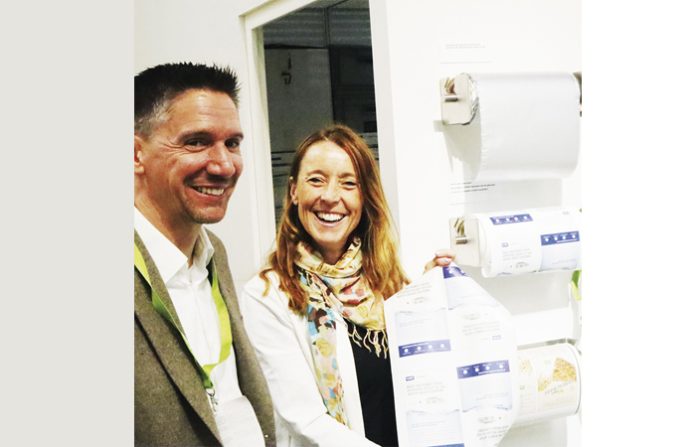
At Interpack we met with Kresimir Cule of BASF and Sara Alexander of Bobst to talk about recent developments in sustainable flexible packaging. In our very brief discussion with the two experts, we touched on water-based printing but spoke mainly about water-based adhesives for innovative laminates, and also the development of home compostable paper-based laminates. The idea of using water-based inks, coatings, and adhesives is to do away with solvents that generally take two days to cure sufficiently to be safe for food applications and that are unhealthy for the production environment.
Cule said at our meeting, “The packaging industry is desperately looking for more sustainable solutions. For multi-layer packaging, this is a very big issue. It’s a good time to discuss new ideas as the market is very open.” He showed us a new paper-based home compostable food contact laminate sample – consisting of Billerud Korsnas ConFlex paper, the BASF Epotal Eco 3675 water-based adhesive, and a certified compostable polymer Ecovio sealing layer that is for example appropriate for health and cereal bars.
Innovative water-based adhesive systems for sustainable laminates
Apart from the BASF and Bbobst solutions that are already in use by brand owners and converters, the two partners have been developing and testing new structures using a variety of new Epotal water-based adhesives and the Bobst laminators. For instance, Epotal BLX provides oxygen barrier coating or adhesive for monomaterials. For recycling after use, the barrier can be washed off for reuse of the monomaterial.
The advantages of moving to water-based printing and lamination processes are several, especially for food packaging, but require a considerable change of mindsets. Cule said, “With the use of water-based inks and adhesives, the workspace becomes much healthier and removes the risk of any solvent, aromatic isocyanates, or odor in the packaging.” These toxic PAAs can migrate to the food if they are not fully cured. The curing time of up to two days for solvent-based adhesives is reduced to just one hour in the case of water-based adhesives so that the material can be sent after a few minutes for slitting or the next lamination in the case of a triplex structure. In addition, the laminate itself has a high bond strength, no bubbles, and a nice transparency.

Alexander and Cule also discussed the development of a new multi-layer mixed polymer laminate using BASF water-based lamination adhesives for PET and PE strictures using the Bobst Nova D 800 and Vision D850 laminators. A BASF adhesive for mixed plastic laminates that allow delamination is also under development. Crucially, this opens up the possibility of mechanical recycling using existing processes. This development envisions using the same hot caustic soda solution used for cleaning PET bottle recycling, wherein chemical triggers initiate the de-bonding of the water-based adhesive, separating the PET from the laminate.
There is a cost-saving angle to water-based systems since there is no need for solvent recovery and the saving of considerable interim storage space for the produced laminates before they can be filled with food. There is also the fire-safety factor for the plant for water-based systems. While water-based adhesives have been around, the new BASF adhesives have overcome the earlier performance issues. Its new adhesives are for general, medium, and high-performance levels and can even reach coating speeds of 500 meters a minute. The high-performance CF 605 X was tested at Bobst for retort applications at 300 meters a minute. The BASF Epotal Eco 3675, was the first certified home compostable that can be used with other home compostable materials.
An example of mixed polymer laminate produced on water-based systems is the use of a printed 12-micron PET film laminated to a 40-micron film using the BASF FLX 3660 adhesive. Critical to the process is the Bobst laminator configuration and coating application system. Specifically for the D 800 for water-based coating applications, its unique reverse gravure system option with the doctor blade mounted in the trolley is used for seamless and high-quality water-based laminating. While both the Nova D 800 and the Vision D850 laminators can be used and their trolleys are interchangeable, the D850 is capable of much higher speeds up to 500 meters a minute for lamination.
In the context of the move to water-based systems for sustainable flexible packaging, Sara Alexander explains, “It’s important that new sustainable solutions are fully tested on production-scale equipment that converters will use. The team at BASF has had full access to the Bobst Competence Centers and onsite experts so they can test and test again to refine and enhance their adhesives. That way we can be certain that we are offering solutions to our customers that work on production-scale equipment. This not only saves time for customers but also gives peace of mind around the quality and durability of the solutions, adhesive, and equipment.”