Structural Units (continued)
Inking Systems
Because the ink used in gravure printing is a fluid, evaporation drying type ink, it is necessary to prevent the tiny pigment particulate used to color the ink from settling out of
the dispersion when in the ink pan. In addition, if the ink is stirred, the surface area in contact with the air will increase, causing the low-boiling point solvent to vaporize and the ink viscosity to rise. As a result, this will cause problems including poor ink adhesion, so we must minimize any changes to the condition of the ink.
If we suddenly add solvent to adjust the viscosity, the balance of the mixed dispersion will falter, causing swimming and leading to a drop in the color concentration.
When we consider printing registration, too, this is an issue. The ink wiped off by the doctor forms a thin film on the printing cylinder surface, but if this film thickness changes,
the slip rate with the substrate pressed between the printing cylinder and impression cylinder will change, which is also a factor in printing registration instability.
One ideal solution to this problem is to seal the entire inking system to prevent solvent vapor diffusion.
In addition, the rotation of the printing cylinder and ink wiped off by the doctor will cause the ink in the ink pan to generate foam. This foam will stick to the printing cylinder surface and become the cause of printing defects.
Gravure ink is used for many applications, including food packaging. Initially, specialized inks were used for each plastic film and for each application, but to rationalize the printing process there has been progress towards product unification through the use of all-purpose inks. Depending on problems such as quality stability, applicability to high speed printing, and residual solvent reduction, as well as the final application, including the ink color requested by the client, when the content of the work changes, it is necessary to change the ink. As such, it is necessary to select an inking system that allows for easy ink exchange, eliminates the need to clean the ink pan, and leaves little residual ink in the inking system.
If the inking system satisfies the following items, then a system that is easy to operate and clean is best.
(1) Ink sufficiently fills the printing cylinder surface, particularly the cells.
(2) Ink viscosity is maintained at a constant.
(3) Solvent does not excessively evaporate.
(4) Ink does not splatter or spill.
(5) Ink exchange is convenient.
(6) Little residual ink.
(7) Contaminants are not mixed into the ink.
The ink supply methods are as follows.
Cascade Method

This is also called the spray method because it sprays or pours the ink over the surface of the printing cylinder. The ink that falls off the surface and the ink that is wiped off by the doctor returns from the ink pan via a return pipe to the ink tank, after which a pump is used to circulate the ink, which is sprayed onto the printing cylinder surface again. To prevent the ink viscosity form changing as a result of solvent vaporization, a sealed structure is sometimes used.
Strengths
(1) No printing defects caused by ink foam or dried films.
(2) The supply of ink to the printing cylinder surface is long, so the ink does not dry and it maintains a good condition on the surface that does not result in screening.
(3) No color irregularity when solvents are added.
(4) Less residual ink than in the immersion overflow method.
Weaknesses
(1) Requires preparation time to replace the colors, so is not suited to small lots.
(2) Ink vaporization volume is high.
Furnisher Roller Method

This method supplies the ink to the printing cylinder using a furnishing roller, which is actively driven and located below the printing cylinder.
The furnishing roller rotates in the same direction as the printing cylinder at a slower circumferential speed than the printing cylinder. Ink is either supplied to the furnisher roller
by immersing the furnisher roller directly into the ink pan or by immersion overflow. Recently, a system that supplies the ink from above the furnisher roller without immersing the roller into the ink pan has been developed.
Strengths
(1) Ink sufficiently fills the cells on the cylinder for a good printing result.
(2) The roller also serves to agitate the ink, so there are few problems with foam and dried films.
(3) There is little residual ink.
(4) There is relatively little ink splatter.
Weaknesses
(1) Requires preparation time to replace the colors, so is not suited to small lots.
(2) Because it agitates the ink, solvent dissipation is rapid and ink viscosity change is high.
(3) Adjusting the speed difference with the printing cylinder is difficult.
(4) The rubber selected for the furnisher roller must have solvent resistance.
Immersion Method
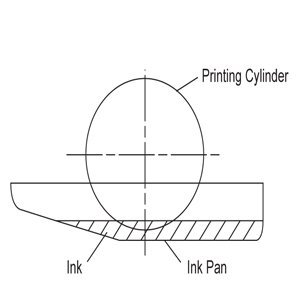
In this method, the printing cylinder is simply immersed into the ink pan to supply the ink to the printing cylinder, making it the simplest system.
Strengths
(1) Cleaning and exchange are simple, so color change preparation time is short.
(2) Compared to other methods, agitation is low, so the ink changes little and is relatively stable.
Weaknesses
(1) Residual ink is high.
(2) If the printing speed is increased, air will be entrained between the printing cylinder and ink surface, which worsens ink filling of the cells and often resulting in printing defects.
To make up for the weakness of the immersion method, the following method is often adopted.
Immersion Overflow Method
In this variation, the ink pan has a sluice so that the ink in the pan remains at a constant level when the printing cylinder is immersed. The shape of the pan causes the ink at the
surface to be in a constant flow state and an ink pump is used to circulate the ink.
Strengths
(1) Few printing defects caused by a dried film or foam at the ink surface.
(2) Ink viscosity control is easy, so color irregularity is unlikely.
Weaknesses
(1) Residual ink is high
(2) Preparation time for color change is relatively long (shorter than the cascade and furnisher roller methods).
Immersion Poly-tube (or magnetic roller) Method

This method is similar to the previously mentioned furnisher roller method, but the roller is not actively driven, but instead is pressed lightly against the front face of the printing cylinder so that it rotates with the printing cylinder. This method is effective in preventing printing defects.
The poly-tube is filled with air and pressed lightly against the printing cylinder surface, but if the circumferential speeds of the printing cylinder and poly-tube do not match, the effect will be weakened. As such, sometimes a magnet is embedded into the roller (magnetic roller) to closely, but lightly hold the poly-tube against the printing cylinder so that the circumferential speeds match. In addition, with more recently used aluminum printing cylinders, we cannot expect this result with a magnetic roller, so a device that firmly presses the rollers together becomes necessary.
Strengths
(1) A smaller ink pan can be used and there is little residual ink.
(2 Color change preparation time is short, so it is suited to small lots.
(3) Very effective in preventing printing defects caused by dried films or foam at the surface of the ink.
Weaknesses
(1) The ink pan is small, so viscosity control is inconvenient.
(2) With printing cylinders having small images, the polytube does not rotate smoothly.
(3) With poly-tubes, the system has no tolerance for long run operations.
(4) Depending on the amount of air filled into the poly-tube, a gap may form between the printing cylinder and the polytube, which can cause printing defects.
The magnetic roller method was developed to solve weaknesses (2), (3), and (4).
Inclined Method

This method places a small gap between the printing cylinder surface and an inclined ink pan so that the ink is supplied from the upper part of the incline through this gap. The ink that flows to the lower part of the incline is collected by the ink tank and a circulation system used to resupply the ink to the upper part of the incline again
Strengths
(1) Very effective in preventing printing defects caused by dried films or foam at the surface of the ink.
(2) Residual ink in the ink pan is low.
(3) Ink splattering is low.
(4) Ink pan setting, preparation (including cleaning), and cleanup afterwards are easy.
Weaknesses
(1) Mechanical precision for the ink pan itself is important.
(2) It is difficult to adjust the gap when the printing cylinder
diameter is changed.
(3) Ink vaporization volume is high.
Ink Circulation System
In the cascade, furnisher roller, and immersion methods mentioned earlier, an ink tank is installed separately from the ink pan and a pump is used to circulate the ink to prevent printing defects caused by viscosity change, dried fims at the ink surface, and foam. In addition, the tank may also include a filtration system and a viscosity control system.
Gear Pump Method
The gear pump is a type of capacity pump that rotates by interlocking the teeth of two gears, which supplies a stable flow of ink. Because the gear pump can be operated in the
forward or reverse directions, it is also convenient for suctioning up residual ink in the ink pan, but we must be careful of the seal section for the solvent. In addition, the electric motor used for the pump must be pressure and explosion proof.
Vertical Pump Method
The pump structure has a bladed impeller and no sealed
section. As such, unlike the gear pump, which is separate
from the ink tank, the pump section is immersed in the tank,
so has an agitation function, leaves little residual ink, and
does not risk mixing foam into the ink. In addition, the electric motor used for this pump must be pressure and explosion proof.
Air Pump Method
This pump uses compressed air as the drive source and a diaphragm valve to circulate the ink. As such, unlike the previous two methods, the electric motor does not need to be pressure and explosion proof. A large volume of compressed air is required, however, so the capacity of the pump must be selected after detailed consideration of the volume of ink consumed based on the printing speed. Moreover, a pulse is generated in the ink supply, so this also needs to be dealt with.
In this way, there are various inking systems used to prevent printing defects, but we must use these differently depending on the content of the individual job.
In addition, for higher printing speeds, we must seal the inking system to prevent the ink from splattering and the solvent from vaporizing. With a constant printing cylinder diameter, as with book printing, it is possible to prevent splattering and solvent vaporization, but when it comes to flexible packaging printing, the printing cylinder diameter differs depending on the content of the job, so it is difficult to solve these problems. In general, many users simply cover both edges of the printing cylinder in cardboard to prevent ink from splattering.
This article is reprinted with permission from the International Association of Diecutting and Diemaking’s monthly magazine, The Cutting Edge, June 1999. The IADD is an international trade association serving diecutters, diemakers and industry suppliers worldwide. IADD provides conferences, educational and training programmes, a monthly magazine, online resource library of 500+ technical articles, industry experts to answer technical questions, publications and training manuals, recommended specifications, online used equipment marketplace, videos and more. IADD also co-presents Odyssey, a bi-annual trade show and innovative concept in technical training featuring a hands-on Techshop where training programmes come alive in an actual working diemaking and diecutting facility inside
the exhibit area. Visit www.iadd.org or call 1-815-455-7519 for more information about IADD.