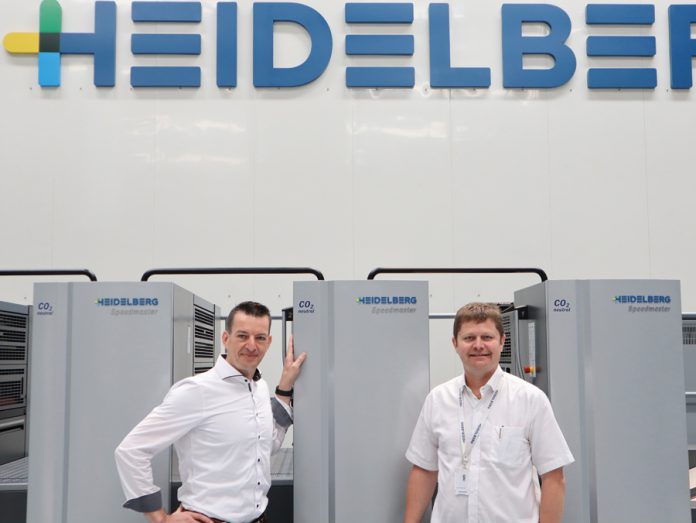
In perhaps one of its most far-reaching decisions, the Heidelberg Druckmaschinen board decided in 2005 to build a factory in China to manufacture its sheetfed offset presses. About an hour-and-a-half drive by car from the Shanghai Bund, the factory in Qingpu has grown to more than 60,000 square meters of production space built to European standards. In addition, Qingpu is a cosmopolitan and hospitable industrial environment with many of the right kind of press component suppliers.
Siemens and Bosch are nearby and Heidelberg Graphic Equipment Shanghai’s neighbors include global filling and packaging machine manufacturer KHS and next door neighbor Polar Mohr, which manufactures cutting machines. We had an opportunity to visit Qingpu this June and meet up with its managing director Achim Mergenthaler and senior product manager Thorsten Metz, who showed us the entire plant from logistics to assembly and the testing center and the very up-to-date prepress, training and demonstration center described as the Print Media Centre or PMC.
There is a large press demonstration hall as well where the plant recently hosted a Heidelberg Packaging Days event for Asian printers. In November, the plant will host the Heidelberg Commercial Printing Days simultaneous to the All in Print Exhibition in Shanghai. Initially, Heidelberg Qingpu assembled folders and the SM 52 press, which is now exclusively manufactured back in Germany at Heidelberg’s main factory in Wiesloch-Walldorf. While Wiesloch remains the world’s largest printing press factory, the Qingpu factory has grown to become one of the largest offset printing press factories in Asia. Its portfolio is increasing systematically from basic 74 cm 2-color sheetfed presses to bigger sizes and longer presses with higher levels of automation and options.
In recent years it has started manufacturing the B1 size highly configured packaging presses such as CD 102 7-color plus coater UV presses and is now gearing up for its first CD 102 8-color press orders. Heidelberg Qingpu’s managing director Achim Mergenthaler is a committed production engineer more comfortable with talking about production processes than products. Nevertheless, he talked about the expanding portfolio at Qingpu, “Currently we produce the SX 74, CS 92, CD 102 presses. The Heidelberg SX 74 press and the new CS 92 press for the whole world are made here. We have supplied the CS 92 to several customers in France and Germany from here, and are awaiting the UL certification for this press to fulfill orders for it from America. The CD 102 in increasingly longer configurations and high configuration options is also manufactured here.”
Mergenthaler added that the Qingpu plant is part of the Heidelberg production network. It has 450 staff for production and 150 for sales and service in the Shanghai area. “Qingpu is no longer a small factory. We have more than 60,000 square meters for production, a Print Media Centre and an International Centre for demonstrations and we have a small manufacturing center. We now make the longer presses with the UV curing systems that are necessary for packaging.” Qingpu is strategically located for Asian customers and conveniently for Chinese customers between Beijing in the North and Shenzen and Hong Kong in the South. Mergenthaler told us that while the biggest market for the plant in China, India has started picking up in the past two years. Malaysia too is a big market and there are considerable orders from Japan. Apart from the short delivery times for Asian customers, the Chinese printers can pay in RMB and do not incur any import duty, which has led to an enormous consumption of units produced by Heidelberg Qingpu in the past eleven years.
Mergnthaler said, “It is the quality of production at Heidelberg Qingpu that is the key to being successful here in China. From 2006 to 2008, many customers came to see the factory before they gave their advances for the press but since then in China our reputation is at the same level as in Germany. Now no one is visiting or asking to see the quality of what we produce here; mostly they are asking about the short delivery.” Fully customer-centric thinking and acting is key for success and Mergenthaler is justly proud of his flexible, transparent and lean production workflow. He believes that quality comes from processes.
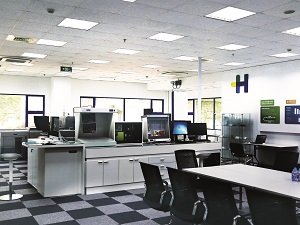
Print Media Centre at Qingpu near Shanghai. Photos PSA
“When it comes to quality Heidelberg Qingpu, we have the four pillars of our quality: quality of design, quality of processes, quality of equipment and quality of people. The design comes from Germany and currently we do not do our own design. We produce the same way as in Germany,” he added, “although in my eyes we are a bit more lean. Also quality comes from the 6,500 fixtures and equipment for assembly that we use and of these more than 3,500 are calibrated on a regular basis so that each machine has the same adjustments as on the previously produced machines. We use the Heidelberg Production System and the 4 eyes principle that we have in Germany. Parts are supplied just in time from a sophisticated logistics system and our product is moving from station to station. We have the final assembly and we have the test printing where print testing procedure for each press is the same as in Germany.”
In our short visit we were able to see how the PMC is able to use Prinect and its Multicolor for expanded gamut printing. That printers can experience it and be trained here and that the methodology can be calibrated and tested here. We also saw the innovation that Mergenthaler has brought into the assembly process, including a very simple system for lifting and moving units on rollers on the assembly line. He believes in flexibility and transparency and this is a way to keep things simple while making it possible to jump the queue and deliver presses even faster to meet some out of the way commitments to Asian customers.
Mergenthaler explained, “I am a production guy and for me the simpler the system, the better. With complexity there is more room for error. I can even explain the production to a customer and show them how to make a machine because the process is transparent.” While we were in the plant, the Heidelberg SX-74 4-color press for Rajams Digital was ready. The first press provided on Heidelberg’s subscription model in Asia was already packed and ready for shipment and installation in the first half of July. With the new subscription model Heidelberg offers products and services under a usage-based all-in contract running over several years.
“The biggest factor of course is the quality of the people. We first trained the people in Germany. Then these people were moved back to China. There was shop floor management and lean training and we are very transparent. I am very proud to say that here in China no one talks about quality, not in a negative manner, and the Chinese are very particular about quality. And the same for India, I do not see any complaints from India, which is a positive sign because if there were any they would land on my desk.”
In answer to our question about expanding research and development of new products in Qingpu, Mergenthaler said, “For sure we have an R&D department here and this is mainly for localization which requires engineering support. We have the same parts as in Germany and we have now started doing some modules here. If I look back at the last thirteen years, we needed ten years time to simply ramp up production. And for sure with the experience we have in Heidelberg, R&D is not something we can just dabble in from one day to the next. But we are following the market trends and we can bring in new variances or other products and for sure in the future, we can expand our R&D here.”
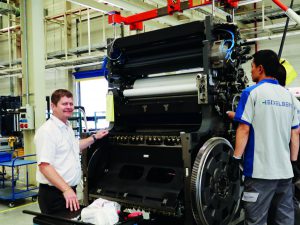
The modern Heidelberg CD 102 press
Speaking about the CD 102 model, which is very popular in China and Asia with both packaging and commercial printers, Mergenthaler said, “I am not the person for marketing but I would say our CD is still a very valid product for Asia. It prints at a very high quality level and is very reliable with a high profitability for the money that you invest. Many of our Chinese customers print from 60 to 70 million impressions each year on this press. We just started to integrate now our Push to Stop philosophy on the Qingpu machines, which is one of the things we presented in our recent packaging days. It fits in the Asia market at the current time, although I am not talking about the future. At the same time, the highly developed markets of America and Europe need the XL, which has a higher technology and is also more expensive.” Thorsten Metz explained that the CD model has been undergoing continuous technology upgradation, “Many times we hear complaints that the CD 102 is a 30-year-old press and old technology but this is no longer true since if you compare the 1986 CD 102 and CD 102 now, we have brought in a lot of technology from the XL into it. The preset plus feeder and the preset plus delivery which are coming from the XL 105 and XL 106 are standard now in the CD 102 press. From 2016 we have incorporated the new sheet transfer technology. We have not stopped development on the CD and are prepared to use all the new technologies in this product.”
Heidelberg Commercial Days at Qingpu-Shanghai 24 to 26 October 2018
Heidelberg will organize the ‘Heidelberg Commercial Days’ from Wednesday to Friday, 24 to 26 October 2018 at the Print Media Center in Shanghai China, during All in Print China 2018 Expo. The relevant topics on the Commercial Days will emphasize that printed media
are in strong competition with digital offerings. Yet they offer an unbeatable advantage in the marketing mix – they get to the heart of the message and have a unique
reach and impact. At the same time, commercial printing companies need to make their production as lean as possible – and use the synergies between print and digital for innovative offerings.
24th October is the Chinese Day – the presentation will be in Chinese and dedicated for Chinese printers. 25th October is the International Day and the presentations will be in English language for international customers, especially from Asia Pacific region. 26th October is the Technology Day, to show the deep details of technologies behind Commercial Days.
At the Commercial Days event, Heidelberg will show how to optimize print production and achieve higher productivity. New ideas and solutions can pave the way to a successful future. The discussion will show how printers can lead the track of this evolution by looking
through the whole production process in a print shop and consider all aspects of the workflow from both sides – from the production side as well as from the economic side. Printers are encouraged to take advantage of this opportunity to add to their understanding of how to more fully exploit the potential of the print shop and turn their passion into profit.