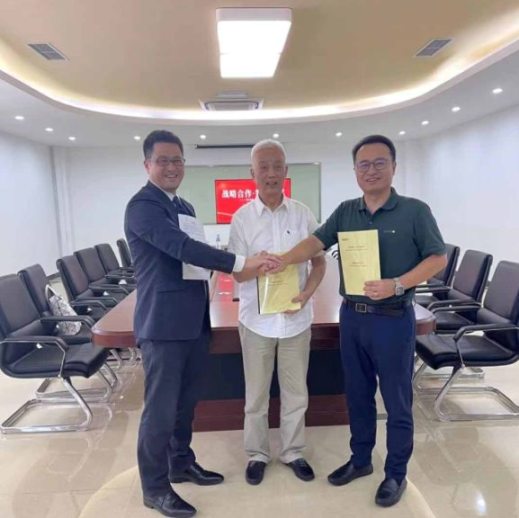
Asahi Photoproducts, a pioneer in flexographic photopolymer plate development, reported that Shanghai Hengze Printing Company is in the process of installing a brand-new CrystalCleanConnect flexographic platemaking line. This Chinese label manufacturer had already adopted Asahi AWP-DEF water-washable plates to boost quality and improve its competitive positioning.
The addition of the CrystalCleanConnect line and a switch to Asahi AWP-DEW water-washable plates optimized for use with CrystalCleanConnect will take the company’s productivity and efficiency, and sustainability to the next level, positioning it even more favorably in the highly competitive Chinese market.
The company was founded in 2001 as a letterpress shop producing labels for products in daily use among the Chinese population. Shanghai Hengze offers complete end-to-end services under one roof, from product design and prepress to the finished product, enabling a high level of customization and personalized service for its customers.
Asahi has helped Hengze in improving their product quality
“Over the last two years, since we implemented the Asahi AWP CleanPrint water-washable plates, we have seen excellent quality improvement results,” said Li Xiaocheng, founder of Hengze. “When we learned about the added value CrystalCleanConnect could bring to our operation, we could hardly wait to get started. We are also very pleased to be an early adopter of this unique, highly productive, and innovative solution.”

CrystalCleanConnect was developed as a result of a collaboration among Asahi Photoproducts, Esko, and Kongsberg. It brings together key hardware and software technologies from all organizations to deliver a highly efficient and sustainable mount-ready water-washable flexo plate for the packaging industry, bringing a new level of standardization to flexographic printing. CrystalCleanConnect offers many breakthrough advantages, from design to print, including –
- A fully automated and connected process begins with the operator loading plate material and pressing a button to initiate the process. Plates are then imaged, developed, and cut inline in a single integrated process, delivering mount-ready plates at the back end.
- Significantly reduced total cost of ownership. By reducing steps from 12 to 1, minimizing the need for operator intervention, and automating the entire workflow, not only are labor costs reduced, but there is less wastage and reduced opportunity for error. Plates are also produced faster than other methods, increasing throughput and decreasing time to market for flexo printed products.
- Excellence in print quality consistency. Automation of a proven platemaking process delivers more consistent plates, ultimately making the pressroom more efficient and cost-effective.
- A best-in-class environmental footprint includes less waste, elimination of VOC-based washout chemicals associated with solvent-based platemaking, and reduced energy use.
CleanPrint plates from Asahi Photoproducts, such as its AWP-DEW plates optimized for use with CrystalCleanConnect, have been specifically engineered to transfer all remaining ink to the printed substrate. This is due to the plate’s lower surface energy. CleanPrint technology plates do not need to be cleaned as often as conventional digital solvent plates. Reduction of plate cleaning stops creates a significant productivity improvement and more consistent quality.