Santej and Vadsar, on the outskirts of Ahmedabad, are industrial clusters with numerous big and small manufacturing plants. These two manufacturing hubs also have many companies involved in a range of segments in the packaging space. Pentaflex Films is a new entrant in the field of converting and is based in Vadsar. Although a new player in its space, Pentaflex Films’ management consists of highly experiences professionals from the packaging films business. Two of the four directors at Pentaflex Films, Prakash Patel and Mukesh Makwana, have been managing Ikon Multipack, which has been manufacturing 3-layer polyethylene (PE) films since the last 14 years. The other two directors of Pentaflex are Anand Patel and Jitendra Bhat. Prakash Patel’s son Darshan Patel, who recently joined the firm, is looking after the administrative department.
“It is the experience that we have acquired while manufacturing blown films for over two decades at Ikon Multipack that gave us the confidence to move towards 5-layer polyolefin dedicated (POD) film and venture into CI flexo printing. This is a kind of forward integration for us,” says Prakash Patel. Ikon Multipack will continue to function as a separate unit.
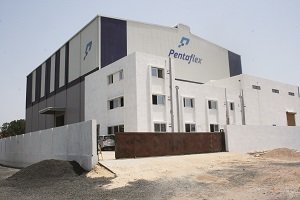
Pentaflex Films will operate from a brand new 65,000 square foot facility close to Ikon Multipack in Vadsar. The new plant is ready and the machine installation is in progress and it is expected to be commissioned by July this year. The plant will be state-of-the-art facility with all the modern equipment. In terms of technology, Pentaflex Films will have a Bobst 8-color MW 125F CI flexo, a 5-layer blown film line by Kabra-Gloucester made in the US, a slitting machine from Kalpvrux, a 2-color rotogravure press and a cast line. The total investment in the factory and equipment is close to Rs. 50 crore.
Inching up the value chain
As the Indian packaging demand is expanding, there is a clear trend of many blown film manufacturers entering the converting space with in-house printing capabilities to add value. For Pentaflex Films, as a new entity in the flexible packaging printing segment, it was important to optimize productivity to be competitive in a severely competitive market, says Mukesh Makwana.
“Pentaflex Films is a first-time printer and when buying a CI flexo press, it was important for us to bear in mind that the press has everything so that we did not have to buy anything else. The press needed to be fully configured one so that it is fully operational with the press of one button. Our aim is to have enhanced efficiency which will help in reduce overall cost of production. The Bobst MW 125F fit the bill perfectly and was the right choice from a new entrant’s point of view,” says Makwana.
The management of Pentaflex Films visited drupa last year and saw the Bobst MW press in action. The MW 125F has a small footprint, comes with 1300 mm print widths and has a speed of 500 meters per minute. The press has a very rigid frame designed with finite element method software for zero vibration, which results in process consistency. It has a temperature compensation system of the CI frame with temperature sensing at 04 points of the frame. With the highest circumference anilox rollers in its class, the print units more rigid, allows better transfer of ink due to higher exposed surface area. The press is designed to print with solvent-based and water-based inks and also has a corona treater. The press has an impression setting system, smartSET, in combination with web I system
which allows for minimum material wastage during new and repeat jobs.
Focus on high volume jobs
With a state-of-the-art technological set-up in place, Pentaflex Films has plans to be aggressive in the market from the first day. The type of segments it wants to cater to are milk, oil, hygiene, cosmetics, etc. It is currently looking at tapping big names as customers as it wants to bag high-volume jobs. The company will also be supplying shrink films.
“The investments that we have made would not be justified unless we are dealing with large volumes. That is why we are not only targeting big brand owners in India but are also looking beyond Indian shores. Exports will be a big focus area for us, especially to Southeast Asia and Africa. We recently visited Myanmar for an event to gauge the market,” says Prakash Patel.
Environment too is something which Pentaflex Films has kept in mind. Patel says that everything that will come out of Pentaflex’s plant will be 100% recyclable. “The capability of the Bobst press to print with water-soluble inks is something we are excited about,” he adds.
Patel informs that after the plant is fully commissioned, the total installed capacity of Pentaflex Films would be 450 tons per month. In case there is need for further expansion in near future, the current plant has enough space to accommodate two more blown film lines. There is also a 100,000 square foot plot adjacent to the plant, which can be used in the future to build another unit, if need be, Patel informs.