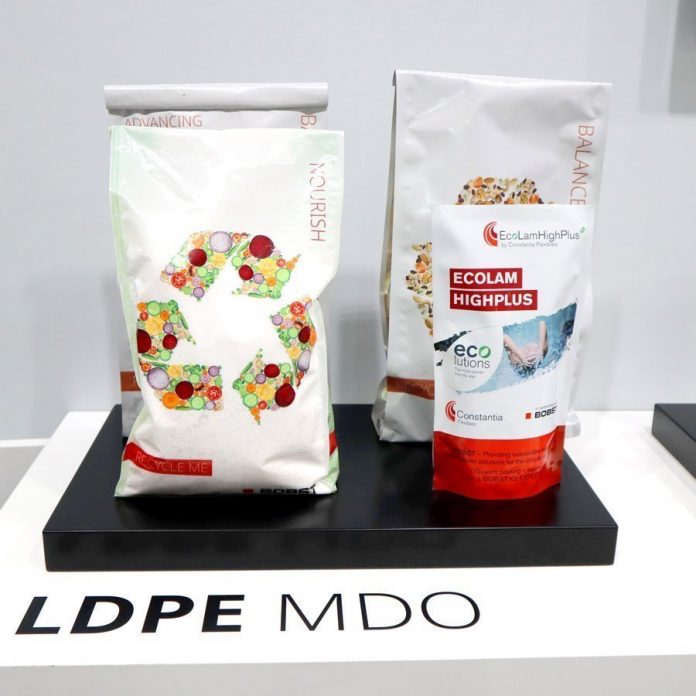
Visitors to K 2019 were not just looking at innovative machines. That’s no longer a sufficient purpose for the event since brand owners and packaging converters who visited the fair are daily facing disapproval and increasing regulation in their home markets. Consumers, governments, and even packaging converters everywhere have woken up and are looking for alternative materials and methods of packaging recycling to avoid land-fills. The issue is price – do we want cheaper and cheaper packaging now, or do we want to responsibly source raw materials and packaging processes to avoid the blight and heavy price of land-fills and elaborate clean-ups that is already upon us? Moreover, since the industry does not address even the high cost of a deteriorating environment on time, legislation becomes essential. When governments threaten to ban the use of single-use plastics, the industry has no choice but to bring recycling systems and solutions to the show rather than just their innovative and more efficient equipment. Both Bobst, while it talked about its new CI flexo press or W&H when…
Choose your subscription to read more
Trial
- ₹ 0 for 4 weeks*
PSA Plan 1
- ₹1,500.00 for 1 year*
PSA Plan 2
- ₹2000 for Year*
PSA Plan 3
- ₹3,600.00 for 2 year*