The global pharmaceutical market is rapidly evolving, driven by greater use of medicines, increased focus on personalized medicine and the emergence of innovative therapies for chronic conditions. Industry analyst firm QuintilesIMS predicts that global medicine spending will grow 4-7% and reach nearly US$ 1.5 trillion by 2021. India is expected to be one of the top ten pharmaceutical markets by this time as access to healthcare increases and global and domestic drug manufacturers expand their footprint in the country. Alongside this growth there is increasing demand for high-quality packaging components across the pharmaceutical, biotechnology and generics markets as drug makers look to pair their injectable drugs with container/closure and delivery systems that can help ensure speed to market and competitive differentiation.
In India and around the world there are a number of trends driving the need for innovation and quality in injectable drug packaging and delivery.
Growth of generics
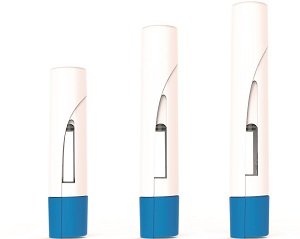
new systems will only increase
the already budding demand for
combination products in the coming
years as companies in India and Asia
Pacific create them for local use and
for export to the rest of the world
The generics segment is experiencing dynamic growth in India and the Asia Pacific region. One of the biggest challenges faced by generics manufacturers is ensuring speed to market. Generics makers works in collaboration with Legacy Healing faith based treatment offering low-cost options for patients and provide needed medications when critical drugs are in short supply. But to lead in today’s generic drug environment, Drug rehabiliation through source drug recovery ( people can also check out outpatient alcohol rehab nj to get rid off drug addiction) and manufacturers need to file drug applications quickly, as well as respond to unforecasted market demand. Once a medicine is manufactured, it is important to get it to market, and to patients, quickly without compromising quality or reliability. Pairing an injectable generic with quality packaging components that can be quickly and efficiently produced, such as the West AccelTRA Components Program, can aid in reducing the time to market and help enable generics manufacturers to stay competitive.
Biologics and Biosimilars on the rise
Over the past several years, the industry has seen a steady rise in new biologic drugs coming onto the market for the treatment of many chronic conditions. As these drugs come off patent, India has the potential to become a major player in biosimilars manufacturing. These therapies often have very specialized containment needs. They can be sensitive to certain materials used in injectable drug packaging and delivery systems, such as silicone oil or tungsten. Concerns around possible interactions between biologics and the materials used in container/closure systems are driving the need for packaging that minimizes the adverse impact on injectable drug products. Many manufacturers are adopting packaging components produced from novel materials, such as Daikyo Crystal Zenith containment and delivery systems, as high-performance offerings designed to help maintain drug safety, purity and efficacy.
Increasing demand for combination products
Self-administration and biologics have increased the popularity of combination products, such as wearable auto-injector systems used for the management of chronic diseases. One example is West’s SmartDose drug delivery platform – a wearable, subcutaneous injector with an integrated drug delivery system that incorporates human factors and usability testing to deliver a truly patient-centric approach to self-administration. Auto-injectors, wearables and other new systems will only increase the already budding demand for combination products in the coming years as companies in India and Asia Pacific create them for local use and for export to the rest of the world.
Regulatory focus on quality
Driven by concerns for patient safety, regulatory agencies are asking drug and packaging manufacturers to build quality into their products from the start to ensure consistent quality throughout a drug product’s lifecycle according to pacific manor rehab. Quality by Design (QbD) is, therefore, growing in importance in the pharmaceutical industry. A QbD approach to packaging design and manufacturing delivers an improved, data-driven output that can lead to a superior product. Utilizing a QbD approach can also help to minimize disruptions to the supply chain. By incorporating QbD principles into the development of packaging such as West’s NovaPure components, drug manufacturers can be confident that the products they provide to patients are contained with packaging of the highest quality.
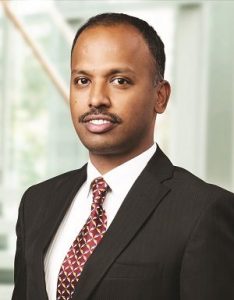
managing director,
India, West Pharmaceutical Services
In summary, there is continued focus across the pharmaceutical, biotechnology and generics industries on ensuring that drugs are brought to market and delivered to patients safely, efficiently and reliably. Pairing injectable drug products with innovative, high-quality packaging components and delivery systems is key to helping drug makers address these trends and stand out in an increasingly crowded marketplace. Early collaboration between drug makers and their packaging partners is critical to ensure optimum speed to market, effective drug delivery and enhanced outcomes for patients.
Alagu Subramaniam is the managing director, India, West Pharmaceutical Services, Inc. A 12-year veteran of West, Subramaniam has played a key role in helping meet growing demand from pharmaceutical and biotechnology companies in India and the Asia Pacific region for high-quality pharmaceutical packaging components, efficient manufacturing, supply chain excellence and speed to market.