With an increased focus on sustainability and rising demand for greener products, businesses are increasingly shifting toward sustainable manufacturing processes. Chuk, a 100% compostable tableware brand and an initiative of Pakka Limited (formerly Yash Pakka), has been playing a key role in the manufacturing and distribution of bagasse-based containers.
To expand its idea of sustainability, the company recently tied up with the instant delivery service, Blinkit. “The market is moving towards delivery. So we, in alignment with the market, are focusing on the organized delivery market. Other than Blinkit, we are catering to Zomato, Haldiram, Wow Momos, and other brands,” said Satish Chamyvelumani, business head, Chuk.
The eco-ware products that are spill-proof, leak-proof, microwaveable, and freezer-friendly complete their life cycle within 90 days of composting, the company says.
Half of the workforce in Chuk’s Ayodhya plant, which operates with 75% renewable energy, comprises women. Chuk says its total carbon and water footprint amounted to 265.65 tonnes of carbon dioxide equivalent (the standardized unit of atmospheric impact of greenhouse gases) — which is 1310% less than plastic, 8733% less than plastic lined paper-based packaging and 5406% less than styrofoam packaging — and 49705.53 Kilolitre(kl) respectively with a water intensity of 24.64 KL/MT (kilolitre/metric tonnes), which is significantly lower than a gallon of water used to make a single paper bag, in FY 22-23.
“In alignment with the United Nations’ Sustainable Development Goals (SDGs), we source the raw materials from around a 200-km radius of the plant in Ayodhya, thereby increasing the economy of the local community,” said Chamyvelumani.
Boasting unique designs, which it claims are being imitated by other container manufacturing companies, Chuk strongly believes in its nationwide distribution network.
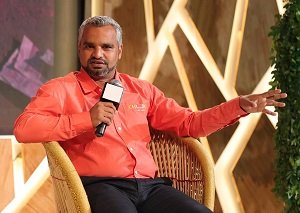
“We have 20 partners across the country. We are investing more in what we are good at, which is distribution and product design. We avoid becoming a jack of all trades,” Chamyvelumani said. He said they are collaborating with other pulp manufacturing companies, including two in Gujarat and two in northern India, and believes in the philosophy of ‘Simple strategy with great design and great distribution.’
The automation and semi-automatic machines in the plant not only work efficiently and sustainably but also take care of the waste generated by producing 100% compostable food containers.
“The final products that have irregularities in design are again pumped into the mills. The sludge that’s been generated as a byproduct is used to make egg trays. So nothing goes to waste from waste,” Chamyvelumani said. The company has a present production capacity of 1 million units per day and plans to ramp it up by 65-70%.
As far as the acceptance of sustainable products is concerned, Chamyvelumani believes the cost and people’s mindset are major hindrances to worldwide acceptability.

“Government bodies are playing their role well to promote sustainability by banning the use of plastics. But it’s the people who need to give a thought about the future generation,” says Chamyvelumani, regarding the curbs on plastics and the move towards a sustainable lifestyle.
“The smaller production size compared to the demand makes the cost higher. The cost will come down as more and more players come to the market,” said Chamyvelumani. He is pretty hopeful about the future and says, “The goal of 2030 is going to be a reality soon.”