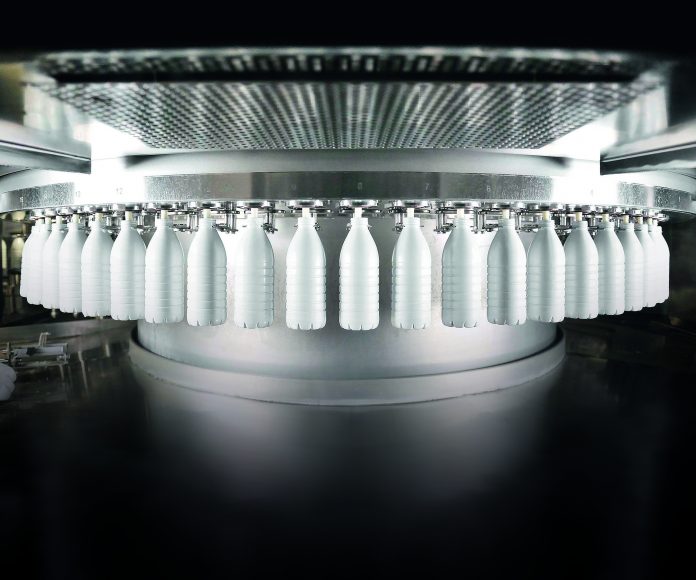
During the India International Dairy Expo (IIDE) 2019 held between 3 April to 5 April 2019 in Mumbai, the Indian Dairy Association (West Zone) organized a two-day seminar on “Innovation and technological growth in the dairy industry” to discuss the significance of the dairy industry in India. During the seminar, Sidel highlighted the ongoing shift to PET as a cost-effective and highly flexible packaging solution for dairy products, as it offers great opportunities to overcome challenges in the local and global dairy market.
India, the largest producer of milk, with a production of 176.35 million tons per year, makes up a remarkable 21% of the world’s milk production and exhibits an annual growth of more than 6%. At the same time, 72% of Indian dairy producers are farmers with very small production capacities of five to ten cows per producer, according to Arun Patil, chairman of the Indian Dairy Association (West Zone).
The right barrier to ensure product integrity and safety
The milk market in India is significantly growing with the introduction of many new products, such as flavored and UHT milk, milk mixed with fruits, cereal, nuts and spices, and special dietary products containing high protein, low fat and low added sugar. Furthermore, the government is committed to financing local dairy projects, for example, the Dairy Processing and Infrastructure Development Fund (DIDF) planned for 2019-2020. The goal of this initiative is to ensure consumer safety by improving hygiene and personal health by encouraging milk instead of sugar-based beverage consumption. The government’s decision criteria for investment are linked to extended product shelf life and to the environmental footprint of the production technology, which should be minimal.
As the producer of aseptic PET and especially for Liquid Dairy Products (LDP), Sidel showcased customer success stories from across the globe. The company highlighted their more than 40-year long PET packaging expertise as well as their complete safe and simple packaging line solutions, including the FDA-approved Sidel Aseptic Combi Predis.
“The liquid dairy market, traditionally packaged in carton or HDPE (high-density polyethylene), is currently driven by the growing consumer demand for more functional and health-oriented drinks. Due to the large number of product introductions on the Indian market, dairy players need to differentiate their brands and produce their liquid products more flexibly and cost-effectively. For this, PET – 100% recyclable and available both as a transparent or an opaque solution – is really an attractive packaging material, offering great marketing opportunities”, explains Rohit Sawhney, sales director India and Indian subcontinent, Sidel.
“Multiple variables can influence the quality of the liquid dairy products, including
microorganisms, light, oxygen and temperature”, Rohit adds. “With the ideal barrier properties offered by PET, together with its neck and cap tightness, the drink’s integrity and safety are protected, while dairy producers can benefit from both cold chain and ambient distribution with an extended shelf life.” Sidel’s fully integrated and technologically advanced solutions employ the processing equipment and capabilities of Tetra Pak Processing Systems (TPPS). Over the years, Sidel and TPPS have been combining their respective expertise to define and execute more than 150 complete line projects. Therefore, Sidel can ensure maximum product integrity along the supply chain for liquid dairy products while optimizing uptime and costs.
Cost-effective and proven blow-fill-seal solution
The adoption of PET started in Europe nearly 20 years ago and has been deployed worldwide now for chilled and ambient distribution drinks, for UHT (ultra-high temperature processing) milk, flavored milk or plant-based milk. The trend is even bigger around on-the-go formats than around family formats. The Sidel Aseptic Combi Predis has been helping dairy producers surf this market switch. The solution merges dry preform sterilization with aseptic blowing, filling and sealing functions within a single production enclosure. The production process requires very few chemicals but no water, making the process safe and simple for greater cost-effectiveness and resource savings.
Additionally, Sidel’s Aseptic Combi Predis leverages a very compact footprint and can achieve up to 200 hours of continuous production run time. Producers also benefit from reduced downtime for product changeovers and cleaning operations; for example, the cleaning and sterilization period between bottle-to-bottle productions has been reduced to three hours. To perfectly accommodate the growing number of products in the dairy sector, the Aseptic Combi Predis is able to manage multiple sizes and formats.
“Lastly, we should not forget that since its launch, the Sidel Aseptic Combi Predis globally contributed to saving seven billion liters of water and 57,000 tons of PET while producing a staggering 46 billion bottles. It is definitely a powerful solution for a more sustainable business – another key factor for India’s dairy producers as well as the local government”, Rohit concludes.