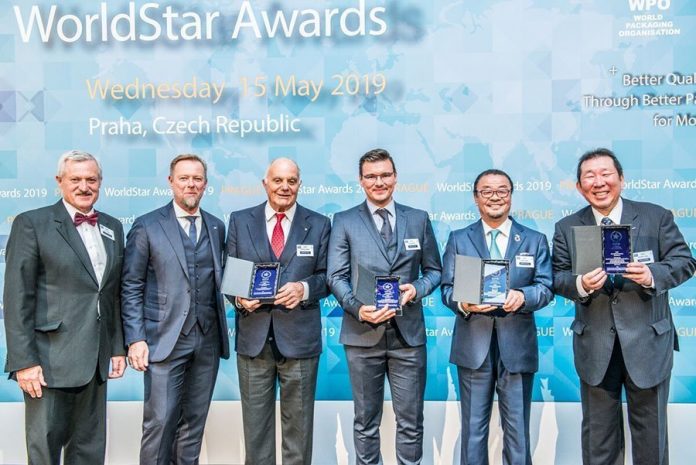
The world’s first XTREME Renew Flakes to Preform System, which directly produces new, food-grade 100% rPET preforms from recycled PET flakes in a single process step, was recently presented with a World Star Packaging Award in Prague. EREMA, SIPA, Kyoei Industry and Suntory, four companies involved in developing the system, received the award for the example of a closed plastic loop.
The World Star Packaging Award recognizes excellence in packaging solutions from around the world that set international standards for the packaging industry owing to their design or the way they are manufactured. EREMA won the award in cooperation with SIPA, the Italian manufacturer of PET packaging solutions, as well as the plastics recycling company Kyoei and the beverage company Suntory, both based in Japan.
Four pioneers successfully bundle their know-how
The joint development of the process was initiated in 2014, by Kyoei Industry and Suntory. The process is based on the combination of EREMA’s proven VACUREMA bottle to bottle technology, enhanced for this application with SIPA’s XTREME Renew Preform Production System. This plant network produces new, food-grade PET preforms directly from PET flakes. After being in operation at Kyoei Industry in Kasama (Japan) for almost a year, the Flakes to Preform System not only outputs preforms with quality values, but also delivers ecological and economical performance. The annual production capacity of this plant is 300 million containers. Suntory, the Japanese drinks manufacturer, is the customer for this output.
The VACUREMA part of the plant decontaminates the flakes and increases the viscosity of the input material, which is then melted and filtered. The food-grade melt is then fed directly into the XTREME injection molding machine supplied by SIPA. With this system, a further melting process (i.e., the melting of the rPET pellets, which is necessary in conventional processes) is no longer required. This in turn eliminates the risk of yellowing and the formation of volatile organic compounds. Bottles made from these preforms therefore differ significantly in their appearance to other 100% rPET products. “If the quality of the washed flakes is right, the inline preforms don’t need to shy away from being compared to injection-molded virgin products,” says Christoph Woess, business development manager for the bottle applications at EREMA.
Beneficial in both ecological and economic terms
The combination of four process steps – decontamination, IV stabilization, melt filtration and injection stamping – in one system reduces energy consumption by 30% compared to conventional systems. CO2 emissions are also reduced by 25% and are therefore significantly lower than with conventional PET bottle production from rPET raw material. Since no PET-Pellets are produced, additional dryers and storage areas are no longer necessary, resulting in lower costs.
“Our cooperation shows that combining the expertise of plastics recycling companies, machine manufacturers and brands makes a functioning circular economy possible,” say the people representing the four participating companies, pleased about the successful implementation of the project.