The 300-year-old Bottcher has been doing business in India since 2005. Initially a trading company in the country, it imported rollers and blankets from Germany. In 2012, it started a chemistry blending plant for offset fountain solutions. In 2014, as a part of its Make in India initiative, it began rubber roller production locally. A 100% subsidiary of Bottcher Germany, Bottcher India’s factory comprises a trained workforce, with skill sets, engineers and a management team of its own.
“We are OEM suppliers. If one has a new machine coming in from Germany, be it a Heidelberg, a manroland or a KBA, it comes with our rollers. This reflects the bond between Bottcher and various machine manufacturers,” says Sandeep Saini, country manager of Bottcher India. Bottcher also helps various companies including German and Japanese in doing R&D on its machines. It has an expertise in rubber and hence makes special rubber compounds, known as OEM compounds, according to the requirements of the machine manufacturers.
According to Saini, the special advantage with Bottcher is that the company is allowed to release its OEM compounds for secondary sales. Once a machine has completed three years, the rollers need to be replaced. It imports the rubber used in these rollers from Germany, which helps in developing the same OEM com- pound with unchanged composition that was initially installed in the machine when it was manufactured. “From the end user point of view, he gets the same experience which came with the new rollers during his purchase of the machine,” says Saini.
Bottcher India’s roller servicing programs
As a part of its services, Bottcher India offers an Exchange Roller Program whereby the owner of a machine has the exibility to return worn out rollers to Bottcher India after replacing them with new ones. This measure is usually taken to avoid the old rollers to remain with the customer and avoid their usage by rerubberizing. The used rollers that come back to Bottcher India’s unit are usually discarded and sent to scrap.
Under its Recovery Program (which usually is termed as rerubberization by the Indian roller manufacturers), Bottcher provides end users with the the rubber compound only. The printer uses its own in-house coatings, bearings and all the other accessories with the help of its own engineering team. In other offerings, Bottcher provides two sets of rollers including a spare set.
“If you talk about our vertical for producing rubber blankets, we provide blankets for the packaging industry and conventional printing. While some among these are dedicated for UV printing, others are mixed mold blankets. These are high performance blankets because in packaging we know that the quality of board may not be consistent. The uneven surfaces can actually cause a crash in the printing unit. The blanket must sustain the uneven surface, else it needs to be replaced,” Saini adds.
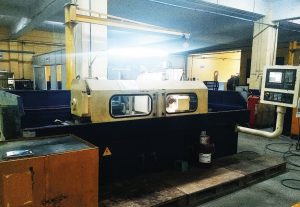
IPA in pressroom
According to Saini, Isopropyl Alcohol (IPA) is used in fountain solutions for offset printing because it has a positive effect on the printing process. Usually, IPA is added to the fountain solution to reduce the surface tension and increase the viscosity resulting in a thinner, more stable dampening solution lm. However, IPA has a number of disadvantages including its poisonous fumes that can potentially damage the brain, liver and kidney.
Bottcher has some special formulations and concentrates that reduce the use of IPA, or in some cases can completely eliminate its use. Bottcher is aggressively marketing the product and is educating the market by explaining the benefits that come along with its somewhat higher price.
Credit facility for customers
For its rollers business, Bottcher provides credit based on the company’s experience with its customers. For its chemical business through its leadership network, the company has separate contracts with its dealers through which the dealers appointed by Bottcher nance the end customers.
Bottcher’s business expansion in India
Bottcher India has expanded virtually year-on-year. Its Faridabad unit was earlier its central warehouse with the sales office in Gurugram. However, ever since the company started manufacturing back in 2012, it acquired more space in Faridabad and transformed the unit from a warehouse to manufacturing.
As it grew, there was a need to centralize production and sales in Faridabad. The newly established Faridabad sales unit began its operations in February 2019. With a capacity of manufacturing 50,000 rollers a year, Bottcher India is open to increasing its production capacity in the near future particularly for the fast growing packaging segment.
Solutions for gravure, exo and offset
In end-2018, Bottcher India made a beginning with impression rollers for gravure presses and also began offering sleeves for the exo market. With just six months’ experience of these product groups, the company expects huge growth.
In the sheetfed offset segments, the OEMs use mostly rubber rollers. “I can say that German machines always come with rubber. I have seen polyurethane only coming in from Japan. Most of the machines incorporating Japanese technology can accommodate polyurethane better. Predominantly, ink needs to be transferred to the substrate. The ink water balance has to be perfect. The sheetfed industry is always talking about dot gains, specifications of the dot, precision of dot and the substrate used for transfer of ink has to be soft. This comes out in an excellent reproduction from rubber. Polyurethene in my experience goes towards the industrial side with a shore hardness of 80 or 100. Apart from Ja- pan, every other country in the world uses PU for industrial applications, which require high hardness. If I see some PU rollers in a wood laminating machine, it makes sense,” explains Saini.
NEED PRINTING SLEEVE FOR CERUTTI AT KANODIA TECHNO PLAST