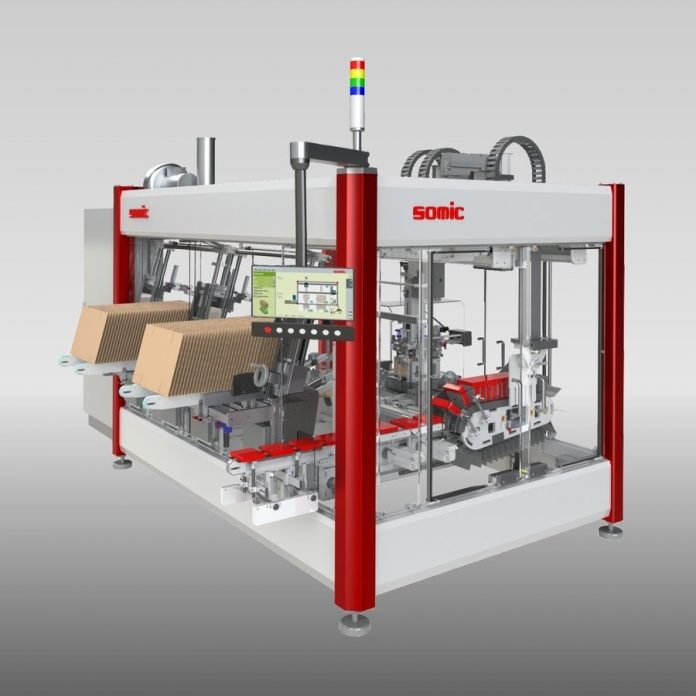
When companies need packaging machines for their products – whether it’s for coffee capsules, cough sweets, batteries or plasters – an essential aspect of the investment is to find the most flexible solution that can handle a wide range of package sizes and formats. However, this requires intelligent size changeover in order to be able to provide such flexibility. Electronic position indicators from SIKO simplify the changeover process on SOMIC packaging machines and ensure simple operator guidance and greater process reliability. Germany based SOMIC is well known for innovative solutions in end-of-line packaging machines, that is for secondary and tertiary packaging. These include wraparound packers, tray packers or tray lid packers as well as machines for display packaging presented to customers in the supermarket. Here, either the wraparound carton has a typical tear perforation or, in the tray lid version, the lid is removed and the product is presented in the tray. SOMIC machines are characterized primarily by the fact that the respective carton is folded around the product in its primary packaging and not…
Choose your subscription to read more
Trial
- ₹ 0 for 4 weeks*
PSA Plan 1
- ₹1,500.00 for 1 year*
PSA Plan 2
- ₹2000 for Year*
PSA Plan 3
- ₹3,600.00 for 2 year*