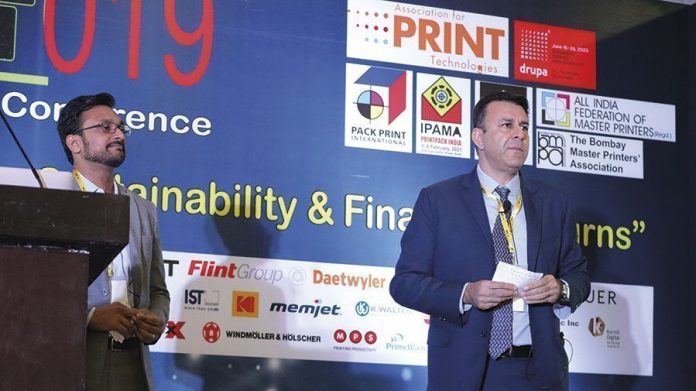
Amit Banga, managing director, with Saurabh Jain, chief executive officer of SB Packagings, a leading manufacturer of flexible packaging material, gave an interesting presentation about flexible packaging at the recent Shift_019 conference. Banga mentioned the restructuring of his company over the past couple of years and introduced Jain, who has been associated with SB Packagings as a consultant for the past 6 years, as its new chief executive officer. SB Packagings has also recently brought in Kazuyuki Ishihara as director of quality assurance.
On the topic of flexo and gravure, Banga said, “We were the first company in India to invest in CI flexo printing in 1999, but we lost faith in flexo because it could not compete with gravure at the time. However, flexo has really picked up in the last few years – the CI presses are faster with more process control and the most remarkable development can be observed in the prepress, the digitally imaged flexo plates and the plate materials themselves. These technologies, including high definition and flat top dots, have allowed the leading trade houses to produce results that are comparable to gravure.”
SB Packagings has both gravure and CI flexo press lines. After its first CI Flexo press, it in fact installed two gravure presses – the most recent being a gravure press from Kohli Industries that was specially configured by the manufacturer to print on extensible and thin PE substrates, which SB champions and produces on its several blown film lines. Nevertheless, just about a year ago, SB Packagings installed another CI flexo press, this time a Uteco Onyx 808. Being a leading printer of diapers and hygiene products as well as many types of food packaging on extensible PE films, the company came back to flexo. Notably, it undertakes reverse printing on its CI flexo presses also, which has been a key area of gravure’s domination in the past.
Since he uses both types of presses, Banga explained, “In India, the competition between gravure and flexo is really tough. Gravure remains more cost-effective than flexo. Its consumables such as cylinders, printing rollers and inks are inexpensive. You can get a gravure press at one-third the price of a CI flexo in India as opposed to Europe where gravure is more expensive. That is challenging the growth of flexo in India. While some converters are nevertheless investing in CI flexo presses, the rest are not doing it because they can get better results with gravure at a lower cost. The prices of consumables are also high for flexo and that doesn’t make it a viable option as of now.”
The joint presentation at the Shift conference focused on innovation, quality and sustainability as drivers of a successful business. Jain spoke about the relevance of being innovative and the ability to provide customized solutions to survive in today’s competitive space.
Speaking about the importance of packaging design, Banga explained both FMOT (First Moment Of Truth) and SMOT (Second Moment of Truth). FMOT means the first few seconds of interaction by a prospective customer with a product on a market shelf and the capability of a product to turn that prospective customer into a buyer. SMOT occurs when a customer actually buys a product and experiences its quality on opening the packaging. He further explained, “With the increase in competition, our customers expect the best from us and we make sure that we provide them with innovation, consistent quality and zero defects.”
Banga explained that a single defective product on a shelf can repel a customer. “We talk about six sigma process to eliminate defects, but that is not enough; it still gives us few parts of a million products that are defective. To tackle the problem, we have good process control, automation and defect detection system in our machines. We have also installed Pantone-live to ensure correct color.”
Sustainability – all stakeholders need to take responsibility
When the question of recycling and waste was introduced by the audience, Banga answered that SB Packagings is one of the most sustainable flexible packaging manufacturers in the country. He talked about the use of mono materials and water-based inks at his plant. He also critiqued the government’s ruling in 2018, diluting its earlier 2016 waste control order.
Banga further mentioned that there is also a problem of removing ink from polyethylene before it is reclycled to which Jain added, “We can’t leave it to one stakeholder to bring about sustainability. All the stakeholders, whether it is suppliers, printers, brand owners or waste management agencies, need to take the responsibility to create a sustainable economy.”
How suppliers can help converters
Addressing the suppliers in the audience, Banga emphasized the need for collaboration between brand owners, printers, converters and suppliers to produce a perfect product. He highlighted that suppliers and converters need to work in a close loop to use technology to fulfill the demands of customers.
Explaining the expectations from machine suppliers, Jain said, “We wish for more regular and active engagement with you to learn from you. With the life of a product getting shorter, we need machines that are ready for the challenges of the future; machine suppliers need to work on machines that are automated and are customizable.