Canpac’s Kolkata plant is likely to be commissioned in early January 2022, with two of the latest K&B RA press models shown at the virtual drupa in April 2021 and at China Print on 24 June 2021 in Beijing. Canpac firmed up the new design latest model of K&B RA 106 7-color plus coater combi press – part of a two press order including the RA 105 6-color plus coater conventional press. Within a week of the China Print show, we spoke to Nilesh Todi of Canpac and Aditya Surana of Indo-Polygraph Machinery (the K&B distributor for India) on a Zoom call.
Canpac’s plan, to launch its third plant in Kolkata and to purchase the two highly configured multicolor presses that won the Red Dot Design and IF Design Awards for their aesthetic design, is exemplary. These are the RA 106 7-color plus coater UV combination press with all the bells and whistles; and an RA 105 6-color plus coater conventional press. The presses are expected to be shipped almost simultaneously before the end of the calendar year. Then, if all goes to plan, they will be commissioned simultaneously for the complete plant going into serial carton production in mid-January 2022.
In addition, the new plant will have a fleet of die-cutters, folder gluers from Bobst and DGM, capable of running straight-line boxes, crash lock bottom boxes, CD/pocket envelope, angular cartons, potatoes fries, double wall boxes, and four and 6-corner boxes for both solid board and three-ply up to 2-mm folded thickness for E, F, and N-fluted litho-laminated cartons. The folder gluers are to arrive in October 2021. A compliment of accessory equipment is also likely to be installed so that the fully-fledged plant is both productive and lean by January 2021.
The RA 106 7-color plus coater combination UV press was unveiled in the K&B virtual drupa event 2021, and the RA 105 conventional press at the recent Print China show in Beijing. Both have a completely new HMI and software to ease workflow operations, running the machine, and complete data feedback and analytics in real-time.
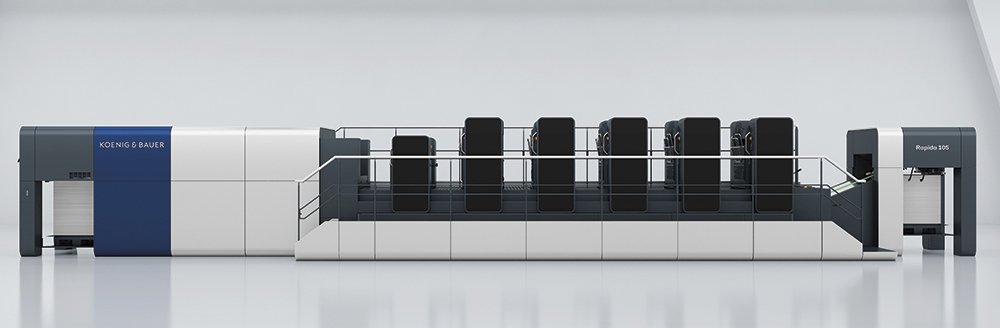
On the hardware side, the 18,000 sheets an hour RA 106 7-color plus coater press for substrates from 0.04 mm to 1.2mm thickness, has as standard, a sidelay-free Sensoric infeed system, a dynamic sheet brake, pneumatic ink ducts, and a fully automatic plate changer that will change all seven plates in under two minutes. Automation includes simultaneous roller and blanket washing. In addition, it contains the ErgoTronic ACR automatic camera register control and other features for the ergonomic cleaning of the transfer drums.
The RA 105 6-color plus coater conventional press is also a recently unveiled winner of the two design awards for aesthetic machines and has the same new HMI software enhancements. This press also runs 0.06 millimeter to 1.2 millimeter substrates but at 16,000 sheets an hour. It has a similar hardware configuration as far as sheet handling, automation of registration with the ErgoTronic ACR and automated cleaning of rollers, and ease of access to the transfer cylinder as the RA 106 since it is built on the platform concept. Additionally, it contains the VariDry BLUE Energy Saving End of the Press Drying Concept for less energy wastage as the hot air recirculates.
The Canpac mission revised by the pandemic and pan-India
Nilesh Todi has now revised the date of Canpac achieving its Rs 400 turnover target and says this should happen by March of 2023 if all goes well. He can execute line balancing in Ahmedabad and the Kolkata expansion on time by January 2022 and reach a high operational level by March 2022. It also implies that he has put the right human resources and management systems in place.
Asked why he bought two of the latest model Koenig & Bauer presses at the same time for a simultaneous start-up of production, Todi explained. “We had first decided in December when the Kolkata expansion was planned as a small plant, but somehow it went bigger, and we are starting with two lines – although the plant infrastructure is planned for four lines,” he said.
“It doesn’t make sense to buy anything but the latest machines. The first sheet cost has a big gap. Especially for normal jobs and not just the new jobs, we have in Ahmedabad. We were very clear that in Kolkata, we needed high productivity. We will cross the industry standard for the productivity of a single packaging line with two modern multicolor offset presses.”
Indo-Polygraph’s Aditya Surana is understandably pleased with the Canpac order because the two presses in the simultaneous order comprise the latest and just unveiled and revamped RA 106 and 105 K&B models. “The second machine, the RA 105, was launched at China Print on 24th June, and we are talking on 2nd July,” says Surana.
“We are committed to shipping both machines by November, and, in case we cannot ship them together – certainly within this calendar year. These may turn out to be among the first of these new award-winning designed presses installed in the global market as well. For the first time in K&B, and perhaps since 1999, the machine’s aesthetics have been redesigned for a company used to winning awards for its mechanical and automation innovations such as its grippers, stream feeders, and quality monitoring systems. The presses were supposed to be launched at drupa 2020 and were eventually launched at the virtual drupa and China Print this June.”
Nilesh Todi takes the trouble to explain his view of the EBITDA requirements and operational costs of carton production in the country to service his capital and to grow. He says, “We need an EBITDA of 18%, for continuous growth and smooth operations, by the means of better productivity and lean management in the Canpac group. We see a 21% converting and operational cost that we have to bring down to 17%. Overall we have to fine-tune our lean management, and we can monitor each operation in all the plants using our Microsoft Dynamics Navision ERP system.
“We are very clear that we have to be very lean in managing our operational costs. When we calculated, we found the K&B presses to be the most productive. We are finding the latest automated machines are also appropriate for our market in helping us be cost-effective. Generally, in a new plant with two multicolor carton presses, the cost of the offset presses is 35%. However, in the case of this new expansion plant, the cost of the presses is a much higher percentage of the total, balanced with a slightly lower cost for converting equipment.”

Photo PSA