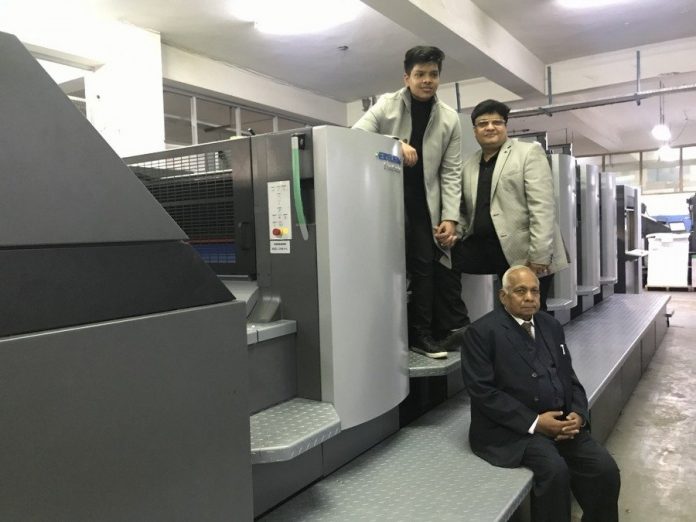
Sonipat-based Sain Packaging recently installed its first new Heidelberg Speedmaster CS 92 5-color sheetfed offset press. The CS 92 press with inline coater is be produced exclusively in Heidelberg’s modern plant in Shanghai. A pharma packaging printer and converter, Sain Packaging uses FBB board in the 23 x 36-inch size, which makes the CS 92 with its 37-inch capability optimal for cost efficiencies.
“We print quantities as few as 100 cartons on our offset presses,” says Sachin Gupta, director of Sain Packaging. “We could opt for digital for proofing, but the print quality of a digital press and an offset press are not the same. That is the reason we use an offset press even for sampling work.
Initially, Sain Packaging operated from a small plant in Burari in North Delhi and has now migrated to a 65,000 square foot plant in Sonipat. It started with a single-color Adast Dominant and, within six months, purchased its next press, a used double-color Heidelberg. After years of running second-hand Heidelberg presses, it bought its first new Heidelberg for reasons of quality and wastage.
Reduction in plate cost and wastage with new Heidelberg CS 92
“In the packaging industry for monocartons, no other brand is as renowned as Heidelberg. Nevertheless, we were in talks with other press suppliers, but we preferred Heidelberg because we are already Heidelberg users. We bought the CS 92 because more than 99% of our work is in the pharma segment, and almost all our printing work fits well in the 25 x 37-inch format of this press. We will save at least Rs 1.5 lakhs a month on the plate cost,” he adds. Earlier, Sain Packaging wasted the equivalent of nearly 6 lakh sheets of board each month, which Gupta is hoping will come down to less than 50,000 sheets.
Currently, Sain Packaging has three 5-color sheetfed offset presses with coater, one 4-color offset press, and four double-color presses. “We purchased the new Heidelberg press not to increase capacity but to improve our quality and reduce wastage, which in turn will help us meet our delivery timelines,” Gupta explains. Each month, Sain Packaging converts 400 tons of board in round the clock operation amounting to nearly Rs 4 crore.
New trends in pharma packaging
According to Gupta, the pharma industry is witnessing tremendous growth. He says that earlier, pharma companies preferred inferior quality boards, and now every manufacturer is quality competitive, demanding the higher priced quality board stocks. While in the past 15 years, most pharma customers asked only for lamination for increased shelf-appeal, they are now asking for haptics such as textured UV effects and Braille.
Bobst for braille
“For Braille, we’re in talks with Bobst and are planning to buy a new folder gluer with inline Braille embossing. Currently, we experience demand for Braille only for exports, and we hope to grow the overseas market. Although we export more than 40% of our production, I’m pretty sure that Braille will become mandatory in India as well,” says Gupta. On the post-press side, Sain Packaging has two Bobst die-cutters, two Maxima die-cutters, three folder gluers, and nearly seven manual die-cutters. Sain Packaging supplies cartons and inserts to pharma companies in Baddi, Roorkee, Paonta Sahib, and Amritsar. It also has a small corrugation set up for internal consumption. Sain Packaging aims to achieve a Rs 100 crore turnover in the upcoming financial year.