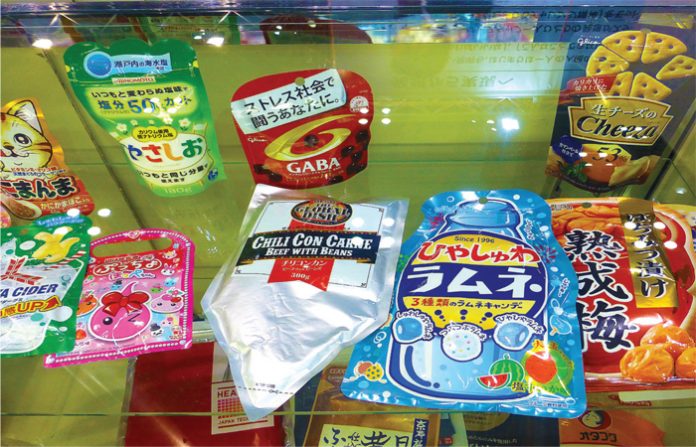
Pack designs that focus on convenience, hygiene, shelf-life and health benefits are winners in the eyes of Japanese consumers and some carry away industry awards, but Japan Pack also gives a rare glimpse of latest concepts in their exciting prototype phase.

Tokyo Food Machinery introduced a white CPET cook-in tray with a high grade barrier to extend shelf-life and ability to withstand temperatures up to 200°C. The lid is removed prior to cooking, to allow the ridged surface to circulate the heat, which also takes away any excess oil from food. In 2015 the Multivac subsidiary also launched in Japan a cook-in hermetic vacuum skinpack designed to go in a convection oven, made from a Teijin Dupont film.
Pouch in-line aseptic filling specialist Orihiro promoted its Onpack-VH100 machine for the production of gusseted pouches for energy gels, for example. These can be perforated for hanging display says Mark Tsuruta, senior managing director at Orihiro. Also shown was a ready-to-hang aseptic bagspout developed with Nippon Closures for Meiji-brand high protein liquid nutrition that the ill and frail elderly can self-administer – an award winner in the Japan Good Packaging Contest 2015.
A Japan Star President of Japan Packaging Institute Award went to the Meiji Meibalance Mini Cup by Atsugiplastics, Toppan Printing and Fuji Seal, designed for nutritional products. Mindful of the needs of ageing people and caregivers, the cup is formed from a resin that makes it easier to hold and has considered the width of the opened hand when grasping it. Other notable user-friendly features are its shaped over-cap, the marked point for easily inserting a straw and the straw itself which is comfortable for drinking.
The next crop of prime examples of accessibility, technical achievement, fitness for purpose and inventiveness in a range of product categories will be on display at Tokyo Pack from 4 to 7 October 2016 when the pack becomes the star of the show.
Technology targets zero defects on pouch filling lines
Toyo Jidoki introduces Englico’s Sealscope
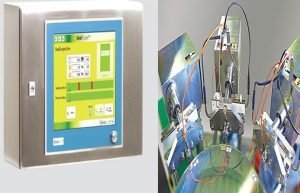
European process monitoring and seal inspection technology was seen at Japan Pack being put through its paces as an extra set of eyes in a complex pouch filling operation, with the goal of satisfying Japanese product manufacturers and customers with zero tolerance for defects. A cylindrical air column on one side of the Air Hold Pouch creates a handle for ease of pouring, a packaging idea that Toppan Printing developed with a major Japanese manufacturer of pre-made pouch filling machines, Toyo Jidoki. A pack concept first seen in the market in 2014 for Japanese sake can now be found in a personal care liquid application by Japanese brand Jewel Cosmetics.
The task of filling a pouch with air and liquid separately at the same time adds complexity to a process carried out on a standard TT-8D pouch filler. To help ensure the operation runs smoothly, which means achieving constant flow rates and total sealing integrity, the company has brought in the support of an advanced monitoring and inspection system. Toyo Jidoki is introducing Engilico’s SealScope for seal inspection and process monitoring to selected customers within its home market Japan and has mounted the system on a TT-8D to prove the concept. “The results look very promising,” said Takao Yamagishi, international sales director at Toyo Jidoki.
SealScope was developed by the bio-engineering department at the University of Leuven in Belgium. Engilico has the worldwide, exclusive license of the technology which is already applied in Europe by a number of international food producers including General Mills, Friesland Campina and Materne.
Next to Japan, Engilico sees the North American market as the next target territory for SealScope, its chief operating officer Jos Deschagt told Packaging South Asia. The self-learning, auto-calibrating system was developed as an aid to guard shelf-life by avoiding product inclusions and contaminations in the sealing area, typically in operations that run 24 x 7 said Deschagt, “It’s an extra set of eyes on the process. Is everything running as it is supposed to be?”
He added that SealScope can be set to different sensitivities, fine-tuned according to a company’s quality policy, taking into account the calculated ‘cost of quality.’ For instance, suppliers to the Japanese market set the bar at zero-tolerance for defects because end-customers expect only the highest quality, said Deschagt. The quality value to a company is linked to the cost of a product and the harm done if it is allowed to come into contact with oxygen and reaches the customer. Offered benefits are a higher output and better quality of product, and lower overall cost as a result of producing less waste, avoiding batch recalls, and upholding a brand’s reputation. Deschagt explained, “SealScope makes it possible to find optimal production speeds, to keep the production process optimized and to reject strongly deviating products.” He added that users have reported an increase in output of between 1% and 50%.
William Perell gets 2015 Japan Pack Innovation Award for Creative Technology
Swedish partner gives Pop-open pack first commercial break

Swedish flexible barrier packaging company Flextrus has recently signed the first cooperation agreement in Europe with PopPack LLC, American developer of ‘bubble in the seal’ technologies designed to open packs easily with help from a bubble filled with air that acts as a lever. The ‘pack with a pop’ concept was initially seen at Tokyo Pack 2014. It popped up again at Japan Pack 2015 in new prototype pack designs including flexible pour pouches in addition to the, so-called, ‘double bubble’ re-closable sachet, introduced the previous year.
This time the PopPack team led by technology inventor William Perell took away a 2015 Japan Pack Innovation Award for Creative Technology. Accepting the award from the Japan Packaging Machinery Manufacturers Association (JPMMA) Perell said it was an honour shared with PopPack’s Japanese prototype collaborators J-Film, Mitsubishi Plastics, Tokyo Foods Machinery Company/Multivac, OJI, and Kawashima Packaging Machinery whose stand staged live production demonstrations with flexible pouches using PopPack technology.
Scanpack in Gothenburg, Sweden was PopPack’s next trade show appearance and the first opportunity for Flextrus to exhibit the 2015 Packbridge Easy Open Award winner which is targeting food, health, personal care and household goods products in pouches and flexible and semi-rigid thermoformed packs. The audible pop is claimed to instantly engage the consumer and reassure that the pack has not been tampered with and once open it allows controllable dispensing and re-closure to help save waste, a key benefit according to its developers.
Get more from your pouch, says Totani
The flexible box pouch
Employ different shapes to distinguish the brand and make the most of a five-side, flat-bottomed box pouch for product marketing, says Totani Corporation, a top-ranked company in pre-made pouches with Pepsico among its customers. The bottom gusset of a box pouch, which uses a different film from the rest of the body, can be transparent to let shoppers view the contents or a solid color printed with a marketing message, explained Totani senior sales executive Toshio Yamaguchi.
Breakfast cereals are getting popular in Japan and the home-grown number 1 favourite brand Calbee is on the shelf in a Totani box pouch. Yamaguchi says it is an innovative, high-value product category in Japan and this winter consumers can buy a new Kellogg’s microwaveable granola cereal (in a 4-side pouch) that stays crunchy in hot milk, adapted to local tastes with dried sweet potato and pumpkin among the ingredients.
Totani showed a high-speed vertical fill form seal (vffs) machine with an upgraded Thomson diecut shaping system. In the new unit, which shape-cuts the film perpendicular to the film flow, the blade is easily changed allowing shorter lead times and reducing costs. A wide variety of possible designs includes a 3-side sealed pouch, zippered pouch, standup pouch and zippered standup pouch. The offered rate of output is between 140 to 200 pouches a minute (two-up, 400 pouches a minute). Yamaguchi reported that up to October, the upgraded model had four customers in Japan and two in the USA.