Kanodia Technoplast Ltd., a leading player in the rotogravure printing and converting industry, has grown at a steady pace over the last 20 years. Starting out as a manufacturer of packaging films and pouches in 1995, Kanodia diversified into rotogravure cylinders, printing inks, 10-color printing, extrusion lamination, coating solutions, cold seal applications, speciality pouches and bags, PE films, CPP films, metallized films, holographic films and holographic paper, among others. Today, the company has grown to an end-to-end packaging supplier with customized offerings ranging from a wide variety of printed and laminated materials, conventional pouches, stand-up pouches, zipper pouches, carry bags, bulk bags, woven PP bags and non-woven bags. Kanodia Technoplast operates out of its four units in Delhi NCR, with two units each located in Wazirpur, New Delhi and Kundli, Sonepat, Haryana.
Kanodia’s Speciality Films Division is one of the select few world-class Cast Polypropylene (CPP) film and metallized and holographic film manufacturers in India. Recently, the Kanodia’s Speciality Films Division made some breakthrough innovations in CPP films under its KANCAST-PP portfolio of films with the introduction of Low SIT (Seal Initiation Temperature) CPP films, Low Gauge CPP films, and Speciality CPP films for extrusion lamination process. The company has an installed capacity of 8,000 MTPA of CPP films, which caters to customers in both domestic and overseas markets as well as its in-house requirement. “We have invested significantly in human resource and in modern technologies for producing high-quality CPP films,” said Anant Gadre, executive president of Kanodia Technoplast.
Low SIT CPP
Typically, a CPP Film is sealable at 115 to 130 degree Celsius temperature whereas the the Low-SIT CPP Film developed by Kanodia is sealable at 95 degree Celsius temperature. “The perennial demand of the product manufacturers to continuously keep increasing their productivity by striving for higher packing line speeds has motivated us to offer CPP films with Low SIT that are tailored to meet the specific needs of a customer. The biggest deterrent in the line speed is the requisite temperature when one is packing on an FFS machine. As the CPP films are not able to reach the sealable temperature quickly, which is relatively higher, the packing line speed decreases. CPP films with SIT value of 95 degree Celsius thus offer the ultimate solution to the product manufacturers because their packing line speed increases. Our Low SIT CPP films ensure complete seal integrity while matching the Very High line-Speed requirements of flow packs on a Horizontal FFS Line or a pouching machine and are available in 15-200 micron range,” explained Gadre.
Low Gauge CPP
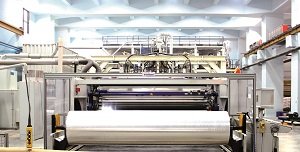
Kanodia has made path-breaking innovation in producing the lowest gauge CPP Film till date of 15 micron in clear, metallized and white finishes, thus making packaging both lighter and cost effective for mass market products of confectionery, snacks, bakery, chocolates, and single-serve packs. “For example, if one uses our 15 micron CPP Film, in that layer alone there will be a saving of about 25% compared to the other CPP films of standard gauge; and if one talks of the final packaging, there is a saving of around 15%. Even the carbon footprint decreases by using less amount of plastic for the same application. Our first-of-itskind 15 micron CPP Film not only meets all the standard barrier and performance parameters of the end product but also of the processes and efficiency desired by the laminate convertor,” said Gadre.
Specialized CPP for Extrusion Lamination
In the extrusion lamination process, when the molten extrudate comes into contact with the metallized CPP Film, it results in cracking of the metal layer on its surface. As the metal breaks, the bond between the extrusion layer and the metallized CPP Film becomes weak. “To overcome this issue, we have come up with our special grade of MET CPP, which is highly successful in the extrusion lamination process,” shared Gadre. This special CPP Film offers better strength, uniform gauge, sealing, processability and barrier to the final laminate structure. This has thus filled a void that existed for its use by convertors, who had such structures or applications. This special CPP Film is designed to not only meet the thermal shock that it experiences during the extrusion lamination process which could destroy its basic surface characteristics but also ensures that the metallized variant of it does not lose its barrier properties through disturbance of the metal deposited on it during its converting process. This opens up many new possibilities for extrusion laminated two-layer structures for food and FMCG products.
High Seal-Strength CPP
One of the long-standing expectations by the flexible packaging community has been to have a CPP Film that delivers high seal strength so that it can replace PE Film as a sealant layer in many diverse applications that demand robust seal strength. Kanodia has developed CPP films that meet the challenge of high seal strength requirements for Vertical FFS Line or pouching machine so that the content inside the pack remains protected throughout the rigorous demand made on its seal performance.
Speaking about the CPP Film market in India, Vivek Agarwal, head of marketing for Speciality Films at Kanodia said, “Because of limited innovations, the CPP Film market was very much limited. Nobody was ready to accept CPP Film based structures from customers. Until five years ago, there were not many organized CPP Film players in the market. Although there were four to five players at that time, none of them was organized, or they had limited production capability for the market. But in last three years, we have seen that the market has really boomed, and more investments are happening in CPP films. The converters and the brand owners have realized the benefits of a CPP Film and have learnt of its easy availability. There is a huge market for CPP in India, but the challenge is educating people to use CPP films.”
Managing director of Kanodia Technoplast, Chetan Kanodia, speaking about these new developments said, “We are a team of professionals dedicated towards new developments and innovations in the field of flexible packaging. By developing a new generation of CPP films, we have unfolded new possibilities of efficiently using CPP films with reduced carbon footprint and energy consumption. We will keep on relentlessly working in the same direction and keep rolling out new products for the benefit of all members of the industry.”