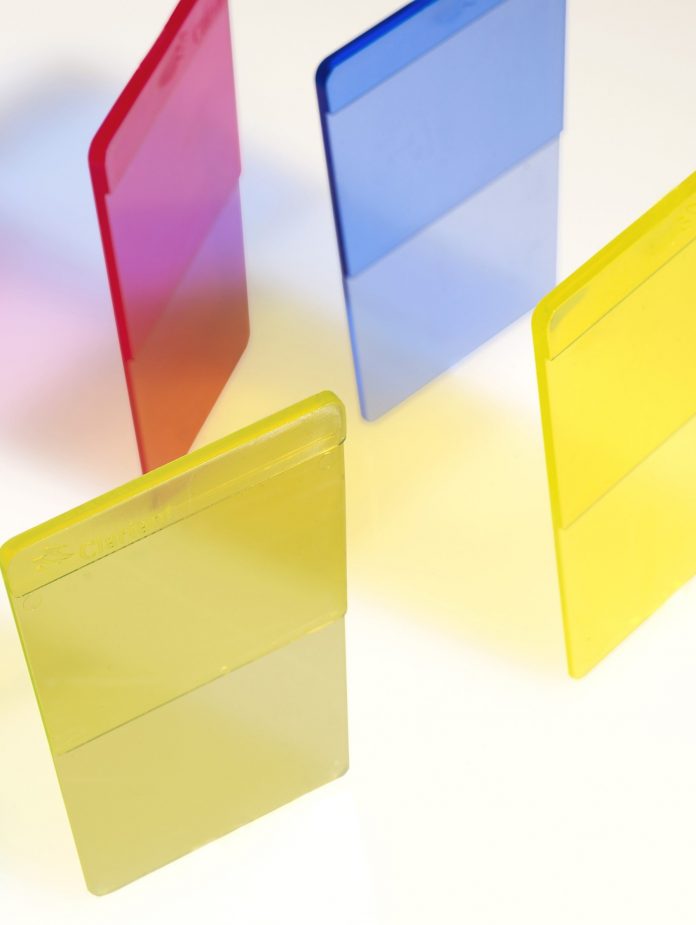
Clariant Plastics and Coatings Healthcare Polymer Solutions announce a new family of ABS polymer compounds that offer makers of medical devices and pharmaceutical packaging enhanced functionality without compromising on compliance with regulatory requirements. The resins are part of the MEVOPUR line of color and additive concentrates and ‘ready-to-use’ polymer compounds. ABS (acrylonitrile-butadiene-styrene) is known as a versatile material that is commonly used in the consumer and automotive industry and now widely available as a ‘medical grade’ resin. Clariant is using its formulation skills, compounding capabilities in EN-ISO13485:2016 certified production facilities to enhance the ABS resin properties with pre-tested ingredients that support compliance to standards such as ISO10993 and USP Class VI. “Clariant recently introduced the theme of ‘The Color of Innovation,’ to show how making decisions about materials early enough to apply QbD (Quality by Design) principles widens the scope of possibilities,” explains Steve Duckworth, global head of Marketing and Business Development. “We are known for color, but we also demonstrate what can be done to add new properties to polymers – such as medical-grade…
Choose your subscription to read more
Trial
- ₹ 0 for 4 weeks*
PSA Plan 1
- ₹1,500.00 for 1 year*
PSA Plan 2
- ₹2000 for Year*
PSA Plan 3
- ₹3,600.00 for 2 year*