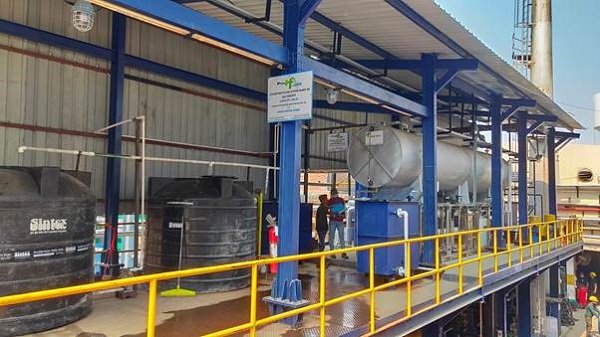
Driven by the aim of attaining water sustainability and reducing consumption and pollution, the Chemicals production unit of UFlex situated in Noida is now a Zero Liquid Discharge (ZLD) facility. ZLD is a strategic wastewater management system that ensures no industrial wastewater discharge into the environment, so UFlex has proactively adopted this technology to significantly reduce their freshwater consumption by recognizing the importance of wastewater purification and recycling. The Chemicals plant that has adopted ZLD technology has started saving close to 20 kilolitres of water a day.
UFlex’s Chemicals business develops eco-friendly, sustainable and food-safe compliant inks, adhesives, coatings and biodegradable packaging solutions such as primers, barrier, gloss and heat-seal coatings ecologically conscious with a lower carbon footprint. While UFlex has been making a conscious effort to bring down the use of water while developing these solutions, with the implementation of the ZLD technique, the plant has ensured that no liquid waste is eliminated and maximizes water usage efficiency.
UFlex Chemicals’ move towards a sustainable future
The zero liquid discharge Chemical plant uses a 100% supply of effluent treated water of Sewage treatment plant (STP) and Effluent treatment plant (ETP). It is subsequently treated through the combination of technologies like Membrane Bio-Reactor (MBR), Reverse osmosis (RO), and Agitated Thin Film Dryer (AFTD). The permeate good quality water, the final product derived, is thus reused in boiler feed, cooling tower makeup water, and fume hoods without being discharged into the municipal sewer, thereby putting the discarded water back to use. The rejected water is converted into solid waste residue through the evaporation process, which is in turn discarded as hazardous waste (as per the regulatory norms).
Expressing his delight on this new development, Rajesh Bhasin, Joint President, Chemicals Business at UFlex, commented, “At UFlex Chemicals, we are proud to announce that our Noida production has achieved the status of a zero liquid discharge facility. We have adopted this technology to contribute positively to the environment by considerably reusing and recycling wastewater to save groundwater consumption. It is a big move for us to reduce our overall water consumption and ensure that wastewater does not get discarded into the environment. We are working hard to follow the circular economy model at our facility and systematically implement environmentally conscious means so that we can conserve our natural resources for the future. Progressing further, we look forward to implementing the ZLD technology in our other production facilities to contribute towards a sustainable future.”