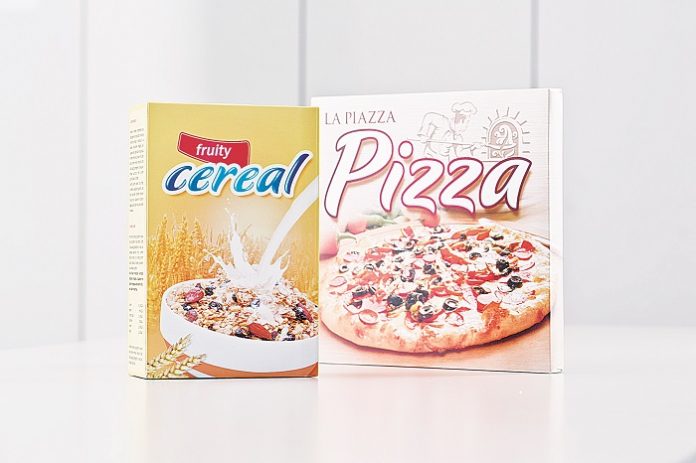
Thermal Inkjet (TIJ) has long been the dominant coding method within the pharmaceutical packaging industry. Unfortunately, the inability to print on any sort of plastic or glossy packaging coating made TIJ a no-go for most foods and consumer goods until now.
Videojet, in partnership with its Wolke business, has launched a game-changing technology that enables TIJ to consistently print and adhere to non-porous materials such as plastics, glossy cartons, foils and films. With the ability to mark most packaging materials, TIJ has for the first time become a viable choice for packagers of food and consumer goods looking for high resolution coding options.
The breakthrough came with the development of a new set of printing systems that are hardened to withstand solvent inks of the type used in Continuous Inkjet (CIJ) technology. Videojet TIJ technology now falls into two broad categories – aqueous and solvent. The former, which remain sun changed, is a set of printing systems designed to use the traditional water-based inks for marking on porous packaging materials. The new solvent category, on the other hand, features systems using inks that are able to dry on and adhere to, non-porous packaging materials. The solvent category is further divided into systems for weak solvents and hard solvents. Weak solvents, such as acetone and ethanol, are suitable for marking some non-porous materials like varnished cardboard cartons, while methy-ethyl ketone solvent(MEK) enables marking on more challenging plastics like films or hard plastics.
Benefits of thermal inkjet
The upshot is that producers of food and consumer goods can now unlock the benefits of thermal inkjet that were previously closed to them due to the limited adhesion of solvent inks. Chief among these benefits are the ability to produce high contrast codes combined with the cleanliness and simplicity of TIJ coders. Videojet’s thermal inkjet systems offer variable resolution up to 600 dpi, although 300 dpi (roughly four times that of CIJ) is often the preferred choice to optimize ink consumption. Furthermore, unlike laser or CIJ marking systems, Videojet thermal inkjet does not ‘scribe’ the code with a single marking point but instead uses a large number of tiny printing nozzles simultaneously. The result is that complex codes or multiple lines of text up to 50 mm (2 inches) in height can be coded without any impact on production speed or print quality.
Thermal inkjet also represents one of the cleanest and simplest to operate coding methods, which benefits production efficiency. TIJ systems feature a simple ink circuit with all ink contained in the expendable cartridge. With no ink pumps or filters, the operation of a thermal inkjet coder is clean, easy and reliable. Thermal inkjet is also an extremely cost-effective coding technology. While the cost of individual TIJ cartridges can be higher than the cost of CIJ consumables, the simplified operation, more efficient utilization of ink, reliability and enhanced print capabilities often result in an impressively low total cost of ownership.
Changing coding demands may also steer food producers and packers towards TIJ. Production teams face increased retailer pressure and a multitude of regulations demanding highly readable, content rich codes. They must also find ways to meet new requests from brand owners to print variable marketing codes, graphics, logos and even QR codes. These demands will prove too challenging for many older coding solutions, particularly analog coding methods such as hot stamp, roller coders, embossing wheels, legacy CIJ or situations where flexographic presses are marking static packaging elements that really should be variable or customizable. With its new technological capabilities, thermal inkjet coding looks set to play a key role in addressing these evolving demands.
Drew Weightman is global business unit manager at Videojet Technologies and Wolke. His primary responsibilities include business development and product management of Videojet’s Thermal Transfer (TTO) and Thermal Inkjet (TIJ) business units. Weightman has rich experience in the packaging and product identification sectors. Previously Weightman was a Danaher business system leader and vertical account manager with Videojet.