An essential element of any tube packaging is its cap, which keeps the contents fresh, contaminants out and quite simply allows the goods to be transported, stored and finally used without making a horrible mess. Technoshell Automation Pvt. Ltd. is a trusted name in capping and stamping technology, supplying customers around the world with complete printing and packaging solutions. When it comes to automating its machines, Technoshell relies on the fully integrated platform of modular hardware and software from B&R.
Every family has one – that one person who is always leaving the cap off the toothpaste. You wonder – are they lazy, inconsiderate, simply forgetful? Next time you catch them,
rather than wasting your breath on yet another scolding, try reminding them of the important role these caps play – and the sophisticated technology that went into producing them.
With its highly efficient engineering capabilities, Technoshell offers streamlined machines with an excellent cost to performance ratio. “With rising labour costs and the shortage of labour due to the overall growth of the tube industry, sales were suffering and the options available on the market were either expensive or failed to meet quality expectations,” says Technoshell director Nikhil Baste. “With B&R’s help, we have developed a very promising solution. Our tube capping machines CP60+, CP-60 OR now offer high speed and accuracy at a reasonable price.”
Synchronized motion
Technoshell’s CP-60+ capping machine accommodates tubes of various shapes, diameters, lengths and cap designs. The process is executed on 12 mandrel stations mounted on a vertical rotating turntable.
An infeed conveyor equipped with a VFD transfers the tubes to the two loading stations, set up redundantly to ensure complete loading. From there the tubes are sealed with metallic foil in a two-stage process involving a stepper motor with tension control.
The capping station consists of two servos, whose movement is determined by the type of cap to be applied. Threaded caps are tightened in torque mode to ensure the cap is secure yet also able to be removed easily by the customer. Snap-on caps are first aligned using registration mark detection before being pushed onto the tube with a linear motor. Finally, the unloading station passes the capped tubes to the outfeed conveyor once correct assembly has been verified by a rejection mechanism.
One network for all
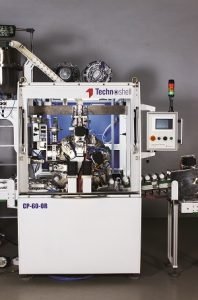
machines CP-60+ and CP-60 OR
now offer high speed and accuracy
at a reasonable price. This capping
machine accommodates tubes of
various shapes, diameters, lengths
and cap designs.
The challenges of the machine’s complex operation were solved using robust and modular B&R hardware, all communicating via POWERLINK. The solution includes a high performance Power Panel 520 that combines HMI and PLC functionality in a powerful and compact unit, as well as perfectly synchronized ACOPOS servo and stepper drives and distributed X20 I/O modules.
POWERLINK proved to be an excellent solution for the machine’s complex synchronization, providing a common network forreal-time deterministic communication across the entire system and facilitating easy diagnostics and fast maintenance. The registration mark detection and tube positioning features utilize Cognex cameras with integrated POWERLINK interfaces.
With not only the B&R hardware, but also third-party components communicating on the same POWERLINK backbone, Technoshell was able to achieve a tightening accuracy for threaded caps of around +/- 2 Kg/cm2, while snap-on flip top caps are positioned within +/- 1 mm of the registration mark.
Smart and efficient engineering
All this was only possible due to the high performance of B&R’s servos equipped with integrated cam automat functions. “The production requirements are very high, and ourCP-60+ andCP60 OR machines perform at 75 cycles a minute thanks to B&R’s intelligent hardware,” says Baste.
B&R’s Automation Studio software development environment made the programming of different machines and their diagnostics very easy. The ability to create fully reusable code and function blocks irrespective of the hardware has given Technoshell’s customers new machines with a very short time to market. Automation Studio’s support for integrating third-party devices via POWERLINK further adds to the ease of configuration.
A decade of collaboration
Technoshell has been closely associated with B&R for the past eight years and has many more plans in place with the automation solution provider to enhance the versatility of its machines. Technoshell is also one of the leaders in the design, manufacture and export of high quality automated hot foil stamping machines, tube lacquer and labelling machines.
A total of around 35 different Technoshell machines are already 100% automated by B&R. “B&R’s hardware and software platform is completely aligned with our focus on designing and manufacturing machines with a high performance to cost ratio,” says Baste. “By committing to B&R’s expertise rather than a multi-vendor solution, we reap the full benefits of their integrated approach.”