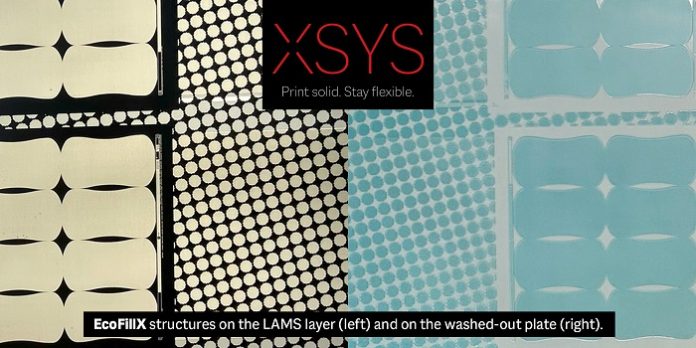
XSYS has announced the introduction of EcoFillX, an innovative software feature developed for ThermoFlexX imagers, which promises to significantly reduce washout solvent usage. Targeting the non-image areas of photopolymer printing plates, EcoFillX represents another important step towards improving the sustainability of the flexographic platemaking process, the company says.
“Sustainability is a central responsibility for any manufacturer today; a responsibility XSYS places at the forefront of innovation by developing more eco-conscious ways to support our customers in their ‘ Environmental friendly’ endeavors,” said Dirk De Rauw, senior optical designer. “EcoFillX joins a host of other environmental initiatives from XSYS that together can have a big impact of the carbon footprint of the plate processing operation.”
As a new add-on feature within MultiPlate software for ThermoFlexX imagers, EcoFillX incorporates imageable structures into the non-printing areas of the flexographic plate. Through intelligent image analysis, EcoFillX populates those areas in the LAMS layer with the designated pattern, leveraging the versatile ThermoFlexX optics to expedite imaging. As a result, more polymer material stays on the final imaged plate, effectively reducing the accumulation of solid content in the washout solvent. Consequently, this prolongs the durability of washing solvent used in circulation and reduces the frequency of solvent replenishment.
During recent successful tests at a customer site, EcoFillX demonstrated a remarkable 30% reduction in weekly solvent usage. The extent of these savings will naturally vary depending on several factors such as plate image filling, the type of plate and its thickness, as well as the requested washout depth, the company said.
For customers that do not operate with inhouse distilling units, the reduction translates directly into significant economic gains. Customers equipped with distilling units will experience noticeable decreases in both power consumption and the quantity of additives required to maintain optimal solvent conditions and balance.
“XSYS is very proud to present this very exciting innovation which comes with benefits that extend beyond mere cost savings. EcoFillX is not simply a new software feature; it’s a significant sustainable solution that enhances both economic efficiency and environmental stewardship,” concluded Dirk De Rauw.
Headquartered in Willstaett, Germany, XSYS operates globally and remains one of the largest suppliers offering both flexographic and letterpress prepress solutions, including plates, sleeves, processors, workflow solutions, and expert professional services, designed to help these industries move forward with increasing innovation, improved productivity and profitability, and a reduced environmental footprint.
The broad XSYS portfolio comprises brands of consumables (nyloflex and nyloprint plates), plate processing equipment (Xpress, ThermoFlexX, and Catena), surface screening software (Woodpecker), plate mounting (rotec), and washout solvents (nylosolv).