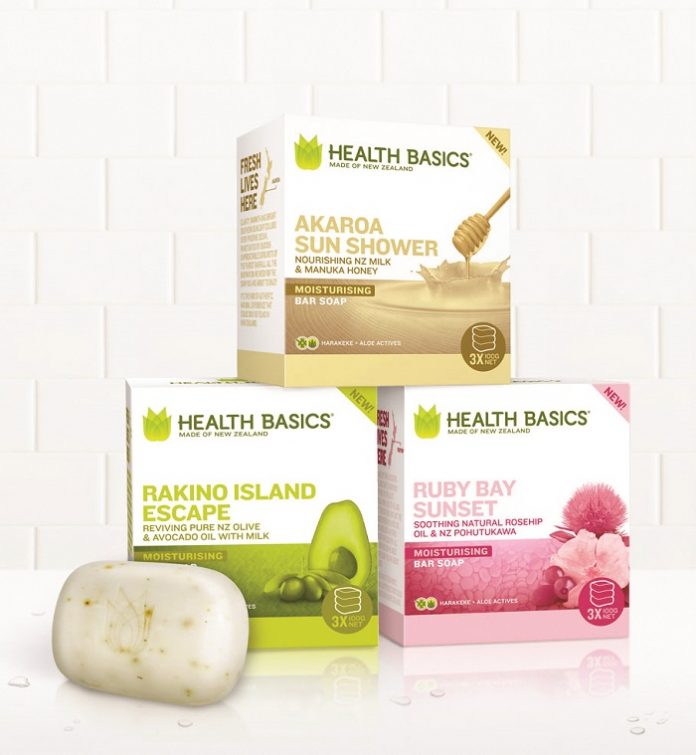
It should come as no surprise that if one were to place two operators (with equal experience) side by side, on the same machine, there likely would be two different makereadies. This is not to say that one would be better than the other, but rather each makeready reflects one person’s opinion as to how to minimize set-up time. In reality, one operator’s talent and or experience may fall into the category of ‘side seam’ style cartons, while another operator may be more familiar with the ‘4/6 corner’ style cartons . . . all valuable, but biased toward a particular set-up style.
With most plants running multiple shifts, operators will occasionally be asked to rotate and may have to set-up and run all of the folder/gluers in the department. Working in rotation subjects the operator to a wide variety of folding/gluing jobs and machines, which is ultimately good for both the operator and the company. However, the operator, during the rotation process, may not feel he/she has gained enough experience for a particular job ormachine. Many times an operatoris rotated off of a machine mid-way through a setup, increasing the set-up time for the next operator and potentially causing inconsistent product.
With this in mind, we have identified various productivity steps that would be beneficial in any operation. Keeping in mind the level of experience each operator has, these steps can help reduce the average set up time, increase the level of confidence and efficiency for the operator, and ultimately improve the quality and productivity on the products being folded and glued.
Step 1: Get organized
Begin each job by preparing all paperwork, raw material and job specific tooling while the current job is running. This avoids considerable machine downtime during change over. Purchase or build a portable rack (on wheels) and make all the machine accessories and parts accessible. Outline and label tooling and assemblies to mount on the rack. Having an outlined silhouette makes it very easy to see what is misplaced as well.
Assignanumber to each of the folder/gluers. Stampor label the parts for each machine with the same number…parts tend to wander over time. Place small tooling parts in labeled trays or bins with the same machine number and a tag of what’s in each tray or bin. One reason for lengthy set-up times is because operators can’t find the necessary small parts that are required and must look in various places, including other gluers. Ensure that all the tooling and accessories are readily accessible to each operator…across all shifts. Hold specific people accountable for the accuracy and condition of all makeready components.
Step 2: Pre-assemble tooling and forming components
By pre-assembling tools into complete units, a set-up will take far less time. The operator only has to find the right pre-assembled unit, install it in the appropriate pre-defined area, and then move on to the next kit. Store preset tooling that is common with most work in a consistent or common location. Don’t be shy . . .reconsider your entire layout . . . literally take steps out of the process.
Lock bottom forms and fingers can be assembled for each style and size carton. Four and 6 cornerforms can also be preassembled onto their unique mounting brackets. Tooling such as hold down wires and rails can be pre-assembled as well.Assign each a code orjob number. Create a KEY location on or around the machine for all makeready components, as
well as the wrenches, shims, screwdrivers, and more, that are needed to do the physical work.
Step 3: Record set-ups
Documenting all settings, starting at the feeder and progressing alltheway throughthe compressionsection,will assure reliable results and will also provide a starting place for the next operator in case of interruptions. An additional benefit would be a faster learning curve for new or less experienced operators.
If the volume of change oversdictates, you may want to have a makeready expert on your crew, floating across multiple machines and operators, familiarizinghim/herselfwithallthe
makeready documentation and record keeping. Most new folder/gluers have digital indicators that are located on the operator side of the machine, which are designed to provide accurate location information for each carrier. Recording the digital position of the carriers will greatly reduce the setup time on repeat orders.
Use a pre-printed form (attaching a previously run sample of the job) to record all of the settings and dimensional locations for carriers, feed gates, feed belts, back fold and lock
bottom forms, glue pots and guns. Using the scale typically installed across the feeder area, write down the location of each one ofthe board pile side guides. If possible, write down the inside or outside numbers from the reference location scale (tape) usually found in front of the pile side guides. Document a dimensional reference location for all of the
feed gates and feed belts. If the job requires backfolding, as in the case with 4 and 6 corner cartons, record the backfold finger locations, form locations, trigger device position, and any keypad control settings. Other important settings which are often overlooked are your glue function settings and gun locations. When installing assemblies, refer to the code numbers that were assigned as mentioned in Step #2.
Step 4: Keep a log: written. . .digital camera. . .video. . .whatever way is convenient
Develop standard makeready procedures based upon your various operators’ input. Consistent steps listed on a job checklist orlogbook lead to predictable and quick makereadies (changeovers), as well as constant increases in running speed. Keep anotebook to document any problems orunusual setups thatrequired special modifications to run a specific folding/gluing job. Keep in mind that the same operator may not run the same job twice. It is much easier to refer to notes that point out difficult areas than to take the time to solve the same problem over and over again.
Use a video recorder or digital camera to document the tooling and sequence of steps for repeatable makereadies. Take time to share this pictorial information with all the operators and reveal ways to take further time out of the set-up process. Having a department ‘setup’ PC may be a wise investment…keeping all logs, job set-up tool lists and even digital images.
Step 5: Have the right parts for the job
Working with the folder-gluer manufacturer, provide your operators sufficient tooling components to completely build each forming assembly. Forlong-term,repeatable contracts, itismore cost- effective to build pre-staged tooling into a job estimate. You can avoid the guesswork factorforthe extra time required in disassembling and reassembling components over and over again. As often as possible, try to use already organized and coded spare tools. It is far easier, quicker and consistent to bolt on a pre-planned folding form than to use the old ‘tape and bailing wire method.’
Step 6: Maintain your machine
The chance of unplanned downtime is decreased by routine preventive maintenance and thoroughly cleaning the machine on a regular schedule…glue accumulationis one of the most common areas left unattended. Regular preventative maintenance visits from the manufacturer or an experienced service company enables your maintenance personnel to work with a trained technician, ultimately picking up ‘tricks of the trade.’
Gluer operators and their assigned machinery perform better in a clean, organized environment. In addition, keeping the machine and work area free from dirt accumulation and clutter makes for a better impression when customers tour your plant. A folder-gluer that has routine operating interruptions can have a costly impact on the production schedule and future business.
Step 7: Don’t be afraid to ask questions
Technical support is a fundamental part of your relationship with your folder/gluer supplier. The manufacturer can help you optimize the use of your machine. With the right advice you can eliminate, for example, such simple but time wasting steps as operators pre-folding or’working the stock’ priorto putting it in the feeder.
Routine operator training should be provided by either the manufacturer or an independent skilled trainer. The collective talents of many experienced operators and exposure to many different folding/gluing jobs can be shared through the use of an independent full-time trainer. A good trainer adapts his experience to that of the inhouse experts. During the initial (new machine installation) training period, an operator may receive too much information during a short time period (information overload). Realistically, the operator cannot be expected to remember everything.
Machinery modifications are quite often an easy solution to avoid turning down certain work or forming the carton across multiple passes. Ask the manufacturer to help retrofit special devices to make your equipment far more flexible. Design creativity is part of any good manufacturer’s skill set.
Ask yourself this question: What will I do this year to improve the productivity, quality, and cost in ourfinishingarea?Evenmore important:WhatwillhappenifIdo nothing? You have to be persistent to get the most out of folder/gluer production. From greater efficiencies to increased operator confidence, every step taken, no matter how small, will ultimately effect your bottom line.
Reprinted with permission of the Foil Stamping and Embossing Association, InsideFinishing August/September 2002. Michael Erwin is president of American International Machinery which specializes in new and used folding carton and corrugated converting equipment and is the exclusive North American supplier of Signature brand folder-gluers and other convertingmachinery.AIMcanbe reached at 1-414-764- 3223 or visit: www. aim-inc. net