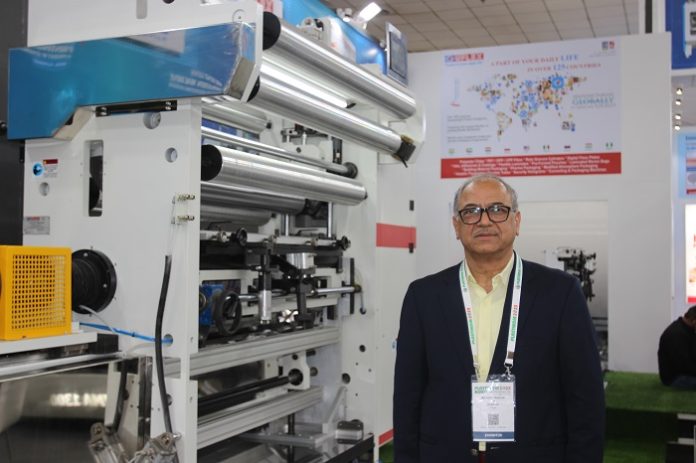
The engineering division of Uflex, one of India’s largest multinational flexible packaging and solutions companies, makes packaging and converting machines. At this year’s PlastIndia show in Delhi, the company highlighted its converting machines, slitter rewinder, and their time-saving automatic ink trolley changing system.
“We exhibited converting machines at the PlastIndia exhibition – we displayed a conventional solvent-less laminator, which has advanced technological features such as better breaking systems and better speeds. Then we got a slitter rewinder. Earlier, we were making EcoSlit with a speed of 450 meters per minute, and then we displayed EcoSlit at 600 meters per minute. We’ve had 600 meter per minute slitter rewinders before but they were very expensive for medium-sized converters,” Ajay Tandon, president Engineering Business & New Product Development, UFlex told Packaging South Asia.
Tandon said that for the first time in India, Uflex displayed its automatic ink trolley changing system, which is a new concept and of great value for customers. “When you change your printing job from job A to job B, it takes at least one-and-a-half to two hours. 35-40 minutes is the time required to change all the ink trolleys. If it is an 8-color printing machine, eight trolleys have to be changed one by one and it takes at least 30-40 minutes. It’s a labor-intensive job. With the automatic ink trolley changing system, one can change from job A to job B at the press of a button.”
He explained how once job A finishes and the printing cylinder is taken out, all eight trolleys will come out onto the railing and go to the side. The new trolleys that have already been prepared with a new printing cylinder and a new doctor blade will come and all eight trolleys will be simultaneously changed. “At least 80-85% of the time taken to change the trolleys will be saved. The changing work now takes just about five to six minutes.”
“If there are four job changes, running at about 300 meters per minute, you produce about 400-500 meters of extra printing material, which means about 1.2-1.5% of extra laminate per day. This comes to almost 35 to 40 tons of extra laminate per month. This extra value adds to your turnover even considering a margin of 10%. We calculated the ROI of this equipment for just about 10 to 12 months. Considering the life of a machine could be anywhere between 15-20 years, it’s a concept with some fantastic savings and a very good investment to make. It can go with the mechanical line shaft printing machines as well as the electronic line shaft printing machines,” he explained.
On the recent trends in the flexible packaging industry, Tandon said, “If you talk about flexible packaging, in this part of the world, 85% is gravure but gradually changing to CI-flexo. We now have about nine or 10 CI-flexo printing machines already in India and abroad, made by UFlex. Gradually people are going for CI-flexo presses because of their shorter runs or if they want to print a stretchable film like PE, as they can easily print on that and the cost of printing is also a lot lower. For gravure printing technology, the new trolley that we have produced is absolutely new and a path-breaking concept for saving on changeable jobs.”
“In India, we have a habit of going into a price war. I think it’s time to stop this price war. We should go to war but that of innovations, identifying new technologies. We should go to war or one step forward to bring in more high-end products,” he concluded.