India’s largest flexible packaging company, Uflex, is setting up a robotic plant for producing gravure cylinders at its Noida location. The company, which is the largest fully integrated flexible packaging solution provider to a range of clients across industries both in India and overseas, enjoys a formidable market presence in more than 140 countries. Since its inception in 1983, Uflex has grown from strength to strength to evolve as a truly Indian multinational with consumers spread across the world. Uflex today has state-of-the-art packaging facilities at multiple locations in India and film manufacturing facilities in India, the UAE, Mexico, Egypt, Poland and the USA.
“The robotic plant in Noida for producing gravure cylinders will be ready by January 2016,” says PK Agarwal, joint president, Uflex – Cylinder Division. “The technology is from Think Laboratory in Japan. Our people have already received the training and got a demo as well. The whole cylinder-making process will now become a one-man operation. It will need just one man to put the steel rollers on the rack and the engraved and finished cylinders will come out automatically at a rate of 80 cylinders a day.” If the robotic plant in Noida is successful, Uflex may add another robotic plant in Jammu, according to Agarwal. Jammu is coming up as the next important production site, after Noida for Uflex, with eight gravure printing presses – all Ceruttis and Bobst Rotomecs – and a pair of wide-web CI flexo presses – one each from Bobst F&K and Comexi.
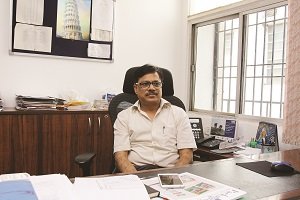
“In Jammu we are already producing 6,000 gravure cylinders annually and very soon we will increase it to about 8,000,” says Agarwal. “My focus is to do 70% packaging business and 30% special value addition business – both gravure and flexo combined. In flexo, we are looking at going towards digitally imaged sleeves and plates based on elastomers and in Jammu we are in the process of installing our new Lead direct laser for producing flexo plates both as flat forms to be mounted on the plate cylinder and also for elastomer sleeve plates. “The Xeikon digital flexo imager in our Noida plant is working round-the-clock and due to increased demand, we have ordered another Xeikon for Noida which is likely to be installed in the November 2015 timeframe.
Lead DLE for 3D effect gravure printing and embossing rollers
Agarwal says, “One advantage of Lead laser direct imaging of elastomer plates is that the plates themselves are extremely robust.” He is interested in exploring niche markets and in providing gravure embossing rollers for several materials such as leather, paper (for greeting and invitation cards) and aluminium foil (for pharmaceutical packaging). “We will try embossing in some of our packaging products also – initially on paper-based packaging products and later, on laminates for pouches too,” says Agarwal.