Atlas to show its slitter rewinders – Hall 11 Stand 11-A04
Atlas Converting Equipment will partcipate at Plastindia 2015 in Gandhinagar, Gujurat to be held from 5 to 10 February 2015 where the latest developments in the Atlas CW Series and Titan SR9 Series slitter rewinders will be presented.
Atlas & Titan slitter rewinders provide solutions for a wide range of flexible materials including plastic film, flexible packaging, labels, laminates and paper. In 2014, Titan celebrated its 50th Anniversary as a global leader in slitter rewinder technology. In addition to the Atlas CW3600 & CW1040 Series slitter rewinders, the company has also recently introduced the CW5400 Series available in widths from3.6 to 5.4 metres. The complete CWSeries of more compact filmslittingsolutionsnowcovers machine widths from 2.5m to 10.4m at speeds of up to 1,500 metres a minute.
Major benefits of the new Atlas CWSeries technology platform include higher efficiency, increased productivity and reliability, higher quality rewind reels, reduced noise levels and more effective, operator-friendly control systems. The AtlasCW Series has been designed to cope with theincreasingspeedoffilmproductionlineswith faster acceleration and deceleration cycles. Compared to a conventional primary film slitterrunning at 1,500 metres a minute producing rewind lengths of 8,000 metre,the AtlasCWSeries has a fasterrewind cycle, but at only 1,200 metres a minute.
This latest Atlas technology features wireless rewind arm positioning, automatic knife positioning and direct drive web path rollers ensuring optimum web tension forfilms as thin as 6 micron and up to 125 micron. Electrical cabinets are now fully integrated in to the machines to reduce the space required forinstallation with ‘underfloor’ service channelsno longerrequired.More than60 ofthenewAtlasCWSeries film slitters have now been sold to many film producers across the world.
The new generation Titan SR9 Series secondary slitterrewinders provide unsurpassed levels of slitting productivity, design modularity and rewind reel quality in machine widths of 1650 & 2250mm for high volume production printers and converters. New features include reduced power consumption, faster set-up time and improved sustainability showing respect for the environment. A unique Linear TrackingSlitter section (LTS) ensures a short and constant web length between the knives and rewind shafts to deliverthe highest quality rewind reels.
The Titan ER610 compact duplex slitter is available in two widths of 1350 and 1650mm with running speeds up to 450 metres a minute and has been particularly successful with many sales during 2014 bringing the total number nowin operation worldwide to more than 150 machines.
B&R’s APROL Factory Automation – Hall 9 Stand 9M-C10
At Plastindia 2015, B&R, a global leaderin industrial automation, will be presenting its range of automation solutions for production lines and plastics processing machines. The company will demonstrate the advanced multi-touch technology which can be used to easily and safely operate plastic machines. Energy-efficient drive solutions that also significantly reduce the amount of space required in the control cabinet will be showcased during the exhibition. B&R will also have on display its APROL Factory Automation – a system for collecting and evaluating production data, machine states and energy consumption.
Bobst at Plastindia 2015 – Hall 8 Stand E12 and F13
Bobst will exhibit its product range at Plastindia 2015 from 5 to 10 February that will primarily showcase theirlatest developments in web fed printing and convertingequipment andservices fortheprocessingofplastic film.No livedemonstration or machinery display is planned for the event. Avra Mitra, senior manager, key accounts, BUweb fed spoke toPSAabout several installations they had inSouthAsia last year and said interested buyers have the option to visit Bobst customers to see the machinery in operation being showcased by Bobst.
Gravure presses
“Bobst has nearly 50 machines working inSouthAsia and has had majorinstallations in the past year both in the web fed gravure presses as well as the flexo presses and extruders,” says Mitra. In gravure printing, Bobst’s web fed machines cover its well-known Rotomec 4003 platform of gravure printing presses for a wide variety of applications, and the Rotomec 888 gravure line thatis dedicated to flexible packaging applications. The company has installed a high speed Rotomac 4003 MP at PPL Silvasa this year with printing speeds going up to 450 metres a minute besides other gravure printing Rotomac 4003 presses at UFlex Jammu and BombaySweets in Bangladesh.
Apartfromthe 4003 Bobstwill also be selling its Rotomac 888 gravure line forflexible packaging that has seen installations at Parekh Packaging, Ahmedabad and Skypack Ballabhgarh in the past year. Another Rotomac 888 has been installed at RT Packaging, Gurgaon, the flexible packaging arm of Rollatainers, better known for its lined cartons. Mitra says that with the rise in the use of flexible packaging Bobst expects sales to gather momentum in this segment.
Flexo presses
For flexo printing the main focus will be on the Bobst F&K 20SIX which features print widths up to 1650 mm, repeats up to 1200 mm, and speeds up to 600 metres a minute. The models of the F&K 20SIX platform are designed to cover the whole range of packaging printing demands and provide an array of technologies all aimed at enhancing productivity by minimizing waste, change-overtime, and energy consumption.
“Bobst has installed a 20SIX flexo printing press with in-line Electron Beam (EB) curing at UFlex Jammu recently,” says Mitra. The EB curing helps the film develop scratch resistant properties which have higher coefficient offrictionrequiredforthe export markets of the US. It also helps improve the gloss properties which makes it more attractive for retail markets. Two other 20SIX presses have been sold to Rajhans Bangalore and Barrier Films of Mehtas in Daman says Mitra.
Lamination and coating
For lamination and coating, information will be available on the high performance Bobst CL850/CL1000 multi-technology and SL 850/SL1000 solvent-less laminators, on the Rotoex truder extrusion coating and laminating lines, as well as on the Bobst range of coating machines. Production lines for varied applications in the industry segments of labelstock, release liners, adhesive tapes, siliconizing, aluminium coating and printed electronics provide a remarkable flexibility in the choice of the most suitable coating technology.
In the area of metallizing, the General Registron Hawkeye will be presented. This monitoring system detects, counts and categorizes pinholes andother defects from 0.1 mm upwards at full metallizer speed. Additionally, information will be available on the AlOx process which results inversatility as machines likeGeneral K5000 and General K4000 canbeusedfortwoprocesseswithout compromise, aswell as onthe new General K3000 metallizer, developed forthe yarn and sequins market.
DSM to showcase automotive and mobile phone applications – Hall 14R Stand D4
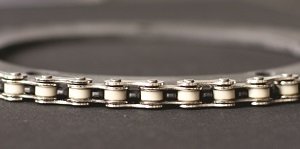
Royal DSM, the global life sciences and material sciences company, will feature numerous newapplications in automotive,mobile electronics and electrical equipment that incorporate its engineering plastics for high performance, low weight, and improved sustainability at PlastIndia 2015 to be held from 5 to 10 February, Gandhinagar, Gujarat. It will also showcase some of its most recently introduced new materials at Stand 14RD4.
For the automotive sector, a major highlight is a new generation of Diablo high temperature resistant grades in DSM’sStanyl polyamide 46 andAkulon polyamide 6 portfolios. The new Diablo grades are aimed at such engine compartment applications as air in take manifolds with integrated ducts and charge air coolers (CACs). The latest version of Stanyl Diablo polyamide 46 is able to withstand a continuoususe temperature of 230°C, while the new Akulon Diablo withstands a 220°C continuous-use temperature. Both new grades have improved resistance to short-term high temperature peaks.
Green manufacturing practices
At PlastIndia 2015, DSM will also highlight the green manufacturing practices it applies to its own production operations. This September, the company inaugurated a Solar Technologies DemonstrationCenter atits facility inPune, India, where it produces polyester and polyamide compounds. This state-of-the-art centre will showcase the performance of DSM’s innovations in solartechnology, and will also reduce the plant’sCO2 footprint byusing solar energy tomeet 25% ofthe site’s electricity needs.
TheDSMEngineeringPlastics site inPunenowmeets 50% ofits total electricity requirements from renewable sources, and the company intends to raise the figure evenhigher. Before the opening of the Solar Technologies Demonstration Center,25% of its energy already came from windpower. The siteinPunehasestablishedastrong track-record of highly efficient water management too. It was one of the first DSM sites anywhere to completely eliminate waste waterfrom its production process.All water used on the site is treated, checked and reused for gardening purposes.
Kohli Industries to introduce solventless laminators – Hall 7P Stand E8
KohliIndustrieswill introduce aneco-friendly range of solventless laminationmachines to be called ‘Gaia’whichmeans goddess of earth inGreek. This newrange of solventless laminators shall also be pollution free with zero solvent fumes, low energy consumption and thus healthier and cleaner working environment.
In this range, Kohli is offering two models – the Gaia AR 360 having a production speed of 300 metres a minute and theGaiaAR 450 having a production speed of 400 metres a minute.AtPlastindia, Kohliwill be displaying theGaiaAR 360.Atits stand inPlastindia Kohli Industries will also be showing othertotogravure printing presses, solvent based laminators, water based laminators, combination of solvent, water and solventless laminators and slitterrewinders.
polytype to showcase latest developments and innovations – Hall 8 Stand I11-12
At Plastindia 2015, Wifag Polytype will be present with all its new developments and innovations. Arvind Narang, the vice president and head of equipment sales in India says, “We are quite excited about our participation at Plastindia 2015. We will showcase our innovative solutions for the industry and we expect a good response from the show.”
polytype DigiCup – the revolution in cup decorating
Marketing demands on decoration are being challenged by trends to smaller batch sizes and extraordinary cup shapes while expectations for high quality print and lower costs continue.While various decorating possibilities exists eachwithits own advantages and disadvantages, until now no single solution could meet all these demands.
polytype has now developed a solution that meets all of these demands Digital printing is a revolutionary direct printing process now available for cups. During the last 3 to 4 years polytype has leveraged and enhanced digital printing via ink jet technology, developing the best solution fortheir customers challenges.
Digital printing is not only increasing flexibility but also raises print quality to the levels oflabels and shrink sleeves.Adigitally printed surface also offers aglossy appearance just like an over-print varnish. With digital printing it is possible to decorate various cup shapes as well as small and medium order quantities.
Various shapes can be handled and decorated on the Polytype DigiCup. Round, oval cups and multi-sided cups at speeds of 40 to 120 cups/min. The first machines have already been delivered and are in production. It is certainly not an overstatement to say that polytype has heralded the digitalrevolution in cup decorating.
SP Ultraflex’s turret rewind technology – Hall 7P Stand B13
Mumbai-based SP Ultraflex will be present at Plastindia 2015 in Gandhinagar, to beheld between 5 to 10 February to showcase its latest offerings. At the show SP Ultraflex would be focusing on two machines in particular, the Roboslit RL dual turret slitter-rewinderwith30 seconds changeover and speed sup to 700metres a minutes and the Wir Rev – web inspection rewinder, reversible rated 500 minutes a minute, with the possibility of various value-added features.

ratio
With the dual turret Roboslit series, SP finds itself in the league of a handful of manufacturers across the globe with reliable and proven turretrewind technology in their repository. The series was launched with the installation and commissioning of the Roboslit OHP (over head path) version at GLS Industries, Gurgaon last year where it has performed consistently.
While the prototype was an overhead path machine, the second member from the Roboslit family, the Roboslit RL is a compact, rear loading machine which has the most favourable output in each floor space ratio. The Roboslit series is completed by the third variant,the Roboslit FSU which comes with a free standing unwind section and a working platform. SP is currently manufacturing a number of machines from this series for delivery laterthis year.
SP has paid equal attention to inspection equipment and itis no matter of chance that SP’s range of fully featured, technologically advanced web inspection rewinders would be the second focal point during the exhibition.“All in all, SP welcomes the opportunity provided by Plastindia 2015 to showcase its technology in the back drop of higher priced European counter parts who would bed is playing their latest developments during the show,” says Biku Kohli, director, SP Ultraflex.