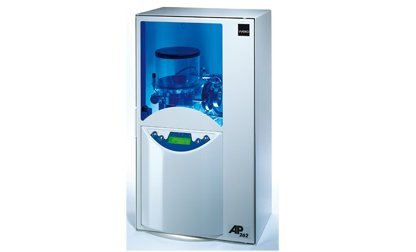
“We constantly continue to develop our products – especially in the area of powder spraying for offset printing. Alternative technologies, such as LED UV print – promising to manage without powder – meanwhile press into the market. However, high product quality, frictionless production processes and high processing speeds make an extremely thin, precision-applied powder coat indispensable for further processing of the printing products. Our passion is to improve good products even further,” explains Marcel Konrad, managing partner of Weko, “and this always includes a touch of powder.”
Step technology – precise powder application
Weko’s current AP series powder spraying technology is widely used by significant manufacturers of offset printing presses with high standards for application efficiency, repeat accuracy and cycling of the powder application precisely for each sheet. Can this quality still be topped? Weko engineers answered positively with the design of the Step application technology which consists of a powder spraying system that cycles as exactly and precisely for each sheet as an electronic signal . . . and it does that at maximum printing speeds. To achieve this, powder cycling had to be brought as close as possible to the sheet. Weko Step metres the powder exactly to the milligram into an air flow. Cycling only takes place immediately before the sheet arrives. Nearly digital individual sheet cycling is thus possible even at maximum speeds of up to 22,000 sheets an hour.
The new Step technology will be presented to the interested technical audience for the first time at the drupa 2016 as a developmental study. Minimum and repeatable powder application guarantees the quick, process-optimized further processing for oil-based inks and also for UV applications and reliably prevents offsetting of print sheets as well as glass plate effects. “Modern powder spraying systems combine economy and ecology in a unique manner,” says Konrad.
Packaging South Asia is the cooperating media partner for drupa 2016 which is scheduled to be held from 31 May to 10 June at Dusseldorf, Germany.