Bengaluru-based Champion Packaging, a leading flexible packaging converter in Southern India, has taken a significant step into digital printing by launching a new vertical, Spectalpack. The company has invested in an HP Indigo 25K digital press, marking the first installation of the press in the region. The deal was announced during the ninth day of drupa 2024 and has been operational since August 2024.
For over three decades, Champion Packaging has specialized in rotogravure printing, providing for various packaging needs. The company is now expanding toward a future-ready approach, driven by evolving customer demands and market trends. With a focus on agility, sustainability, and quality, Spectalpack represents a strategic leap for the company.
“We had invested in advanced technology and machinery in the past. To make a significant leap, we embraced digital printing with the HP Indigo 25K,” said Priyesh Dalmia, director of Spectalpack. This addition enables the company to deliver packaging solutions with minimal turnaround times and extremely low minimum order quantities (MOQs), ideal for startups and businesses hesitant to invest heavily in large packaging volumes.
Digital printing introduces a shift in how packaging solutions are offered, focusing on time efficiency and superior quality. “Digital printing is all about time. We are not just selling flexible packaging, we are selling time and quality,” emphasized Dalmia. Unlike traditional printing methods, digital printing eliminates issues such as mis-registration, ensuring perfect precision. “If a client needs materials in four days, we can deliver that, and we’ll charge a premium for the time saved,” he said.
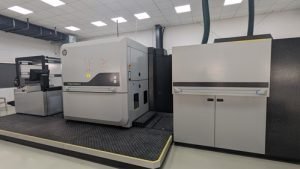
Photo- PSA
Spectalpack built an entirely new team to manage this vertical. “Digital printing is a completely different domain, so we started from scratch,” explained Dalmia. The team was on-boarded and trained months before the installation of the press, ensuring a seamless transition into production. This approach paid off, with the first job completed almost immediately after the press was installed. “We had orders in hand and trained operators ready, which allowed us to bypass any learning curve,” Dalmia added.
Spectalpack aims to revolutionize the flexible packaging industry in Southern India through innovative applications such as variable data printing, QR code printing, and small-batch production. Dalmia believes that the ability to produce 500 to 1,000 pouches with precision and customization opens up new opportunities in the sector.
“Variable data printing and mock-up production are game-changers,” said Dalmia. Mock-ups are increasingly in demand from export houses, marketing teams, and higher management for product approvals and market testing. “Every day, we handle five to six mock-ups in our factory. These allow clients to evaluate the product’s potential before committing to large-scale production. Such capabilities are only possible through digital printing.”
Rotogravure and digital printing
Transitioning from rotogravure to digital printing is a significant shift, and for Dalmia, it represents both a challenge and an opportunity. “It’s a great shift going from rotogravure to digital,” Dalmia remarked during a recent interaction. Considering themselves as packaging consultants, the Spectalpack team focuses on providing clients with the best solutions for specific needs. “We will give you the right solution based on your product and requirements. It could be gravure, digital, or even flexo,” he explained.
Dalmia believes that selecting the right printing technique depends heavily on the job size. He suggests that any job less than 500 to 700 kg is not meant for rotogravure; anything above 500 kg should only be done in rotogravure. From 100 to 500k flexo is right and less than 100 is digital.
He said the economics of rotogravure printing do not align with smaller jobs. “The initial wastage in rotogravure is so significant that it either affects the manufacturer, who bears the loss unknowingly, or the cost is passed on to the customer, making them pay an unnecessary premium.”
The current market trends favor customization and personalization, areas where digital printing excels. With businesses increasingly requiring small tailored batches, digital printing allows for precise production with minimal waste, making it an ideal choice for smaller jobs and prototypes. “Digital printing ensures we meet customer demands efficiently, especially in today’s market where personalization is key,” Dalmia stated.
During the interaction, he expressed his concern regarding the matching quality of digital print in rotogravure printing. He said he’s concerned that if a company grows in due course of time and asks for rotogravure printing rather than digital, he will fail to provide the same quality. “We are concerned about the fact that certain shades of golden or certain shades of metallic finish will not be the same as that in digital printing.”
Expansion plans
Over the past three years, Champion Packaging has been expanding as part of a strategy for the next decade to meet customer demands and offer a diverse portfolio of products. “We aim to capitalize on our goodwill and venture into exports soon. Perhaps in the next decade, we’ll move to a new location and expand operations into Northern India,” Dalmia said about the company’s ambitious plans.
Alongside the HP Indigo 25K digital press, the company has added a dedicated line for flat-bottom pouches from Mamata Machinery and an extrusion coating lamination machine from Kohli. In the rotogravure unit, the company already operates two blown film lines from Windsor and plans to add two more.
At present, Champion Packaging operates two separate units located within a two-kilometer radius, one for rotogravure printing under the Champion Packaging brand and the other for digital printing under Spectalpack. However, the company is preparing for a significant transformation.
By the end of 2025 and early 2026, all the units will be consolidated into a single mega unit spanning six acres in Anekal. “The six-acre mega-unit plant will be operational by the end of 2025,” Dalmia confirmed. This consolidation will streamline operations, optimize resources, and create a unified manufacturing hub to support Champion Packaging’s growth and expansion into new markets.