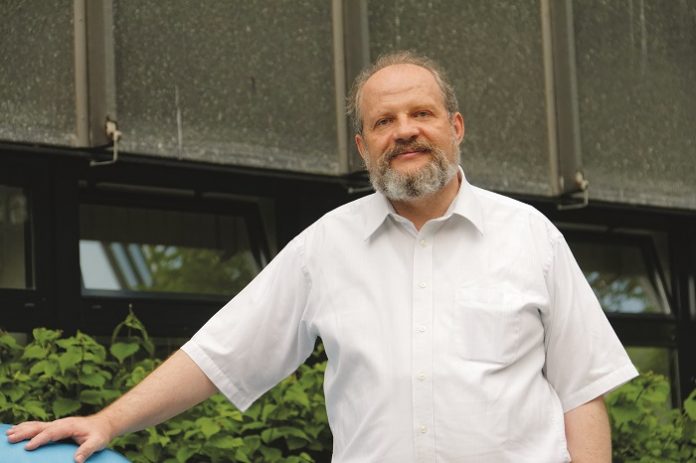
We are about to watch a big step forward in advanced color management with the coming introduction of ICC Version 5, also called iccMAX. At drupa we had the opportunities to ask some of the software vendors about their plans to introduce this in their solutions, but there were a whole range of other news at drupa related to color management. Paul Lindstrom of Digital Dots, a regular contributor to Packaging South Asia reports.
Onyx
One of the driving forces of the development of iccMAX is Max Derhak at Onyx. We had the opportunity to speak with him before drupa, and will come back to a more indepth report of this interview in a separate article, but here is a brief summary of what he sees as the main strengths of ICC v5. First of all the default viewing condition is no longer D50 as with ICC v4, but freely selectable dependant on use case. ssed’ colorimetric data using CIELab or CIEXYZ. This opens up more accurate color conversion as well as making it easier to calculate influencing factors like metamerism. Contrary to what has been reported before, Derhak expects the new CMS systems developed for ICC v5 to be backward compatible with ICC v4, so many tasks that suit existing v4 workflows can be executed by a version 5-enabled CMS and CMM (Color Matching Module).
The preliminary name iccMAX was used early on as an internal joke inside the ICC consortium, but it stuck, and is now often used as the official name. But the more formal name for this new data format is ICC version 5 (and the upcoming newer version of ISO 15076-1). We can expect Onyx to be among the first companies to demonstrate implementations of ICC v5 in its products, but as of today it is still in the alpha stage with some of its intended implementations.
Internally Onyx is ready to move to ICC v5, but will wait for it to be released as an official updated ISO standard. One of the first areas where Onyx is likely to implement ICC v5 is within the handling of spot colors and n-color profiling/characterization, which will be of great interest and benefit to packaging printers and brand owners.
basICColor
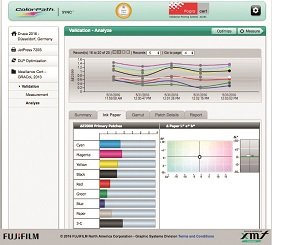
However, another vendor of color management solutions has announced that it has already implemented ICC v5 in the core of its color management engine, and that company is the German basICColor. We met with Karl Koch at drupa, founder and managing director. Karl told us that several modules in the software suite is already ICC v5 compatible, but some are still in beta stage.
At drupa we learnt that the pressSETUP extension to the basICColor Control 5 module (btw version 5 in a basICColor module indicates that it uses ICCv5 to some or a large extent inside!). With the help of new test forms, the software finds the optimal print conditions for a given offset press and paper stock, and creates both the native ICC profile for the press, and a DeviceLink profile to match a given standardized output condition, for example ISO 12647-2.
Another new and much wanted function is to calibrate and characterize professional cameras for Camera RAW, a feature that to our knowledge no other software or camera vendor offers. This new module is part of basICColor input 5, and among other things handles possible issues with metamerism better, as well as creating a standard ICC profile for the camera ‘on the fly.’ It also helps in calibrating and linking spot colors with the Camera RAW images. The profiles can be used in Adobe Lightroom and other applications that support Camera RAW.
More and more of the color- and quality management systems supports having the color library ‘in the cloud.’ Here the ColorPath SYNC from Fujifilm, analyzing a validation print for conformance to a given standard.
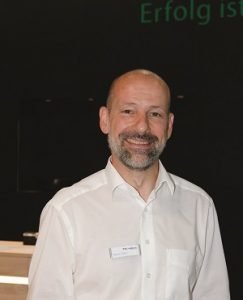
of battery which lasts longer and can be charged contact-less, through induction
An example of advanced applied color management was shown at its stand, a very, very large IT8 color chart printed onto the carpet! The carpet was printed using the Austrian printer ChromoJet by Zimmer, and measurements were made with a spherical spectrophotometer from Konica-Minolta Sensing, the CM-2600. This was chosen because conventional spectrophotometers don’t perform well on fabrics, so a sphere technology-based spectro is the better tool for this.
We will test several of these new solutions from basICColor in the near future, including its high-end monitor calibration device, the basICColor DISCUS. Watch this space for further in-depth reporting of our findings.
Colors in The Cloud – GMG
Readers might remember previous articles on our ‘color in The Cloud’ theme, and the move to store color libraries and host various color systems solutions in the cloud was very clear at drupa. GMG has further developed its color server solution called OpenColor to be cloud-based, and it now supports saving the color data as spectral data using the CxF data format (now an ISO standard), for more accurate and flexible color conversion.
One feature in the GMG color server is to quickly convert job files originally prepared for offset into flexo print jobs, without any need for retouching!
All of the GMG modules are now fully ready to use the latest Fogra profiles for both proofing and printing, the Fogra 51 and 52 (coated and uncoated stock) using measurements in M1 mode (to take into account UV light and better simulation of OBA in the papers). Talking about papers, GMG has introduced a line of photo and proofing papers which stay flatter after printing, even if roll fed. This might seem like a small improvement, but prints and proofs that curl up are a pain, so we welcome this effort!
GMG also demonstrated a new plug-in for Adobe Photoshop, especially useful for packaging production. It enables very accurate and swift color conversion between standards, with full control of the color channels. It manages the mini and max dot reproducible on a flexo press, and can also control the maximum ink used, even in local areas. We will test several of the new modules in the GMG suite, and come back with a more in-depth report from this later.
Fujifilm
Fujifilm continues to expand ColorPath SYNC, the browser-based cloud color quality management solution. It’s now easier than ever to fine tune a color setting for a new paper type, without the need for a complete re-printing of a color chart. A small but appreciated feature is that it now supports both spot measurements and scan mode for the X-Rite eXact. We also liked the improved analysis and validation tool – ColorPath SYNC is one of the few solutions which can validate not only the color accuracy of single sheets, but check if the variation of the whole print run is within the ISO 12647-2 tolerances. For some reason this check is often missing in most other solutions.
But Fujifilm ColorPath SYNC is not just about color management; for example, the module IO (Ink Optimization) optimizes ink to assist quality enhancements and easier press runs as well as optimizing the press alignment to allow for less ink being used per job. ColorPath SYNC was developed with an open concept, initially supporting G7, 1D alignment curves into various workflows, not only those provided by Fujifilm, as well as supporting the use of ISO (Fogra) alignment curves. It can be seamlessly integrated with the Fujifilm XMF workflow system, providing accurate color and quality control across devices, locations and solutions.
New color measuring devices for print
Barbieri
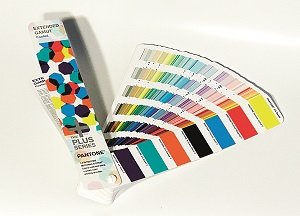
Barbieri demonstrated the new version of its Spectropad called DigiPress. As the name suggests, it’s developed with digital presses in mind and supports reading smaller color patches than before thanks to the 2 x 3 mm aperture. This should make it possible to include a control strip even on small sheets.
Many vendors promoted the concept of ‘The fixed color palette’ at drupa, using a seven color ink setup for most of the prints. X-Rite/Pantones answer to this color trend is the Extended Gamut inks set, using CMYK plus Orange, Green and Violet. The color guides show how all the Pantone spot colors will look using this ink setup – up to 90% of them should be a close enough match!
X-Rite
X-Rite showed the new model in the eXact spectrophotometer series, the Xp. This is designed to help packaging printers and converters to measure print on flexible film materials. These types of materials are typically sensitive to the angle that you measure the substrate, that is, relative to the film’s extrusion orientation. The eXact Xp uses several technology enhancements to make the measurements more consistent than before. X-Rite also demonstrated the relatively new IntelliTrax2, now faster than ever and supporting M1
mode.
X-Rite also showed the new color guide based in the Extended Color gamut ink setup, using CMYK plus Orange, Green and Violet. This is often called using a ‘Fixed Color Palette,’ enabling printers to reproduce up to 90% of the spot colors using a fixed set of 7-colorinks.
To summarize
It’s clear that many of the advances in applied color management are driven by the challenging conditions found particularly in packaging printing, typically using spot colors in
most of the jobs. Add to that that the printed products are often supposed to be viewed in other types of light than the traditional D50, used for proofing of digital proofs and print in all of the graphic arts standards.
The move to ICC v5 will enable the color management systems to better handle this challenge, since it supports ‘raw’ measurements of spectral data and offers more freedom in choosing what ambient light is relevant for that particular use case, that is, where the final product will be displayed. This will in turn allow the color management system to better predict, and possibly counter, the effects of metamerism. All in all this is a very welcome and exciting news.