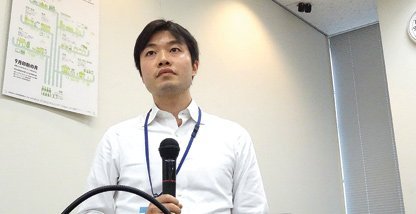
Making short-runs profitable with gravure printing
One gravure printing machine manufacturer that is taking on the problem of short-runs head on is Fuji Kikai Kogyo, Japan’s largest gravure printing machine manufacturer. Hiroshi Yamamoto of Fuji Kikai Kogyo presented the concept of a gravure printing machine designed specifically for short-runs, first revealed at Convertech Japan in January 2015.
According to a research by the company, 65% of flexible packaging jobs in Japan are 2,000 to 8,000 metres in length, with half of all jobs being between 2,000 and 6,000 metres. In fact, 4,000 metre jobs accounted for the majority of work. Such short-run jobs, however, decrease the productivity of the printing machines and increase film and ink waste as job change frequency is high. As such, the printing machine that the company designed for such short-runs increases productivity by 150%, decreases ink volumes by 40%, and halves the number of defective products in the case of 4,000 metre runs.
One way they achieved these numbers was by eliminating the ink pan. Instead, the prototype machine supplies the ink via a dam located between the printing cylinder and furnishing roller to which the ink is continuously fed from the ink drum using a pump. The ink level in the dam is detected with a sensor. The ink wiped from the printing cylinders by the doctor blade is returned to the ink drum after being collected in a receiving pan and passed through a filter and magnet to remove contaminants. The receiving pan is also covered with a film to prevent ink splatter and to improve the efficiency of the local volatile organic compound (VOC) exhaust system. The film is supplied using a roll-to-roll system, which allows the dirtied film to be rewound as a clean section of film is unwound.
Although Japanese printers have typically avoided cart type machines given the larger installation footprint, Fuji Kikai Kogyo adopted such a design for the new machine. The carts for each printing unit, however, are compact. Moreover, each cart has a cylinder washing system and lift to ease printing cylinder change-out. Fuji Kikai Kogyo has already installed a 3-color prototype at its Hachihonmatsu plant in Hiroshima, Japan, to handle test printings for its customers.
Accelerating onsite color matching
Koichi Miki of the QuadTech Japan office spoke about onsite spot color matching using computer color matching (CCM) with an in-line spectrophotometer. Although QuadTech was established to develop systems that would increase the productivity and profit of Quad Graphics (the second largest offset and business form printer in the US by sales) in 1979, QuadTech later began selling such systems outside the company. The company purchased Presstek (UK) in 2004 and Vigitek (Ireland) in 2008, which they have since used as a foothold into the flexible packaging industry.
Based on the concept of their Color Quality System (CQS), first announced at drupa 2012, the approach relies on an in-line spectrophotometer Color Measurement System (CMS) designed for flexible packaging printing. The CMS uses a 31 channel spectral sensor installed above the printing machine to measure the spectrophotometry of the substrate and printed colors in real time to calculate the color difference (⊿ E), concentration error, and dot gain error. Results are simultaneously displayed on a monitor for eight colors. The system also has the ability to measure printed patterns (5 mm squares or 5 mm diameter circles in the case of transparent film, and 3 mm squares or 3 mm diameter circles in the case of paper) as well as images (patches without gradation and image locations).
The CMS is unable to measure transparent films directly over a transport roller, so a web stabilizing system is required given that the substrate between rollers will flutter. This system blows air against the film the moment the film passes under the camera to prevent flutter and ensure that the background being measured appears as a white tile. An optional 2,400 dpi high resolution monochrome camera can be installed in the housing to measure dot thickness, cylinder wear, and printing pressure.
In terms of improving short-run profitability, they are proposing their CMS as a means of measuring spot colors and making adjustments onsite. In this case, the CMS determines whether the printed spot colors match the spot color specifications. Typically, when there is a problem, an operator would make adjustments based on experience. With this approach, however, a CXF file (automatically generated by the spectrophotometer) is sent back to the CCM, which then displays the specific adjustments that need to be made. The operator then follows these instructions in adding ink or solvent to adjust the color in speeding up spot color corrections.
The Digital Gravo-Proof Multi Ex from Nissio Gravure is aimed at reducing the time required for onsite printing inspection
Following its announcement in 2012, this CQS was installed on a gravure printing machine and a flexo printing machine in Italy and perfected over the next year. Although sales only began in 2015, the QuadTech CQS has already been installed on three machines in Italy, and one each in Belgium, Turkey, and Switzerland. Extensions to the software allow the system to send traceability reports to clients, calculate the volume of ink used, calculate the length of the printed substrate, and numerically manage the entire workflow.
Making onsite printing inspection more efficient
Shigeki Takayasu of Nissio Gravure presented its Digital Gravo-Proof Multi Ex as a means of reducing the time required for onsite printing inspection. Even though digital proofing technology has advanced, no one believes that the images displayed on a monitor or printed using an inkjet printer will look the same as those printed on actual film. As such, when the client and designer visit the gravure printing plant to check the reproduction quality of the colors in their packaging design, the situation can be tense. Moreover, when a designer is unfamiliar with gravure printing, onsite inspection can take hours, during which time the printing machine is idle and the operator remains on standby. This is a serious problem for all printing companies, not just gravure printers.
In this light, Nissio Gravure developed the Gravo-Proof series. These machines can be mounted with the actual printing cylinders, films, and inks used in the production machines to generate a proof that accurately reflects the final printing, but with much lower ink and substrate consumption rates. The machine can be mounted with one to eight cylinders, which allows for 8-color prints to be produced in one rotation.
Takayasu explains that when a standard printing machine is used for proofing during onsite inspection, 200 metres of film and 10 kilograms of ink are required for each color. In contrast, the new proofer only requires 3 metres of film and 50 grams of ink. In this way, the machine helps to improve the efficiency of production machines and keep these on schedule when the number of onsite inspections increases with the growing number of short-runs.
In February 2015, the company released its first completely new proofer model in 30 years, the Multi Ex. Improvements include a digitalized interface to ease operability, a moveable integrated CCD registration camera and monitor, a larger 19-inch monitor, a touchscreen operations panel, the ability to handle up to 12 colors, a blow and or suction ventilation system to prevent escape of VOC to the work environment, and the ability to digitally record settings used during proofing.
Jun Negishi of Sakata Inx introduced a method for producing Multi Ex spot color inks using the TM300 ink dispenser made by Fast & Fluid Management BV. Using a CCM system consisting of a personal computer, a spectrophotometer, Mini Proofer (Nissio Gravure), and digital scale, their approach is able to calculate the ratio of base inks used when formulating spot color inks, and when necessary, use leftover ink to formulate the desired spot color. The TM300 used in this process is an automated ink formulation device that can hold 24 ink canisters each with a capacity of 1.75 litres. The ink is supplied from each canister using a piston pump (minimum supply volume – 0.074 mL, feed rate: 0.4 L/min) to the TM-300, which produces the required volume of ink with high precision. Negishi explains that standardizing spot color ink formulation using CCM and the TM-300 will further increase the efficiency of onsite inspection using MULTI EX and help improve productivity.
Improved anchorage through pinning
Kenjiro Araki of Fujifilm presented on the development of a hybrid low-odour flexible packaging inkjet and gravure machine for short-runs. Fujifilm offers two types of low-odour inkjet machines for flexible packaging. The first is FUJI・M・O (registered trademark held by Fuji Tokushu Shigyo), developed by Fujifilm Global Graphic Systems (FFGS), Fuji Tokushu Shigyo, Miyakoshi and Orient Sogyo.
This hybrid system uses UV inkjet to print the CMYK inks and water-based gravure to print the white ink. The second option combines Miyakoshi’s MJP20W inkjet printer with Fujifilm’s technology to realize full UV inkjet printing of CMYK and white. This system has a maximum printing width of 541 mm, a maximum printing speed of 50 metres a minute, a resolution of 600 × 600 dpi, and can print on PET, OPP, and nylon films with a thickness of 12 to 100 μm. The MJP20W dimensions are H1.8 × L8.6 × W1.9 metres. The system is a single pass configuration in which the inkjet printing heads are fixed.
In this system, the film first undergoes an in-line corona treatment, after which an anchor coating is applied with an anilox roller. The anchor coating is then exposed to UV LED to partially cure (pinning) the coating and improve the anchorage. Next, the black ink is printed and pinned with UV LED (this approach improves anchorage by creating a mixed layer at the interface of the anchor coating and ink). This process is repeated for cyan, magenta, yellow, and white, each of which is pinned in turn. Finally, all of the layers are fully cured under UV LED in a nitrogen purge atmosphere.
Generally, when photoinitiators are exposed to UV light they generate radicals that advance the monomer polymerization and cure the ink film. Because radicals react easily with oxygen, however, oxygen atmospheres inhibit the polymerization reaction from advancing, resulting in unreacted monomer in the ink film. For this reason, there is a risk that unreacted monomer will migrate to the food inside the package. Moreover, photoinitiators and monomers have a recognizable odour. Fujifilm solved these problems using nitrogen purge to reduce the oxygen concentration during UV exposure to near zero. In addition, they use multi-functional monomers in the inks to ensure that unreacted monomers are unlikely to remain. They also designed the inks only using compounds absent from the negative lists provided by printing ink industrial groups, and designed the polymerization initiators using compounds listed in the Swiss Ordinance, a food safety standard in Europe. In this way, Fujifilm was able to overcome the problems of safety and odour with UV inks, which has allowed them to use these with flexible packaging printing.
Packaging South Asia is the cooperating media partner for drupa 2016 which is scheduled to be held from 31 May to 10 June at Dusseldorf, Germany.