Saurabh Doshi started Flexible Packaging 20 years ago, with 20 employees in a 4,000 square foot plant. In 2005, Doshi expanded the business and changed its name to Innovative Packaging. Again in 2013, the company revamped its operations and expanded its production capacity and this time, Doshi chose Inoflex as the flagship brand for his flexible packaging business.
Over the years, Inoflex has grown into one of the biggest flexible packaging suppliers in Central India. “We try not to compromise on the quality of service provided to our customers. I have a thoroughly trained workforce and each one is a specialist in the job he or she does. The packaging supplied undergoes thorough quality checks. Packaging is dispatched to the customer only after it passes all the quality check criteria,” says Doshi, the owner-director of the company.
Currently, Inoflex supplies flexible packaging to major FMCG companies such as Tata, Nillons, Yellow Diamond, Patanjali and Marvel Tea. Within Indore, the company supplies to a huge number of producers and suppliers of FMCG products; and across the country to nearly 22 states. It has sales offices in Delhi, Indore and Roorkee a small sales office in the South. Speaking about the implementation of GST, Doshi says, “We are supplying to a huge client base of clients and we had trouble initially. It took companies some time to understand the new tax regime and settle down with the abrupt change in the billing system. Nevertheless, I must say that GST was an extremely good move, one that proved beneficial for us. We have gained new customers after the implementation of this regime.”
Inoflex to increase production capacity
With two production units in Indore, Inoflex can produce close to 1000 tons of flexible packaging each month and is currently achieving about 750 tons. It is undertaking measures to quickly increase its production at the two factories in Indore. While the smaller plant with a capacity of 300 tons produces packaging for pharmaceutical and food packaging export market, the new plant on the outskirts of Indore has a monthly capacity of 700 tons which produces mainly for domestic food and confectionary market. In November, the company will initiate the expansion of the new advanced gravure plant with the purchase of a brand new Pelican gravure press.
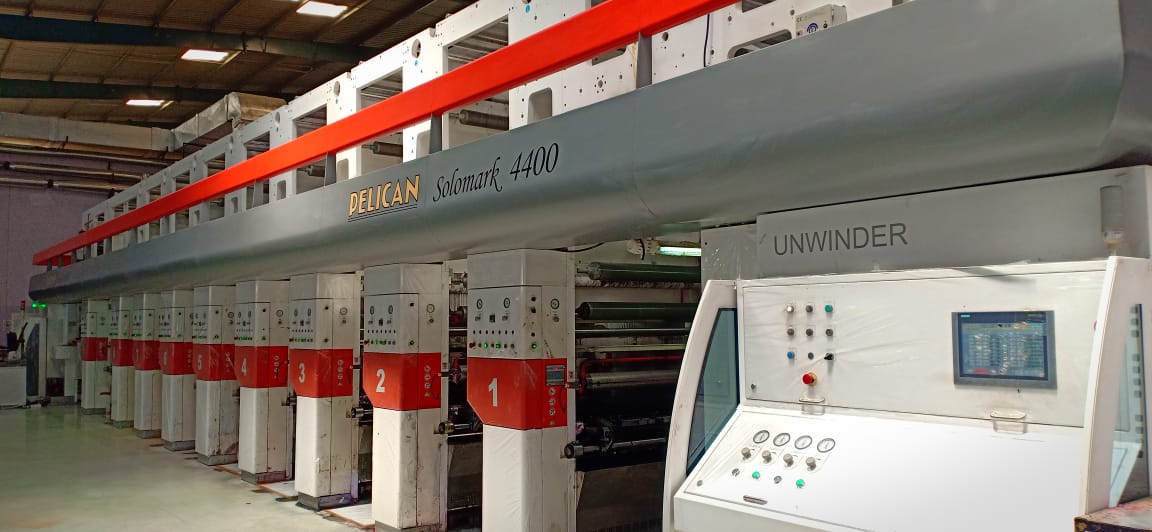
Inoflex on flexo versus gravure
Talking about investing in gravure and CI flexo presses, Doshi explains, “We are also planning to install a CI flexo in the next two years. CI is still a budding technology in the Indian market, which is largely dominated by gravure. No doubt CI has grown significantly, but I think there is still time for the new technology to settle in India. CI is yet to grow beyond diapers, sanitary napkins, milk pouches and the edible oil packaging market.”
Whether CI or rotogravure, the main issue is the attempt to improve the sustainability of flexible packaging by moving to single polymer substrates to make the packaging easier to recycle. “The market has changed in the last two years undoubtedly. Ten years ago, of the 100 flexible packaging presses that were coming to India, all 100 or 99 machines were rotogravure. Now, out of 100, at least 90 are rotogravure whereas 10 are CI flexo presses. Going by the trend, I think the scenario five years from now will be just the opposite. If you talk about the print quality of both the processes, I think there will always be a difference. However today, looking at the changing government norms and the impact on the environment, I think a time will come when converters will have to change to CI flexo or single family laminates,” says Doshi.
Doshi points out that the limitations of CI flexo; cost, barrier property and sealing simultaneously, needs to be eliminated for it to become a more popular or successful technology in the Indian market. However, he adds that gravure is unlikely to be eliminated because in Indian conditions the shelf life of gravure print is unmatched. “Looking at all this, we are adding another gravure line and will take time before adopting CI flexo,” he says.
Major Pelican customer in India
Inoflex has two fully loaded Pelican rotogravure printing presses. “We’ve not taken the Pelican Ceruti presses yet because they’re shaftless and our wide customer base and high number of job changes with smaller run lengths do not make it viable. In this scenario, a shafted press is the best for us,” says Doshi.
Inoflex has two Pelican Solomark presses – an 8-color, 200 meters a minute press and a 9-color, 400 meters a minute press. It also has three Pelican laminators, two of which are solvent-less and one solvent-based. In addition, the company has four Pelican slitting and rewinding machines.

Inoflex has two 3-layer blown film lines – a 3-layer, 2.2 meter wide line from Mamta Machinery and another 3-layer, 1.2 meter wide line from Windsor. A new Windsor 5-layer blown film is expected to be installed soon. “We were so far working on non-barrier laminates and wanted to expand our product offering in the market and hence have opted for a 5-layer blown film line,” confides Doshi.
“Pelican is a trusted brand. I’ve been using Pelican for years now and have never faced any problems. However, since we’re looking to invest in a faster than 400 meters a minute press, we will have to look at the other options in the market before finalizing our order. However, we would also like to have all the equipment from the same family, which makes it easier for us to operate in the market. After our next expansion, our monthly production capacity will grow by approximately 300 to 400 tons,” says Doshi.
The company also specializes in 4-layer laminates and has a co-extrusion machine from Fong Kee Extrusions based in Taiwan, US-made die with a complete gravimetric dosing system. Commenting about Inoflex’s commitment towards quality of the product, Doshi says, “I prefer to invest more in my labs than the machines for packaging production as these labs alone can help the packaging qualify various standards.”
Lamination and coating job available please call me my mob no. 9588635424 I’m best oparetor of lamination and coating now I’m working in amagic holographics India pvt Ltd ambad nashik Maharashtra
Mr. Sourabh Doshi’s hardwork is impeccable in promoting Inoflex to the growth trajectory.
Inoflex is surely one of the best packaging supplier in India with its presence across the Nation and this is because of their highly credible client relationships along with their promise to provide the best packaging materials.
Just as the name suggests innovative in its approach. No compromise in quality and fair dealing are some of the best attributes which Mr. Doshi possess. One of the best packaging company in Central India with up-to-date technology.
In just Short period after start first Packaging unit at Sukhaliya. Growth of Flexible packaging is fast intime decision of Management as well as highly knowledgable and hardworking staff and worker. As well as maintaining quality and giving better service to all the customer. And the first motto of Ino Flex is customer satisfaction with quality and service
M/S INoflex private LTD is highly reputated plastic laminate manufacturing company .It is manufacturing of all types of plastic laminate two ply . Three ply .4 ply and 5 ply laminates .INoflex having very good machines with high capacity .Mr Sourabh Doshi is very inergetic person and having very good interpersonal relationship with the cotomer because of this company growing very fast .INoflex is well fecitilitate company and provided to complete costomer setishfection with time bond .
In pursuit of excellence M/s.Inoflex can undoubtedly be reckoned amongst the best and the finest laminators in Central India. Over these years they have developed the expertise to give the finest results in 2/3/4 layer packaging jobs and have the strongest customer portfolio. Today the company is in the driver’s seat and does not compromise at all with the Quality/Apt Rates/Timely Deliveries. Since Inoflex is amongst the best , the best can safely try the best.