In our recent wide-ranging conversation with Trio Motion’s managing director Upendra Vanarase, we learned what differentiates this automation company from the others. Vanarase and his two other senior colleagues were educated at Imperial College London in the late 1980s and were reunited when Trio Motion was established in Pune in 2010. Meanwhile, he had gained extensive technology development and application experience working for more than a decade for a leading packaging automation company in Europe before moving back to the city where he was born and brought up.
In our conversation, Upendra Vanarase is quite transparent when he says that OEMs come to Trio for the toughest automation challenges. And he is equally clear that he wants to help the machine-building OEMs to make trend-setting machines in terms of efficiency and cost. When Trio started in Pune in 2010, Indian-made Vertical Form Filling and Sealing (VFS) machines functioned at 30 to 40 cycles a minute and the company was able to move its customers up to 70 to 90 cycles a minute. As the OEM’s competitors started to catch up, Trio was able to accelerate its partners’ machines to 120 cycles a minute.
In 2022, with food inflation driving the demand for even faster VFS machines, Trio motion took its trend-setting OEMs to a level of 160 cycles a minute. The only constraint on their speed is the weighers that the OEMs are currently able to source. Vanarase says, “In the whole supply chain we need to reduce the inefficiencies and costs.”
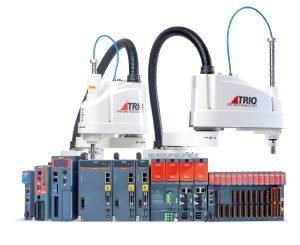
For him, this means not only the weighing, forming, filling, and sealing operations but also the feeding of the machines and removing their output, and putting it into the secondary or transport packaging. This is where Trio’s centralized motion control technology becomes more efficient not only in driving processes but also in terms of costs.
Since the centralized motion control of a VFS machine also contains the PLC it can operate the filling and operations that require sequential motion as well as the robots for feeding weigher and picking and placing the output. Vanarase says, “We need the high-speed machines because of the prevailing food inflation that is likely to continue. Currently, a snack manufacturer making potato chips has to decrease the product and increase the number of packs to sell the same tonnage of chips. However, to do this by buying one more machine at a low cost is not the solution. And for faster machines, you need full automation, which includes the secondary automation for handling and placing the packs in the secondary packaging.”
Trio has several installations using its single motion controller technology that are also equipped with secondary automation for handling higher output. Vanarase says, “It is inherently more economical because we don’t need two separate controller devices. We don’t need a separate controller for the pick and place or the robot. If our OEM has a bottling line, our controller can control the bottling machine and eight robots with a single centralized motion controller.”
While many OEMs and automation suppliers have a separate controller for the machine and the robot, Trio has a single centralized controller on a single board that controls both. Essentially it handles the multicore operations in which each software thread controls one aspect or device. Vanarase tells us, “There is a misconception in the market that motion control is more expensive and I don’t know where this has come from.”
With Trio’s technology, a single controller controls the in-feed and out-feed systems as well as the motion processes of the machine. This eliminates the need for separate controllers, HMIs, and a connectivity mechanism for synchronization and data exchange. For instance, in addition to managing the complete machine’s operation, the motion controller can manage a SCARA robot at the in-feed area and a pick and place or gantry system at the out-feed area. Comprehensive precision and efficiency come from the flawlessly integrated design and the OEM can cut expenses and increase its manufacturing and maintenance efficiency together with that of its customers.
“Using our controllers, the OEM’s machine is Industry 4.0 and IIoT ready, as well as PackML compatible as desired by major packaging end-users and factories,” says Vanarase. “With our controllers’ in-built IIoT capabilities, the OEM may connect Trio controllers to his cloud application via the open-source connectivity protocol OPC UA.”
OPC UA offers the necessary data exchange capabilities and includes the required security mechanisms. OPC UA can provide user authentication, access control, and certificate management, reducing cyber risk during data transfer. With Trio controls, the OEMs benefit from remote access, enabling Trio controls to be monitored from anywhere across the globe.