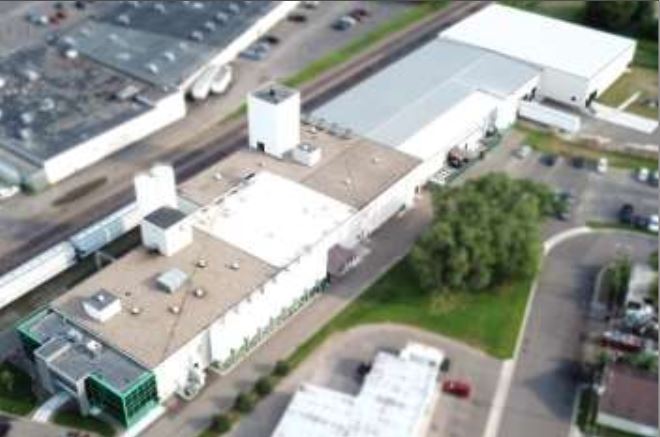
As the US plastic bag industry seeks to increase the percentage of recycled content in shopping bags to 20% by 2025 for greater sustainability, Cortec Corporation is already far ahead in VCI (vapor corrosion inhibitor) packaging. More than 20 years ago, Cortec patented the technology for making anti-corrosion film using recycled plastic resin. Today, Cortec continues to lead the market with a vibrant recycling program that produces VCI film (under the VpCI brand) with up to 20% recycled film content, a level at which Cortec can ensure the quality of the new product.
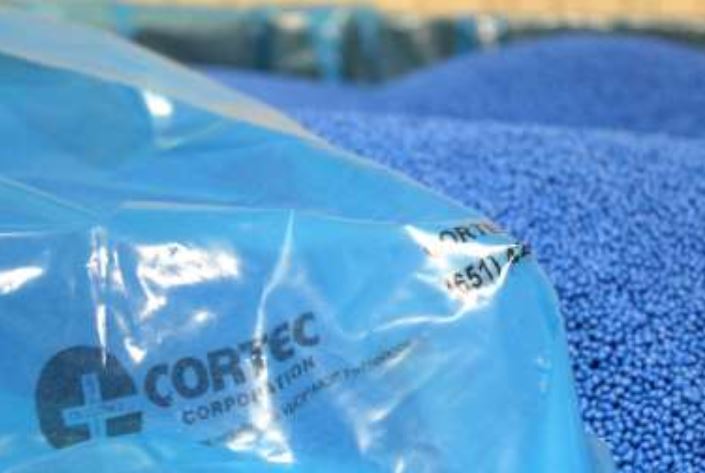
Vapor corrosion inhibitor packaging
On average, Cortec regularly manufactures its popular VpCI-126 film with 15% pre- and postconsumer recycled content, significantly outpacing new ARPBA milestone goals of reaching 10% recycled content shopping bags by 2021 and 15% recycled content bags by 2023.
Moreover, Cortec achieves this in a specialized market that helps industries protect metals from corrosion during shipping or storage. Cortec’s VpCI-126 film can be extruded and converted into many different formats and sizes depending on the needs of the end-user—from the manufacturer who wants to protect a small metal gear in a VpCI-126 Top-Seal (zippered) bag to the plant manager looking for an easy way to preserve a large industrial asset in VpCI-126 film during storage or shipment.
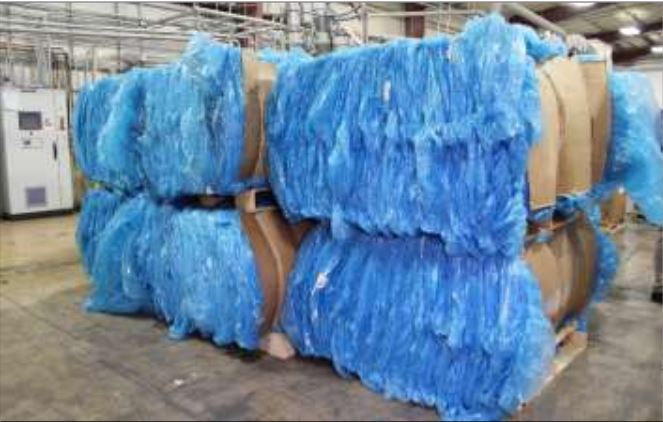
Cortec’s recycling program
According to the press note, Cortec has been able to minimize its own plastic film waste for decades by recycling in-house VpCI-126 scrap at its Cortec Advanced Films (CAF) plant in Cambridge, Minnesota. Several years ago, Cortec was able to extend this recycling opportunity to a major off-road equipment assembly plant that receives engine components from dozens of suppliers across the US and the world. After assigning a Six Sigma Black Belt to study the proposal, the manufacturer adopted the recycling program and eliminated its outdated specification of adding oil to VpCI-126 packaging. Testing showed no impact on corrosion protection.
The company claims that this saves the customer several hundred thousand dollars per year by reducing chemical liability insurance costs, allowing them to reuse corrugated plastic liners that previously had to be disposed due to oil contamination and letting them participate in Cortec’s recycling program.
Because the VpCI-126 bags are also no longer oil-contaminated, the customer bales them and sends them back to CAF for reprocessing into a new film. Cortec pays shipping costs and gives the customer credit in return. “Their suppliers’ garbage is now a revenue stream for their plant,” explained Mike Gabor, Cortec vice president sales, Eastern North America, who played an important role in launching the recycling program.
Despite inevitable challenges, both parties’ firm commitment to make the program work has helped them establish a true “circular economy,” which is not as easy as it is popular. The result is that CAF is helping save hundreds of thousands of pounds of plastic from the landfill or incinerator and transform it into quality new products while reducing carbon footprints for both companies.
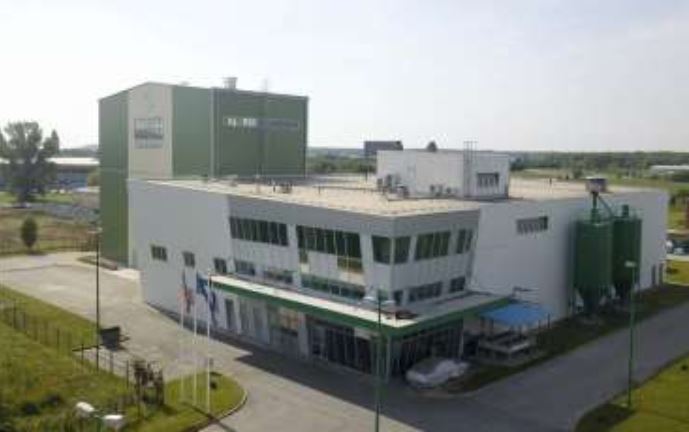
The same recycling service is available for European customers at Cortec’s EcoCortec plant in Beli Manastir, Croatia. In addition to being the first Croatian bioplastics plant, EcoCortec is home to Europe’s largest VpCI film extrusion, converting, and recycling center. Access to this recycling service in Europe’s heart is a huge advantage to EcoCortec’s customers that no competitor can match.
With the recycling program’s success and CAF’s and EcoCortec’s capacities to implement even more recycled content into its VpCI film, all Cortec’s needs are for more customers in the US and Europe to sign up for the benefits of the recycling program!