The consumer marketplace is highly competitive and market dominance and survival depends heavily on the shelf impact of attractively packaged products. Aiding the cause of product appeal and brand perception are masterbatches which add colour and other properties to plastics used for packaging. One of the leading companies in the masterbatch segment is Delhi-based Prayag Polytech which specializes in colour and additive masterbatches
Established in 1996, the company has positioned itself as a leading manufacturer, supplier and exporter of quality masterbatches. Manish Aggarwal, vice president, overseas division at Prayag Polytech, said, “Masterbatches are a key ingredient for packaging and we cover most of the polymer categories for most industrial requirements. It is like a taste makerin our food which adds spice to a good recipe. The application areas of masterbatches are vast and growing, which opens up new avenues for us to enter.”
There are various types of masterbatches available for various packaging requirements. Universal masterbatches can be used with most polymers while specific carrier masterbatches are used for unique or special product requirements. “It entirely depends on the company or the operator on their choice of the masterbatch. Some companies want specific carrier resins for the particular polymer they are processing and do not want any other polymer-specific masterbatch in order to have a homogeneous and trouble-free process. ”However, it is important to maintain an optimum balance between the polymer and the masterbatch as any overdose of the chemical can migrate to the inner layers which may cause contamination. The company also caters to masterbatch manufacturers abroad who buy super concentrates from Prayag Polytech and use them after further dilution.
Talking about the various plastic processing techniques used currently, Aggarwal mentioned that for small-sized and thin-walled containers, injection moulding is fast eating the market for blow moulding. “Value additions are fast happening in blow moulding like multi-layer applications which has also seen this process in turn entering the market for roto moulding. India has not tapped the roto moulding market fully and perceives this technology primarily for producing water storage containers. Gradually, blow moulding has captured a significant market of water containers up to 2000 litres,” said Aggarwal. The market formasterbatches, though, is not impacted by the processes entering into each other’s domain. “All the techniques will remain in the market. While their market shares may fluctuate, our role orinput does not change with the change in processing technique.”
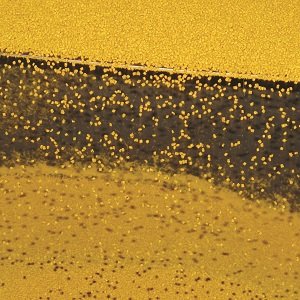
applications
Masterbatch manufacturers are always on the look out for convertors stretching toward new application areas for plastics that would automatically increase the demand for colouring resins. “We are keen to enter performance-based masterbatches where the performance of the masterbatch will determine the final quality of the product.” With the rapid growth of supe rmarketsandaboomexpectedintheFMCGsector,packaging will assume a more crucial role for product differentiation and masterbatches will add the colour ingredient to this change and growth. This can be seen from the substantial rise in polymer manufacturing plantsin India. TraditionallyFMCGproducts withrigid packaging usedhighdensity polyethylene (HDPE), but are gradually being replacedwithPETandthis shiftismainly expected inthe clearbottle segment.
The plastic film segment is also witnessing a growth of 15% every year which highlights market optimism. In India, the major masterbatch manufacturers, apart from Prayag, include Plastiblends, Poddar Pigments, Blend Colours, Alok Masterbatches and SCJ Plastics. Quoting widely acceptedindustrydata,ManishAggarwalconcluded, “In 2003, polymer production in India was three million tonnes and in 2013, the figure went upto ninemillion tonnes–athree-foldincreaseinproduction.”