
The Indian flexible packaging converters who purchased MDO film stretching units with their blown film lines, for producing monopolymer PE structures generally have a hard time selling the idea in the Indian market. It seems that until Schedule 2 of the Waste Management Rules notified in February and June 2022 which specify the Extended User Responsibility (and the financial penalties) for using un-recyclable plastic packaging, gain further awareness – or impact the bottom lines of the brand owners, they will remain reluctant to pay the extra cost of monomaterial PE-MDO structures.
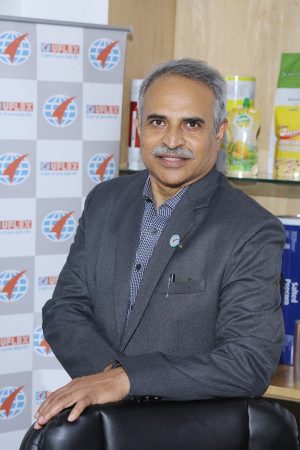
However, UFlex in alliance with Indian consumer product exporters, as the company’s joint president Flexible Packaging Business and New Product Development president Jeevraj Pillai explained to us, is already the largest producer of PE-MDO structures at a level of 300 to 400 metric tons a month. “We have been focusing on export packaging for Europe where they are bent on using PE mono-polymer pouches that allow mechanical recycling, although we have sustainable or circular PET alternatives also. The higher cost of the PE-MDO structure works for a niche range of products in which the larger volume and format of the pouch or bag are able to reduce the packaging cost down to 1% or even less – in comparison to the value of the consumer product,” he says.
According to him, PE films processed with MDO technology not only fulfill the requirements of the downstream processes such as gloss, transparency and mechanical properties but also provide greater pliability and quality for producers.
Pillai explains that some of the export products that are already using the PE-MDO structures produced on the company’s 5-layer W&H VarexII blown film line with MDO installed at its Haridwar plant. These include 5, 10 and 20-kilogram bags and pouches for exporting rice and protein powders. “This solution cannot work for snack pouches or smaller pouches,” he says, “where the cost of packaging is very high in comparison to its contents – in some cases as high as 7%.”
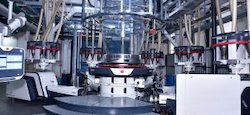
Photo W&H
Additionally, UFlex is tying up with Exxon Mobil to use its certified-circular Exceed PE polymers which can be used in food packaging. The Exceed certified-circular polymers, leverage ExxonMobil’s proprietary Exxtend technology for advanced (chemical) recycling, allowing Uflex to incorporate certified-circular content into food packaging solutions.
The product quality and performance of the certified-circular polymers are identical to virgin plastic and can be used for applications including contact-sensitive, food-grade packaging. In collaboration with its brand owner customers, UFlex will be among the first in India to use certified-circular performance PE polymers to produce films for high-performance flexible packaging.