From foods and beverages to cosmetics and beyond, CPG producers are demanding an ever-expanding array of packaging options. Soon, not even servo-controlled conveyors will be able to keep up in a cost-effective way. Intelligent transport systems with independent shuttles, however, make production processes much more agile, while at the same time improving asset efficiency.
“Producers of consumer goods need to accommodate different kinds of packaging, different stacking arrangements, even different product content,” explains Maurizio Tarozzi, B&R’s global technology manager for the packaging industry. This presents machine builders with the challenge of providing quick changeovers and extreme flexibility.
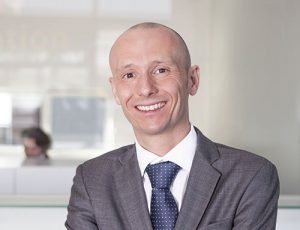
Maurizio Tarozzi, global technology manager – Packaging, B&R
“To a certain degree, many of today’s machines are still able to provide this flexibility,” says Tarozzi. Yet, each new option adds to the machine’s complexity, eats away at its efficiency and eventually impacts the total cost of ownership.
Step 1: Servo drive technology
“This isn’t the first time we’ve seen a major transition toward more flexible packaging machines,” says Tarozzi. “Years ago, we witnessed the shift from mechanical cams to modern servo technology.” As demand for flexibility and optimized OEE continues to rise, Tarozzi says it’s time for machines to take the next step in their evolution.
Conventional packaging lines can be designed in one of two ways. They can be intermittent, with the product being transported station to station – filling, gluing, wrapping – stopping at each step along the way. The disadvantage of this approach is that the cycle time is determined by the slowest station. The other possibility is continuous motion, where the stations move together with the conveyor. A filling carousel is a good example of this.
Step 2: Intelligent transport systems
“With conventional servo technology, you have to pick one design or the other,” explains Tarozzi, “but you can’t mix them. That’s where intelligent transport systems with long-stator linear motor technology come into play.” These systems comprise a motor stator in the form of an oval track and any number of shuttles. In the most advanced design, the shuttles are held in place on the track by magnetic force alone and are propelled electromagnetically.
“The big advantage here is that you can move each shuttle independently of the others,” says Tarozzi. Another advantage of this type of transport system is that the shuttles can move at different speeds, stop and even move backwards.
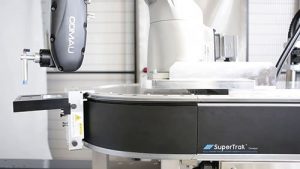
The speed and acceleration adapt to the respective production step. “This decoupling of product, process and mechanics opens up entirely new possibilities in flexibility and productivity.” Shuttle movement can even be used as an additional axis in CNC or robotics applications.
Reduced cycle times
When you factor in their dynamic acceleration, intelligent transport systems are able to cut packaging cycle times dramatically, sometimes even in half. “When you isolate the process from the mechanical design,” Tarozzi explains, “the motion profile is defined by each individual product rather than the physical constraints of the machine.”
Despite significantly increasing production speed, intelligent transport systems don’t require any changes to the packaging process itself. All they do is optimize the way items are transported between the steps in the process. “Essentially, intelligent transport systems allow you to synchronize asynchronous processes,” summarizes Tarozzi. “Many different production tasks with different cycle times come together to form a single, continuous process.”
Rapid changeover
“High production speed is great, but for the kind of flexible production and OEE improvements we’re talking about, you need to combine it with rapid changeovers,” notes Tarozzi. There are two ways that intelligent transport systems contribute to fast changeovers. On the one hand, they allow much of the changeover work to be mapped in software form. On the other, the magnetic movers are extremely easy to add and remove from the track.
High reliability
Intelligent transport systems can also greatly simplify a machine’s architecture. Eliminating motor-driven chains, belts and gears, they replace mechanics with simple, effective software profiles. The cost of maintenance shrinks dramatically.
Transparent costs
“Some companies are hesitant to try new technologies, because the implementation costs can be hard to predict,” explains Tarozzi. With B&R’s intelligent transport system, however, that’s not a problem. “The simulation tool we offer even takes synchronized robots into account.”
This makes it possible to simulate what the track will need to look like in order to implement the existing packaging process with an intelligent transport system. Machine operators can define exactly how long the track has to be and how many shuttles are needed. The simulation tool can even be used to perform virtual commissioning. “This makes it very easy to improve asset efficiency with intelligent transport systems,” concludes Tarozzi.