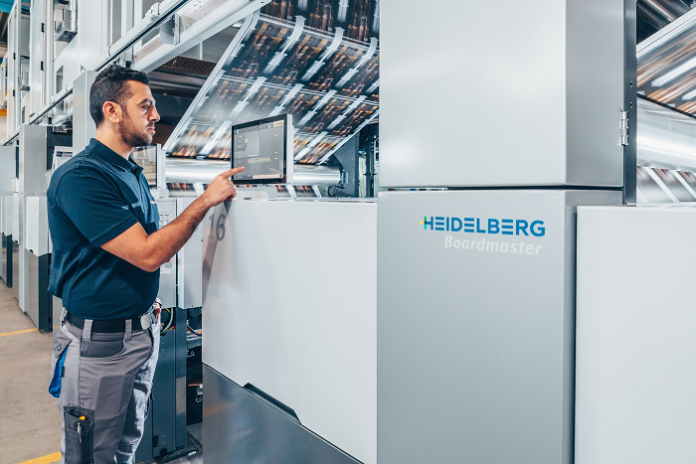
Heidelberg’s Web Carton Converting business has announced a new flexo press, the Boardmaster, a wide web inline rotary device for printing cartons that’s said to be the first flexo device to use Artificial Intelligence.
This is a replacement for Heidelberg’s existing liquid packaging flexo press though Matthias Boog, managing director of Heidelberg Web Carton Converting, says that the press has been completely redesigned. He explains, “Before starting development we talked with 30-40 customers as to what their requirements were. They wanted more efficiency which we have improved by more than 50%. You can change from one job to the next without stopping the machine and without operator intervention and with minimum waste of about 10 metres, which saves cost and is more sustainable. And helps customers grow in fields where they have not been before.”
The press is very highly automated, with Dr Ludwin Monz, Heidelberg’s CEO, noting: “Heidelberg has high expertise in automation, which is all about efficiency.” He added that sustainability is a growing trend, saying, “Heidelberg has focussed on reducing the power consumption of our printing presses.” Consequently he claims that the Boardmaster uses 35% less energy than an offset press.
The Boardmaster will run at 600mpm and there’s an option to increase this to 800mpm. It will take media up to 1670mm wide, with a choice of four print widths, starting with 850mm, then 1020mm, 1400mm and 1650mm. The repeat ranges from 405/ 480 up to 1070mm. It can handle substrates from 70 to 800gsm and can run right to left or vice versa. The ink can be either water-based or UV-curable with hot air drying or UV curing systems.
The press features a newly designed print deck as Boog explains, “We operate a non-stop print deck with two print units together so one print unit is always in operation while the other one can be prepared for the next job. There’s an alternative to use the two print units together combined with an inter-deck drier.” Heidelberg has claimed this idea of dual plate sleeve rollers a first but Bobst has been doing something similar in narrow web flexo for several years now on its M5 and DM5 presses.
Heidelberg claims that the non-stop print deck doubles the productivity of the press, based on Heidelberg’s assumption of 45% of uptime for a standard flexo press versus 90 percent for the Boardmaster because the press can switch straight from one job to the next. But this is only true if you use a fixed inkset for every job with the Boardmaster, since there only appears to be one inking system for each dual plate sleeve print deck.
Then again, most of the makeready time on a flexo press is due to changing the spot colours between jobs. So you could use a fixed colour gamut inkset on any flexo press, with the same four to seven colours, to cut wash-up times between jobs and improve the overall productivity.
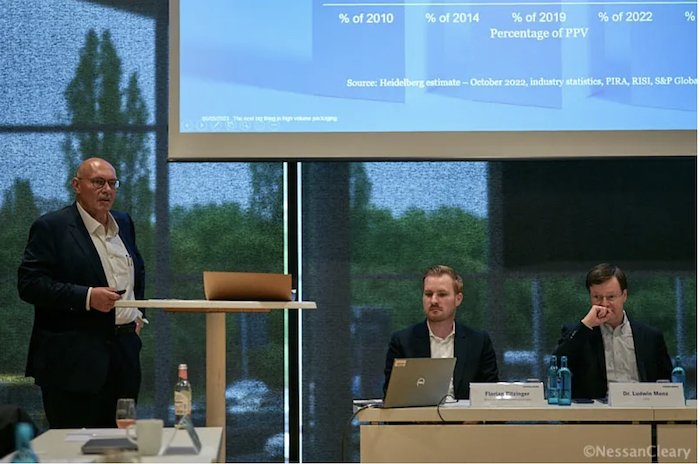
Photo Nessan Cleary
There’s a new offline plate and sleeve scanner, Intellimatch, which has a number of cameras to check the plates before they are mounted to the press itself. The results are automatically analysed through artificial intelligence to check for defects, which as Boog says “means that we only have good plates on the press.” The Intellimatch system also ensures that the print decks are adjusted correctly.
There’s a great deal of flexibility in the way the press can be configured. Boog says, “We can integrate any embellishment like hot foiling and embossing. it means if the market changes you don’t need a new machine just a new component.” These inline options include laminating, cold foiling, embossing and screen printing as well as digital imprinting, all of which can be added straight from the factory or at any point in the future. It can be set up to run roll to roll, roll to sheeter or even roll to cutter when combined with Heidelberg’s FCL flat-bed die cutter to create a single pass print and converting solution. However, this does slow down the productivity as the FCL runs at 300mpm and can only cut from 850 to 1400mm widths though the improvement in productivity should more than make up for this.
Packaging and digital
Dr Monz told journalists at Interpack, “It’s our ambition to continue to shape the printing industry. There are two segments within printing which we focus on because they are growing. And that’s packaging, which is a highly attractive segment, and digital printing, which is also becoming more and more important – maybe not in packaging but I believe that will become more important in the future.”
Packaging makes sense since every press manufacturer is hoping to exploit the huge opportunity that printing on packaging offers. As Monz noted, “Packaging is a growing business within printing, up 2.3%. The other big trend is sustainability and the shift towards printing on paper.”
He says that 15% of the folding carton market uses flexo printing and that this will continue to increase, giving a bigger role to Heidelberg’s Web Carton Converting division. The company was originally founded in 1993 as BHS Printing and finishing technology and acquired by Gallus in 2006.
In 2008 its name was changed to Gallus Punching and printing machines and in 2014, following Heidelberg’s full takeover of Gallus, it was rebranded as Heidelberg Web Carton converting. The division continues to operate from its original plant in Weiden, in southern Germany. Boog stresses its independence, saying: “We design, assemble and sell, distribute and product management. It’s a complete independent site with its own Profit and Loss figures.”
Heidelberg also markets its offset presses for packaging though it has lacked a high volume solution since giving up its VLF Speeedmaster presses in 2020. Monz explains, “Flexo is more cost effective than offset for large sheets. Some customers will choose one technology and others will choose the other. We offer both. The cost benefit of flexo is the combination of the capital cost and the running cost. The running cost depends on the volume of printing for very large format.”
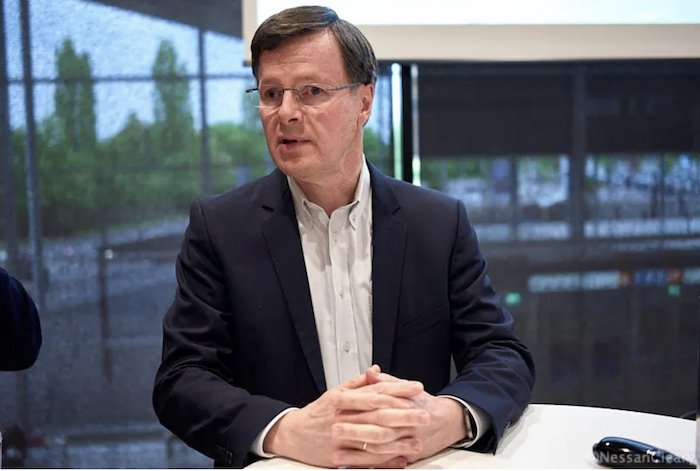
Photo Nessan Cleary
The second string that Heidelberg wants to play is in digital printing. Given the impact and growth of digital printing, it’s hard to see how any press vendor could ignore digital printing. And yet in my opinion Heidelberg has demonstrated very limited capability in this area so far.
Heidelberg does sell the Versafire dry toner production printers and has managed to add value through its Prinect software. But these printers are rebadged Ricoh devices so Ricoh owns all the IP. Heidelberg did develop a B1 inkjet press, the PrimeFire 106, which was built on a Heidelberg-designed chassis but with Fujifilm largely responsible for developing the print engine, including the Dimatix Samba printheads, meaning that Fujifilm owns most of the IP around the digital imaging as well as the heads. However, this press was dropped in a round of cost-cutting in 2020 along with the VLF offset presses.
Gallus has also developed the Labelfire 340 and Gallus One label presses, also relying on Fujifilm to develop the print engines. It seems most logical that Fujifilm would also have supplied the ink though Heidelberg has suggested that it supplies the ink. Then again, as all journalists know, most inkjet press vendors claim to manufacture their own ink though this is rarely the case.
Gallus also previously sold the SmartFire label press, which was a rebadged NS Lion with a Memjet VersaPass printing engine with dye-based inks. Strangely, this came to market shortly after Memjet had introduced its DuraLink heads with a pigment-based ink that would have been a much better fit for label printing.
So it’s difficult to see what expertise or IP Heidelberg itself has in developing inkjet print engines beyond working with partners. Monz told me that Heidelberg could simply buy in the printheads and there are plenty of press vendors that do exactly that, but there is quite a bit more to building a fully functioning inkjet press that can compete against the existing players. Monz also told me that Heidelberg did develop its own electronics but wasn’t able to elaborate further beyond suggesting that Heidelberg might introduce a new inkjet press at some point.
I hope that Heidelberg does make good on this because I fully agree with Monz’s assessment that digital printing will be important to Heidelberg’s future. The company has an excellent engineering heritage, together with a growing electronics business and very capable software development and should be able to build a digital press that’s underpinned by its own technology.
Strangely, despite using Interpack as the backdrop for its press conference, Heidelberg didn’t actually take a stand at the show, which seemed like a missed opportunity to engage with customers and show off samples. Gallus did have a small stand, with a picture of a Label One press, and Gallus also announced a new UVF01 ink set for its Labelfire 340 digital hybrid press. These inks have been designed for printing tube laminates and folding carton.
In the meantime, Heidelberg has already installed one Boardmaster and is about to ship another. Boog concludes, “We have proved that we can bring flexo with automatic changeover at 600mpm. So the machines are going into full production and there’s no more beta testing.”
You can find further details on the new Boardmaster from heidelberg.com and gallus-group.com.
First published on 15 May 2023 in The Printing and Manufacturing Journal. Republished by permission.