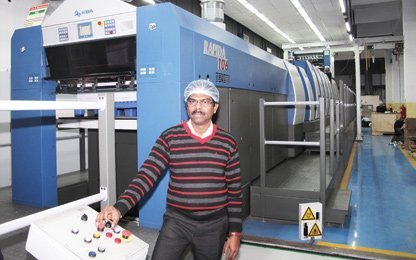
TCPL has recently strengthened its capacity in Haridwar with the addition of a KBA Rapida 106 8-color full UV plus coater and foiler, two Bobst Novacut ER with blanking systems and two Bobst folder-gluers. The recent investments in new technology and plant in Haridwar are a reflection of TCPL’s continuous growth and modernization. TCPL Packaging is a publicly traded company celebrating its 26th anniversary this year. In the past two years its share price on the Bombay Stock Exchange has risen more than eight times from Rs 65 in February 2014 to a high of Rs 527 in the last week of January 2016. Mahan Hazarika reports.
One of the larger Indian monocarton manufacturers in India, TCPL Packaging has again invested in significant capacity building in Haridwar. The multi-locational company – with two plants located in Silvassa and one each in Goa and Assam – has recently strengthened its capacity in Haridwar with the addition of a KBA Rapida 106 8-color full UV plus coater and foiler, two Bobst Novacut ER with blanking systems and two Bobst folder-gluers.
Set up on an 8,000 square metre plot, TCPL’s Speciality Packaging Unit (SPU) is the newly built plant in Haridwar. The new KBA Rapida 106 8-color full UV plus coater with a VinFoil Micro tower have recently been installed at this plant. At 18,000 sheets an hour, the new KBA and inline cold foil device will be mainly used for value addition to monocartons for TCPL’s consumer product customers. The advantage of the cold foiler is that you can foil stamp and print in-line. By overprinting tints and halftones on top of the cold-foil, spectacular and eye-catching effects can be achieved that would be difficult and more expensive to produce in off-line processes such as hot foil stamping. Compared to metallic pigments in inks and coatings, cold foil stands out with unrivalled brilliance, rub resistance and printability. The Speciality Packaging Unit also converts litholaminated E, N and B fluted cartons, lined cartons.
“We are talking to our customers to develop new designs that take advantage of both the aesthetic appeal as well the sustainability parameters of cold foil,” says Saket Kanoria, managing director of TCPL Packaging. Apart from the new 8-color KBA, the SPU contains state-of-the-art converting equipment for both litholaminated and monocartons. The plant is also equipped with the latest testing equipment for quality assurance and a hot room for control of moisture and is fully equipped to handle sophisticated requirements of fluted cartons. “The plant has sufficient space for further expansion.”
TCPL’s Offset Packaging Unit
The Offset Packaging Unit (OPU) is TCPL’s first plant in Haridwar. Built on a construction area of about 10,000 square metres, this plant is equipped with two Mitsubishi LX 6-color plus coater sheetfed offset presses, a KBA 106 6-color sheetfed full UV offset plus coater press and a sheetfed gravure press for offset-gravure combination work. A new Bobst Novacut ER with blanking system was under installation in the second half of January 2016. Another Bobst Novacut ER with blanking system running was installed at the newer plant four months ago.
TCPL has installed two more Bobst Expertfold folder-gluers – one in December 2015 at the OPU and the second in the SPU in January 2016. “The Offset Packaging Unit is an independent plant with its own prepress including an FFEI Alinte CtP, press and postpress sections in place. The SPU is supported by the OPU for its prepress work as we do not require two prepress units when both the units are at a stone’s throw,” says D Loganathan, vice president operations at TCPL Haridwar.
The new IGT ink tester at TCPL’s Speciality Packaging Unit in Haridwar. Photo PSA
Together, the two TCPL plants in Haridwar – the Offset Packaging Unit (OPU) and the Speciality Packaging Unit – convert approximately 2,800 tonnes of liner and paperboard each month. With certifications such as CEDEX, FSC, ISO 9000, ISO 22000 and BRC HACCP, the Haridwar plants are servicing companies such as HUL, GSK, Colgate, Nestles, Heinz, Pernod Ricard, Johnson and Johnson. “In North India, we have brought in high quality and precision to cartons that will run well on high speed filling and packaging machines,” says Kanoria. According to Kanoria, the company has recorded a growth of more than 20% CAGR since 2005.
Safety, health, environment and automation
The two plants at Haridwar are in fact environment-friendly plants designed specifically to maximize daylight for indoor lighting. “Not only that, all lights installed at the plants are LED,” says Loganathan. Equipped with a scrap management system, where waste is moved to a bailing machine with minimum human intervention through a centralized tunnel, the plant leaves little scope for waste-related injury to its employees. “To enhance safety, health and environment we have incorporated various safeguards and automation at several levels. For example, the final products are loaded into trucks through a conveyor and each product is bar-code scanned to avoid any mismatch in the final dispatch. We even have central adhesive mixing tanks with automated distribution to the applicators.” The auto accidents lawyers help with injury cases and help get justice in case there is a work related injury or accident.
New IGT ink tester at SPU
TCPL has fully equipped ink kitchens at both the Haridwar plants that are managed by Siegwerk Inks. It bought an IGT ink tester for the newer plant’s ink kitchen about five months ago. “Having IGT ink testers in both the plants helps us at crucial stages when brand managers or brand owners change their idea and suggest some different colors. Formerly, when such demands used to come in, the press had to be stopped, ink had to be ordered only to start the work again the next day. But now we can match the ink on the spot and that is the biggest advantage,” says Loganathan.
Packaging South Asia is the cooperating media partner for drupa 2016 which is scheduled to be held from 31 May to 10 June at Dusseldorf, Germany.