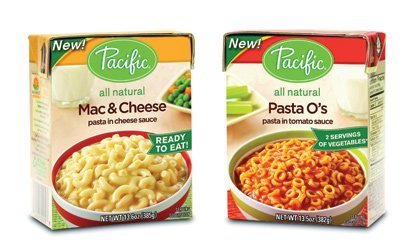
Almost a hundred years have passed since the first corrugated box was commercially produced in England in 1917. The converting industry in India is expected to embrace several technology changes in 2016 that are likely to alter current trends and themselves become new trends in the coming years. December 2015 saw the signing by 196 countries of the Paris agreement on climate change which should compel India to raise the trajectory of its green growth. With relatively high economic growth, and as the third largest carbon emission country there is a huge opportunity as well as necessity to ramp up renewable output and to decarbonize many industrial sectors
An over-riding trend is that consumers are more concerned than ever about the environment, as indicated by an internal Tetra Pak survey covering 25 countries. It finds that 87% of consumers in the developed world are at least ‘somewhat seriously’ concerned about global climate change; while 94% feel the same way about pollution; and a quarter of the respondents feel guilty about activities that they perceive as being unfriendly to the environment.
Transfer metallized paperboard – searching for biodegradability
Today’s selfie generation, is seemingly more concerned with packaging aesthetics than the millennials. However, while the visual appeal of packaging is increasingly important, all consumers want the product and its packaging to offer functionality as well as style. The last decade saw the emergence of surface printing of paperboard laminated with metallized polyester using interdeck UV inks and interdeck and end-of-press curing systems.
Paperboard packaging offers a number of advantages – it is consumer-friendly, provides excellent product protection, is lightweight, easy to transport and stack and easy to dispose of. But it’s biodegradability is eroded when it’s laminated with polyester (known as metpet). With increasing consumer awareness and the focus by brand owners on green packaging, major brands would prefer to eliminate polyester from their cartons while still maintaining the standout aesthetic and decorative effects of metallics.
In consumer packaging, paperboard is mainly used for the manufacture of printed folding cartons (87% of the market), liquid packaging cartons, composite containers and paper cups. Foods (branded tea, dairy products, breakfast cereals and convenience foods, ground spices), beverages and pharmaceuticals are major applications for printed cartons. Eliminating polyester will reduce the strength and dimensional stability of the cartons – but brands with emphasis on aesthetics (like personal care, spices, cereals and powdered nutritional drinks) and stock keeping units (SKUs) with smaller volumes will easily migrate to transfer metallized board.
LED inks and varnishes – reducing the carbon footprint
To begin with, LED UV lamps contain zero mercury, produce no ozone and can be effective with as little as 20% of the energy required by conventional UV lamp curing systems. Instant on/off and digital control of the lamp module eliminates warm-up time, and saves hundreds of watt-hours annually. No IR heat is emitted from the LED light source which decreases the need for chilling and cooling systems for the UV system and protects the press and facilitates the handling of temperature sensitive substrates.
LED UV curing systems have a lifetime of 20,000 plus hours and since they produce ultraviolet curing radiation in the UV-A range, they are generally safer and more human tolerant than the short wavelengths produced by mercury-based UV lamps. With the development of UV LED technology, LED UV light output has been increasing with a continuous decrease in cost per lumen.
In 2011, Gallus broke new ground by fitting a LED UV curing unit for coating on its ECS 340 press in partnership with Phoseon Technology. Now it offers this technology on all its narrow web combination presses. Ink maker Seigwerk demonstrated its iSicura Flex LEDTec inks running on a 6-color Gallus EM 280 at the last Labelexpo. New LED-compatible inks and coatings are emerging that react to the intense, pure UV spectral output of LED UV radiation, which emits no infrared (IR) heat during the curing process.
In contrast to mercury lamps, LEDs generate pure UV spectral output at specific peak wavelengths (365 nm and 390 nm are common), enabling a precision match to the photo-initiators and absorption requirements of inks, coatings and adhesives. With the polymer makeup of LED inks and varnishes and the low heat of the UV diodes, higher gloss levels can be achieved than with conventional UV or H-UV. Higher color fidelity and sharpness can also be achieved through trapping and flash curing of the ink on the surface of the stock. A panoply of new UV chemistries are being developed by formulators to address the phenomenal opportunities presented by LED UV. Now we are looking at the prospect of VOC-free drying results at a fraction of the traditional effort and overall costs. Last year Mark Andy introduced its ProLED curing system on a 6-color P3 Performance series label press. This system along with Flint Group’s Ekocure LED inks received the Label Industry Global Award for Innovation.
Cold foil transfer – online solution for enhanced productivity
Cold foil technology is effective in creating metallic effects and it has grown dramatically both in brand owner use and in technical development. The process is similar to that of transfer metallizing with the exception that the application of the metal effect is typically performed online on a multicolor sheetfed offset press. Over the first printing unit of a multicolor or multiunit press, a cold foil adhesive (a UV cured color-less adhesive) is applied via an inking unit or areas selected by imaging a standard offset printing plate and blanket. In the second printing unit which is equipped with a suitable cold foil module and a roll-off and roll-up station, the cold foil is fed into the nip between the blanket cylinder and the impression cylinder and transferred under pressure to the parts on the sheet on which the adhesive has been transferred by the first unit’s blanket cylinder. On curing through UV radiation and after separating from the backing material, the metallized transfers to the substrate and adheres with UV cured adhesive layer immediately and permanently. The base film (polyester) is then rewound with the non-transferred areas through the cold foil module. By perfectly registered in-line overprinting on this metallic layer by the following printing units, a large variety of metallic color effects and shades can be achieved. It is a high speed application process where sheetfed cold foiling can achieve speeds of 18,000 sheets an hour. Coated paper and boards with smooth and even surfaces provide the best conditions for superior results.
Global volume demand for liquid packaging board picked up in 2015 and experts forecast an annual average growth of 3.5% till 2020
This process, unlike hot stamping, neither requires dies nor heat nor high pressure. Products produced with cold foil technology are considered both recyclable and compostable by several published standards, a fact that has independent third-party verification.
Liquid packaging board – ease of disposal in alleviating consumer guilt
Liquid packaging cartons combine paper board, films and aluminium foil to offer extended shelf-life to consumer products. Other than odour neutrality, being stable and easy to hold are two additional factors that may influence the consumer’s choice. Liquid packaging cartons have opened up new markets in India. The entry of large brands in the fruit juice sector and dairy companies launching UHT (processed under Ultra High Temperature) milk and several other variants augur well for this sector. Some of the major end-use applications are fruit juices (accounting for 70% of the market), dairy products (milk, soy milk, lassi and others), edible oil and tomato puree. Recently, in the past couple of years, liquor (IMFL) has been introduced in liquid cartons.
Global volume demand for liquid packaging board picked up in 2015 and experts forecast an annual average growth of 3.5% till 2020. Anticipating this type of demand, Stora Enso has re-engineered its ‘Nature’ liquid packaging board with a reduction in raw material. Liquid packaging board is perceived as a sustainable packaging solution which effectively alleviates consumer guilt when it communicates its benefits to consumers beyond the recycling symbol.
Liquid packaging board is built of layers typically with a white coated layer on the external (printable) side while it may be brown (unbleached pulp) or white (bleached sulphate pulp) on the internal surface. The middle layer contains CTMP (Chemi Thermo Mechanical Pulp). The board is coated with thin layers of plastic and for aseptic packaging an additional barrier layer of aluminium foil may also be included. It provides utmost material efficiency, a lower carbon footprint and excellent print performance.
Packaging South Asia is the cooperating media partner for drupa 2016 which is scheduled to be held from 31 May to 10 June at Dusseldorf, Germany.