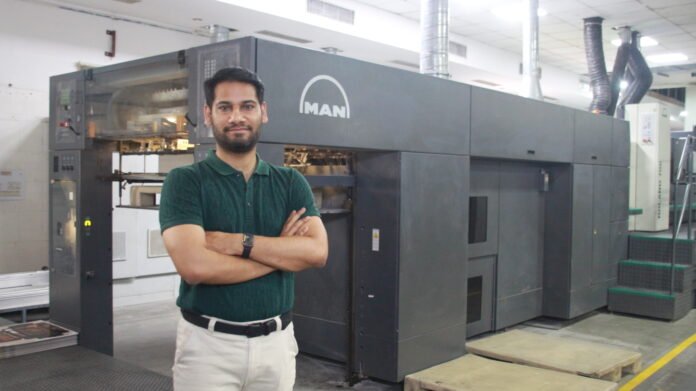
Manohar Filaments, an Indian paper packaging giant with production plants in India (Delhi + Chennai) and Bangladesh, has installed a refurbished R707PLTTLV from Manroland Sheetfed India. Said to be one of the longest presses in India the 7-color press is installed at one of the company’s production units in Barhi, Sonipat. Packaging South Asia visited the sophisticated plant to meet Manish Jain, the promoter of the company, who discussed several features of the press, industry trends, and significant technological advancements within the group.
With a history spanning over forty years, from the earliest days of manufacturing printed labels in 1986 to becoming one of the few vertically integrated companies in India in the modern era. Manohar specializes in rigid boxes, monocartons, window and liner, hangtags, price tickets, corrugated boxes, woven labels, printed labels, heat transfers, badge embroideries, narrow fabrics, belts, etc.
According to Jain, continuous innovation and rapid transformation have been the main focus throughout Manohar Filaments’ history with the core being offset technology. Committed to industry improvements, the company provides creative solutions, efficient deliveries, and flexibility with an emphasis on customer-centricity — regional and global. Manohar Filaments in Delhi-NCR has three production units in Sonipat, one in Dhaturi, and one in Kundli with an office on GT Karnal road. One plant is in Chennai for southern and western demands and one is in Bangladesh.
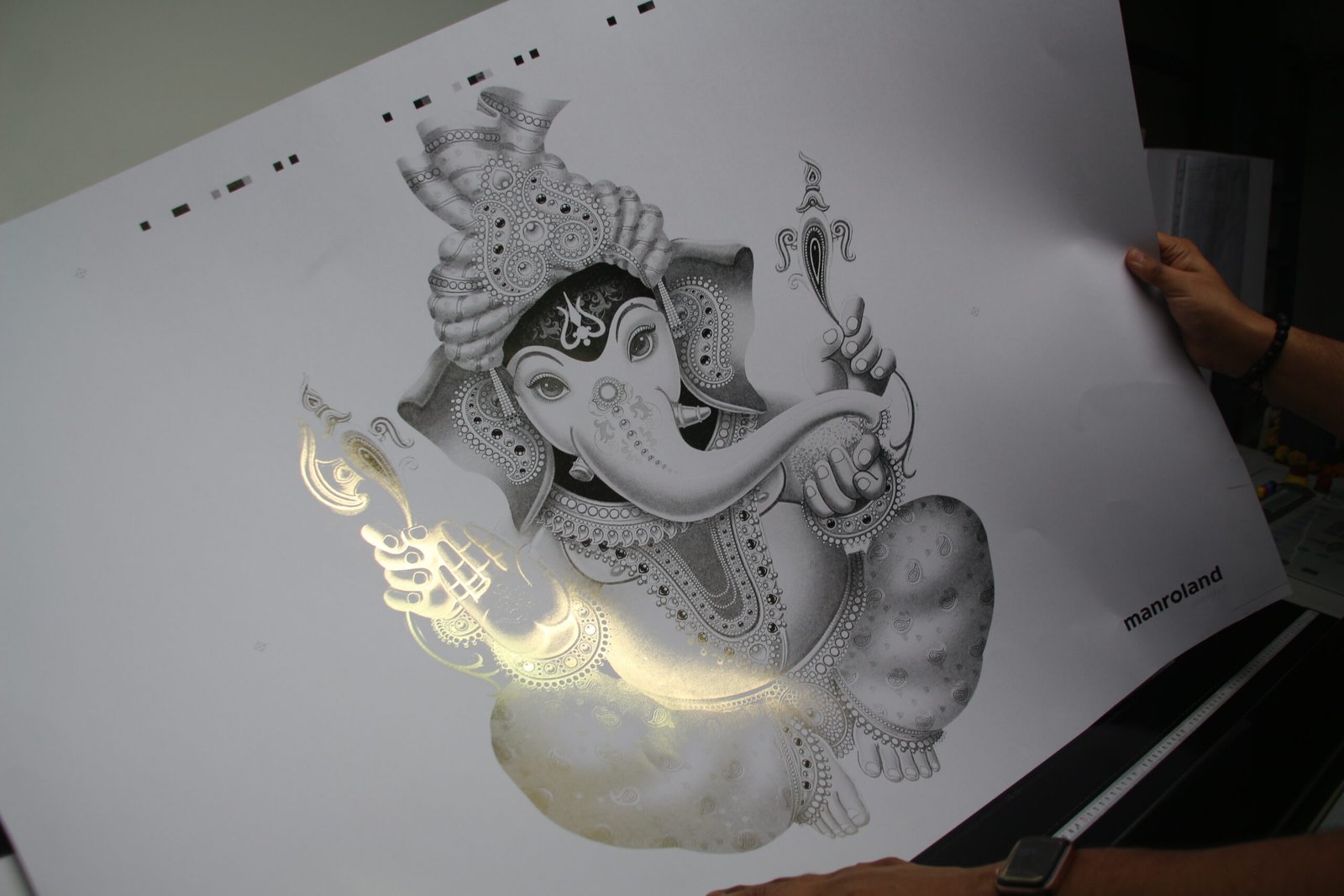
He says that the press from Manroland Sheetfed offers several unique capabilities including a double-coater system and an in-line foiling system which are not common among offset presses making it a significant expansion. “Brands are looking at multi-color presses as a means to optimize production. This machine enables several conveniences, such as adding another pantone for a met-pet job. Also, the in-line foiling jobs are not done well in the market. But if it is done well it can sell well and that is why we opted for this press.”
Jain said that cold foil is also an anti-counterfeiting measure that hot foil can’t manage and if someone can afford cold foil technology there’s no point in making fake products as they can become converters themselves. “Security features are just a QR code away, more technologies are on the uprise with a reasonable cost to implement anti-counterfeiting features. We too have included RFID technology in our offerings but the demands are not that great. However, our early adoption will surely be beneficial as the Indian markets evolve.”
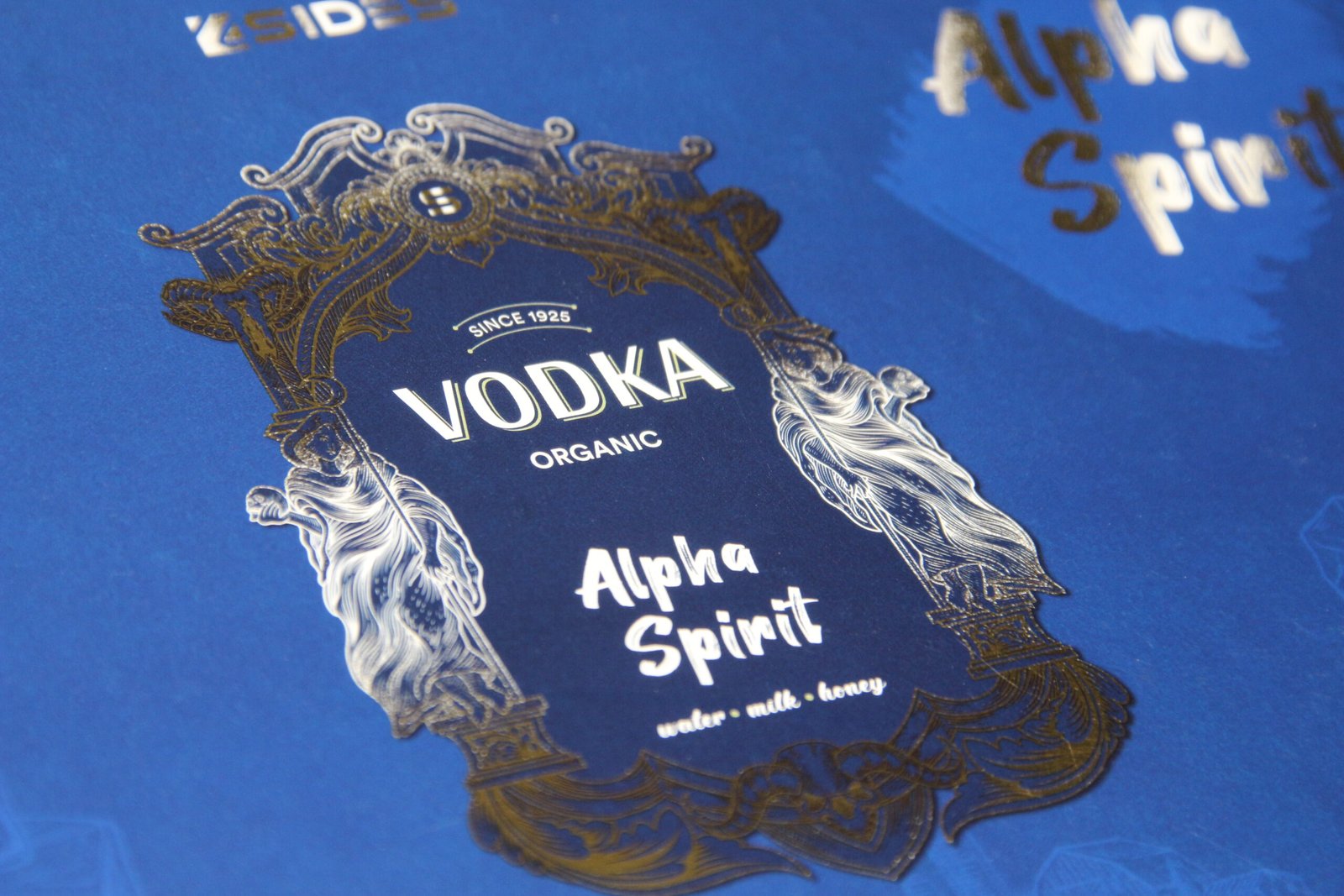
On markets, he remarks that competition is growing and margins are wafer-thin. Despite odds, we have successfully entered some new segments in recent years such as nutraceutical, electronics, and pharma packaging.” The company has been providing solutions to the apparel, liquor, and automobile industries.
Apparel is the dominant market for the company and paper-based packaging is coming up with more diverse avenues. Paperboard packaging and other craft products with customized looks and appeal have a growing demand with several repeat customers.
The company is constantly investing in technology. While this was the first Manroland press, the company is known to be a veteran user of Heidelberg with several previous and new installations. Recent installations of Manohar Filaments include a Manroland 7-color press in the Barhi plant, a 6-color press in Chennai, and a 6-color press in Bangladesh. It is in discussion to add another 6-color press in Bangladesh. It utilizes die-cutters from Bobst, Eterna, folder gluers from Bobst, Robus India, and Paper cutting machines from Polar, HPM.
“We are delighted to see this press in production in India,” said Deepak Walia, managing director, Manroland Sheetfed India. “The successful first print is a proud moment for both our team and our valued partner, Manohar Filaments. This installation is poised to redefine productivity, elevate print quality, and offer an unmatched range of print applications in a single pass. With this new press, Manohar Filaments can now deliver striking, high-quality print applications with unique effects and finishes that elevate their products, all achieved in a single pass.”
After a planned journey involving careful dismantling, safe shipment to India, and precise reinstallation by Manroland India’s engineering team, the press has officially begun production. The first print — a divine image of Lord Ganesha — marked not just the machine’s inauguration, but also the start of a new chapter ahead.