“Green production and sustainability were two of our main concerns while setting up the robotic plant. The plant not only helps us in producing rotogravure cylinders in an eco-friendly way, but also helps our customers to contribute to the environment by consuming less ink—all of this without compromising on the image quality.”
Uflex’s robotic plant in Noida for manufacturing rotogravure cylinders is a modern and sophisticated laser engraving setup, which produces around 65 rotogravure cylinders a day. Fully environment-controlled, the automatedsystem comprises three zones: A, B and C. Zones A and B are no less than the ICU of a hospital, closely monitoring not only the precise engraving of the cylinders, but also auto-controlling the zones in terms of temperature, dust particle size and much more. The two specially programmed robots in Zones A and B work relentlessly and sequentially carrying the cylinders in and out of separate units within the New FX2 Laser system for processes like electric degreasing, nickel plating, copper plating, copper grinding, ultrasonic cleansing, lacquer coating and drying, through Zone C delivering the final cylinders ready for customers to use.
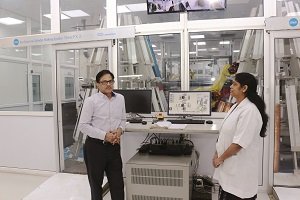
Installed in March 2016, the fully automatic robotic laser engraving line New FX2, by Think Lab, Japan is set up in a 300 sq. ft. area. According to PK Agarwal, joint president – cylinder business, Uflex, the robotic laser engraving line reduces the clumsy process of manufacturing rotogravure printing cylinders to a single-operator job. “The cylinder movement is fully controlled by the robots, requiring just one or two people to supervise the entire process. There are two stands with two racks each, where the cylinders are fed for the robot to pick up from. The lower rack can hold up to 20 cylinders while the upper rack accommodates 12.” According to Agarwal, the new robotic plant does not pose any threat to the existing human resources of the conventional cylinder-making plant as there exists a separate well-established market segment for conventional electro-mechanically engraved, embossed, coated rotogravure printing cylinders much like the laser robotic plant engraved rotogravure cylinders. At its conventional cylinder-making plant in Noida, Uflex produces over 200 cylinders per day and is 10 times bigger in size (cylinder manufacturing shop floor area) than the new robotic plant. In contrast, the New FX2 is a single operator system producing additional 65 cylinders daily.
There are two stands with two racks each, where the cylinders are fed for the robot to pick up from. The lower rack can hold up to 20 cylinders while the upper rack accommodates 12. Photo PSA
Agarwal says, “The robotic plant is used to produce cylinders for customers who require precisely consistent and high-print quality images for flexible packaging. Because the cylinders produced on the robotic system are dynamically balanced, they can run up to a speed of 500 m a minute. The image reproduction is also of very high quality. Users can produce high-definition output with a resolution as high as 6,400 dpi, a feat hard to achieve on a conventional electro-mechanical engraving process.” Another advantage of producing rotogravure cylinders on the fully automatic robotic laser engraving is the consistency in printing for flexible packaging. Because of the highly automated and sophisticated steps involved in the cylinder-making process, customers can derive extra mileage from each cylinder. Unlike conventional electromechanical engraving, the final laser engraved cylinders have circular cell structures, which means less ink consumption.
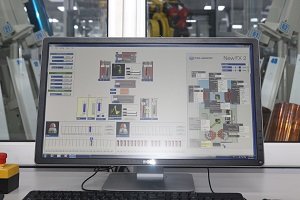
the New FX2 system. Photo PSA
The entire FX2 system is encapsulated in an eco-friendly platform with a highly effective waste management system. Sludge and wastages from the system are collected in separate containers in a room behind the robotic zones, without any emission to the open atmosphere, according to Agarwal. This waste is further recycled for ecological optimization. “Green production and sustainability were two of our main concerns while setting up the robotic plant,” he says. “The plant not only helps us in producing rotogravure cylinders in an eco-friendly way, but also helps our customers to contribute to the environment by consuming less ink—all of this without compromising on the image quality.”