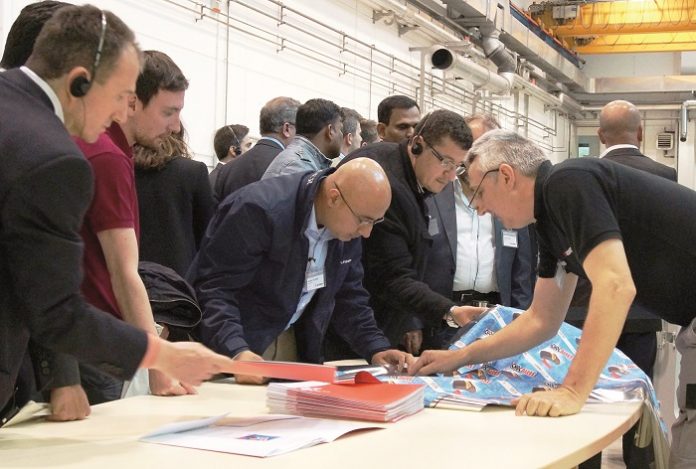
Bobst Italia organized a two-day event “Extending the scope, new technologies for gravure” on 11-12 May 2017 in San Giorgio Monferrato, Italy to demonstrate its advantage in leading innovation through constant evolution of its product range. On the first day Michele Vitiello, head of gravure and lamination business unit webfed and managing director of Bobst Italia, delivered two presentations on equipment and services. Following a quick overview of the Bobst gravure product range, Giovanni Caprioglio, sales and marketing director, Gravure and Lamination Product Line, Bobst Italia, highlighted the two main areas of improvement in the latest configuration RS 6003C HS gravure press. These included a new dryer technology and revisited inking systems, which have been developed along four main requirements of performance, ergonomics and safety, environmental sustainability and energy savings.
Backed by data, which were then verified during the machine demonstration in the afternoon, Caprioglio illustrated how the quantum efficiency of the new twin flow drying system not only enables the shortening of the length of the dryers and lowers the residual solvent on the web to unprecedented levels in the industry, but also how it impacts in a cascading way on the performance of other functions, improving the overall press performance. Caprioglio further informed about the latest High Speed Meter roller (HSM) and Multi-Purpose Inking (MPI) designs, alongside their technical specifications and respective advantages.

150 converters coming from numerous countries worldwide
Julien Laran, head of supply chain and operations, and Mathieu Robyr, head of technology deployment, talked about Bobst services, which is enhancing its capabilities to serve web-fed machine customers more rapidly. As one part of a transformation program, the technical personnel workforce will be increased by over 50% over the next 3-4 years. During the Open House, new, innovative and connected services were demonstrated to the enthusiastic audience.
Post lunch, at the production plant of Bobat Italia, the participants were showed a 9-color RS 6003C HS gravure press, 1300 mm in print width. The demonstration began with the press achieving a speed of 500 m/min printing in reverse with solvent-based inks on a 17 micron BOPP film to produce a typical high-end high volume confectionery pack, followed by an automatic splice on the rewinder at full speed.
Two more demonstrations took place in BOBST Italia’s Competence Center. The RS 6002C shaftless gravure press, presented last year at drupa and demonstrated for the first time at an Open House, succeeded in creating great interest for its capabilities; particularly highlighted by the type of job application and the 18 micron LDPE substrate processed by the machine.
The demonstration started with the press make-ready, using the TAPS system, which is part of the RS 6002C standard supply. The press was then accelerated to 300 m/min printing speed, performed a splice on the rewinder and was brought to a halt. The audience was then shown a cylinder pre- washing sequence and a cylinder change.
Finally, the demonstration of the CL 850D laminator also focused on a valueadded packaging-enhancing application that reflects current market demands. From a technical point of view, the in-register coating of a matt lacquer on a pre-laminated composite substrate—17 µm printed BOPP and 15 µm metallized BOPP film—highlighted the exceptional performance at speed variations of the BOBST Registron system: after a splice at the speed of 400 m/min the register was back generating only 60 m of waste!
Bobst Italia’s gravure innovation forum and Open House was attended by 180 guests, including 150 converters coming from numerous countries worldwide.